As infrastructure projects and smart cities expand with stringent safety and performance standards, Duplast is supporting cable manufacturers with innovative additive and flame retardant solutions. Specializing in high-performance PVC additives and halogen-free flame retardants, Duplast offers engineered compounds that meet both domestic and global regulatory requirements. Product lines, including advanced Ca/Zn stabilisers, SFR & SAT series Flame retardants (Antimony Trioxide replacement) and FGLS series smoke suppressants, are developed to produce high temperature performance cables, improve flame retardancy and to reduce smoke density of PVC cable compounds. Designed for compatibility with high-speed extrusion and crosslinking technologies like e-beam and silane grafting, Duplast solutions are tailored to meet the needs of modern cable production across sectors such as power, telecom, smart infrastructure, and green buildings. In an exclusive conversation with Wire & Cable India, Mr. Siddharth Chopra, Director, Duplast highlights the nuanced and varied scope of flame retardant compounds.
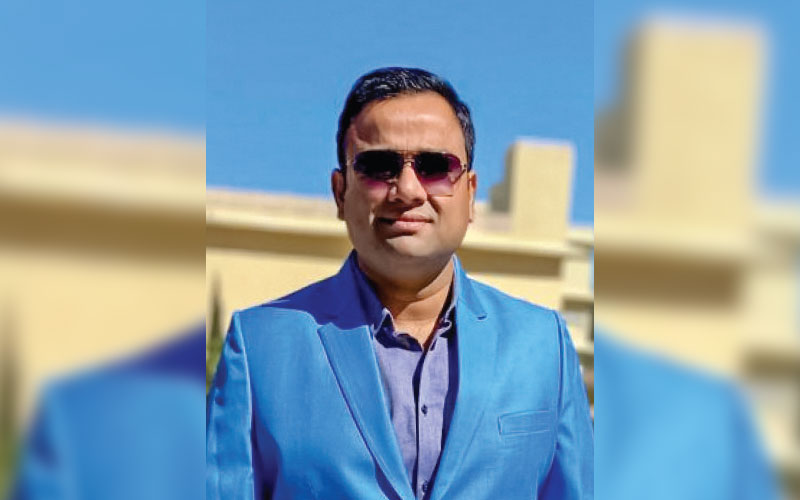
Wire & Cable India: As infrastructure projects and smart cities expand with stricter safety protocols, which of your current compounds are specifically engineered to meet cable manufacturers’ enhanced performance requirements, and what cable types or sectors are they most suited for?
Siddharth Chopra: As a manufacturer of additives for PVC compounds and flame retardants, we are committed to providing advanced solutions that help cable manufacturers meet these elevated standards for safety, durability, and functionality. Our product portfolio is designed to support a wide range of cable types and industry sectors.
Fire safety is a key focus area, particularly in public and high-density environments, to meet these needs, we offer halogen-free flame retardants (HFFRs) tailored for low smoke zero halogen (LSZH) cable compounds. These include finely engineered metal hydroxides such as Aluminum Trihydrate (ATH) and Magnesium Hydroxide (MDH), along with synergistic phosphorus-based additives. These compounds are optimized for thermal stability, effective flame suppression at lower loadings, and ease of processing. They are ideal for LSZH power cables, communication cables like Cat5e/Cat6 and fiber optic, and building wires used in sectors such as transportation hubs, hospitals, data centers, and smart buildings– places where minimizing toxic smoke and flame spread is critical.
We also provide advanced smoke suppressant additives for traditional PVC cable formulations where full LSZH systems may not be feasible. These include SFR & SAT series Flame Retardants, Zinc Borates and FGLS series smoke suppressants that enhances char formation and reduce smoke density during combustion. These are particularly suited for PVC-insulated and sheathed cables used in commercial buildings, residential projects, and various industrial settings where enhanced fire safety is needed without the higher cost of LSZH systems.
To support long-term performance and reliability of cables in harsh environments, we offer high-performance heat stabilizers, especially lead-free calcium-zinc (Ca/Zn) systems. These stabilizers ensure excellent thermal stability, color retention, and processing performance in PVC compounds. They are essential for cables used in smart grid infrastructure, renewable energy installations (such as solar and wind), automotive wiring, and general building and construction. These applications require cables that maintain integrity and function over extended periods and under fluctuating environmental conditions.
