3R Polymers, a manufacturer specializing in tailor-made PVC, PE, and other polymer compounds and masterbatches, advances its fire safety with cutting edge Halogen-Free Flame Retardant (HFFR) and Low Smoke Zero Halogen (LSZH) compounds, keeping in focus the modern infrastructure and smart city requirements of stricter fire safety protocols. The company is exploring synergistic flame-retardant systems, nano-additives, and polymeric blends that go beyond traditional halogenated and non-halogenated systems. Keeping sustainability a priority, 3R Polymers has launched several recyclable and halogen-free compounds, and are currently testing bio-based plasticizers and fillers. In an exclusive conversation with Wire & Cable India, Mr. Nitin Aggarwal, Director- Sales and Marketing of 3R Polymers Private Limited, shares insights on the HFFR and LSHZ compounds and talks about the next big thing- smart compounds.
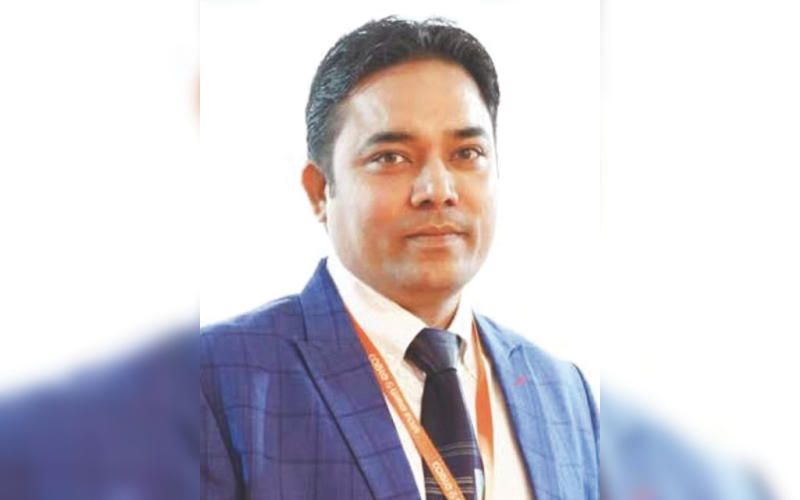
Wire & Cable India: As infrastructure projects like smart cities expand with stricter fire safety protocols, which of your current compounds are specifically engineered to meet cable manufacturers’ fire performance requirements, and what cable types or sectors are they most suited for?
Nitin Aggarwal: 3R Polymers has developed a specialized range of Halogen-Free Flame Retardant (HFFR) and Low Smoke Zero Halogen (LSZH) compounds tailored to meet the rigorous safety and performance demands of modern infrastructure and smart city projects. Our compounds are extensively used in power cables, control cables, and data communication cables deployed in high-density public and commercial spaces, where fire safety and reduced emission characteristics are critical.
WCI: How do your fire-retardant compounds perform in high-speed extrusion or when used with crosslinking processes like e-beam or silane grafting?
NA: Our compounds are optimized for high-throughput manufacturing processes and show excellent performance in high-speed extrusion environments. They are engineered to maintain consistency and uniformity in crosslinking systems, including e-beam and silane grafting, ensuring that throughput doesn’t come at the cost of insulation integrity or surface finish.
WCI: What breakthroughs have you made to help cable manufacturers in reducing smoke density and toxicity without compromising mechanical integrity in LSZH compounds?
NA: We’ve made significant strides in balancing fire performance with mechanical robustness. Our advanced LSZH formulations have achieved lower smoke density and toxicity levels while maintaining tensile strength, elongation, and thermal stability. Proprietary synergistic blends in our formulations allow us to meet EN 50268 and IEC 61034 standards without compromising physical properties.
Watch: Top Cable Companies in India
WCI: Are your compounds developed and certified in direct response to cable manufacturers’ compliance needs for CPR Euroclass B2ca, C1A, or other international fire safety standards? How do you support them in regional compliance efforts?
NA: Our product development is closely aligned with both international and domestic standards. We offer UL-, CE-, and BIS-compliant compounds and provide full technical documentation and testing support to help clients navigate regional compliance hurdles. Our in-house R&D and regulatory teams actively monitor updates like the recent revisions in IS 7098 to ensure our offerings stay ahead of the curve.
WCI: Can you share a recent example where you developed or customized a fire-retardant compound for a cable manufacturer’s specific project or tender requirement?
NA: We recently collaborated with a major cable manufacturer bidding for a metro rail tender that required stringent flame retardancy and UV resistance. Our team developed a tailored LSZH compound meeting both the mechanical and flammability requirements, which successfully passed third-party testing and was integrated into the final cable design submitted for the project.
WCI: Advanced material science applications are beginning to appear in commercial fire-resistant formulations. Are you working with nano-fillers, intumescent systems, or synergistic blends that go beyond traditional ATH-based flame retardants, specifically to enhance fire resistance in cables?
NA: We are exploring synergistic flame-retardant systems, nano-additives, and polymeric blends that go beyond traditional halogenated and non-halogenated systems. These innovations aim to offer enhanced fire performance, improved insulation characteristics, and extended service life, especially in harsh environments like tunnels, offshore platforms, and renewable energy setups.
WCI: Circular economy principles are reshaping material selection processes throughout the value chain. How are you addressing environmental concerns in fire-retardant compounds—whether through halogen-free formulations, recyclable blends, or bio-based additives?
NA: Sustainability is a key pillar of our R&D strategy. We have launched several recyclable and halogen-free compounds, and are currently testing bio-based plasticizers and fillers. These developments aim to reduce the environmental footprint without compromising performance, thereby supporting both OEMs and cable manufacturers in meeting green building and eco-labelling standards.
Also Read: Powering Progress: Mixer’s Tailored Compounds for the Future of Medium Voltage Insulation
WCI: The gap between laboratory certification and field performance remains a discussion point in industry forums. What kind of feedback do you typically receive from cable manufacturers regarding fire performance in terms of what works well, and what still needs improvement?
NA: Manufacturers appreciate our compounds’ balance between processability and end-use performance. Feedback often highlights superior extrusion stability and reduced die drool. However, areas like further lowering processing temperatures without affecting fire properties continue to be an industry-wide goal, and we’re actively working on it.
WCI: From a compounder’s perspective, what’s the next big leap needed in fire-safety material science to meet the cable industry’s evolving needs?
NA: We believe the next major leap lies in developing smart compounds—materials that respond to environmental stress (like heat or moisture) with adaptive performance characteristics. Integrating sensor-compatible or self-healing properties could revolutionize cable longevity, safety monitoring, and predictive maintenance capabilities in critical infrastructure.
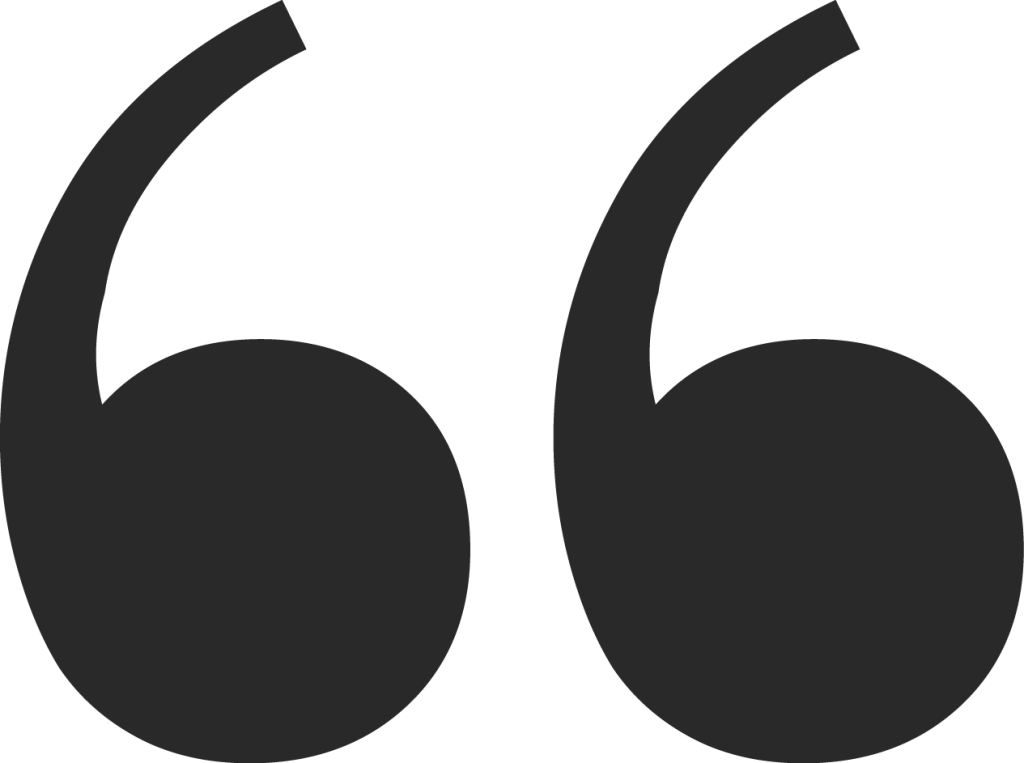
Our advanced LSZH formulations have achieved lower smoke density and toxicity levels while maintaining tensile strength, elongation, and thermal stability. Proprietary synergistic blends in our formulations allow us to meet EN 50268 and IEC 61034 standards without compromising physical properties.