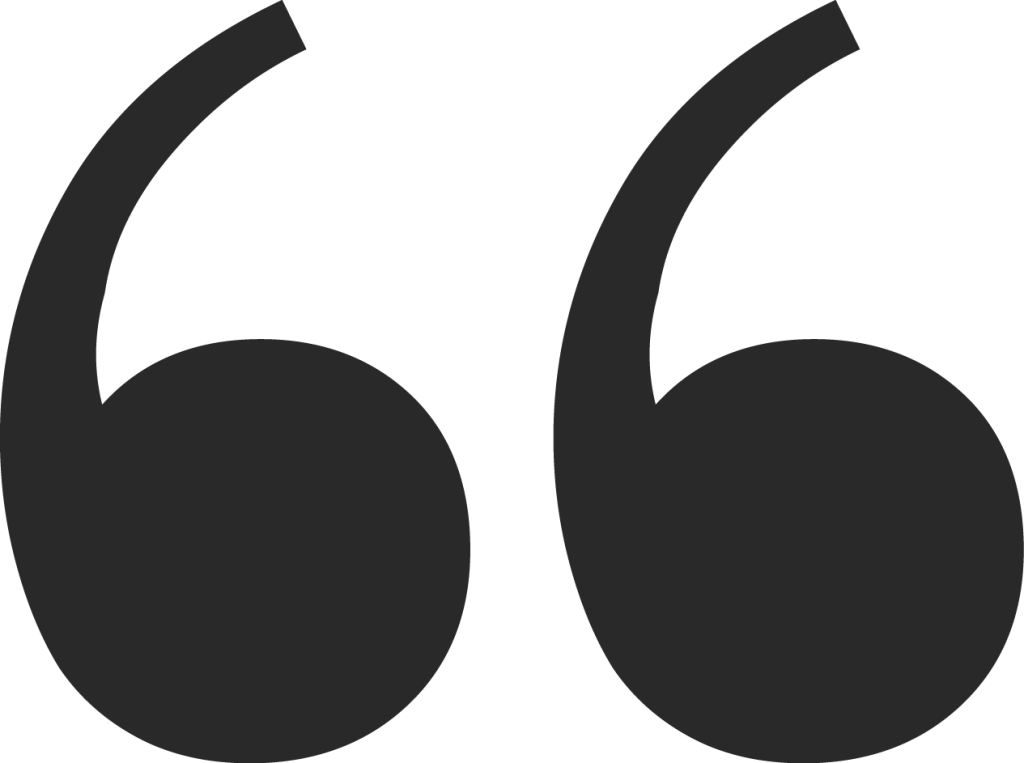
We provide Flame Retardants and advance smoke suppressant additives for traditional PVC cable formulations where full LSZH systems are not feasible. These include SFR & SAT series Flame Retardants, Zinc Borates and FGLS series smoke suppressants that enhances char formation and reduce smoke density during combustion.
Watch: Top Cable Companies in India
WCI: Cable manufacturers report varying levels of success with newer compounds in high-speed production environments. How do your compounds perform in high-speed extrusion or when used with crosslinking processes like e-beam or silane grafting?
SC: As a manufacturer of additives and flame retardants, we engineer our compounds to excel in high-speed cable production and advanced crosslinking processes.
High-Speed Extrusion Performance: Our PVC additives include optimized lubricants and processing aids that significantly reduce melt viscosity and improve melt homogeneity, allowing for higher output rates and superior surface finish without compromising dimensional stability. Our advanced heat stabilizers ensure thermal integrity, preventing degradation even under intense shear and heat, crucial for maintaining properties at speed.
For HFFR compounds, we address inherent processing challenges (high melt viscosity) through surface-treated mineral flame retardants (ATH, MDH). These treatments enhance dispersion, reducing melt viscosity and improving flow, which facilitates faster extrusion and minimizes defects like die swell. We also offer specialized processing aids for HFFRs to ensure smooth, high-speed processing.
Crosslinking Processes (E-beam & Silane Grafting): Our compounds are designed for seamless integration. For e-beam crosslinking, our polyolefin-based HFFRs are inherently suitable, as this process avoids high temperatures that could prematurely decompose flame retardants. Our antioxidant packages are formulated to provide thermal stability without inhibiting efficient e-beam curing, ensuring full flame retardancy and enhanced properties like higher temperature resistance.
For silane grafting (moisture crosslinking), our stabilizers and additives are meticulously balanced to manage reactivity. They prevent premature crosslinking (scorching) during high-speed extrusion while ensuring efficient moisture-induced curing post-extrusion. We ensure compatibility with silane catalysts, allowing for controlled.
WCI: What breakthroughs have you made to help cable manufacturers in reducing smoke density and toxicity without compromising mechanical integrity in LSZH compounds?
SC: As a manufacturer of flame retardant, we have been continuously developing products which have helped in reducing smoke with low addition levels. We have different grades in our FGLS series of smoke suppressants which help in reducing smoke considerably at very low addition levels.
Also Read: Universal Polychem’s Engineered Compounds Enhance Extrusion and Crosslinking Efficiency
WCI: Global export markets demand varying certification standards while domestic requirements continue evolving. Are your compounds developed and certified in direct response to cable manufacturers’ compliance needs? How do you support them in regional compliance efforts?
SC: We are a manufacturer of additives and flame retardants. We do provide customised additives for specific applications and help compounders with formulation for manufacturing of compounds with both domestic and export requirements.
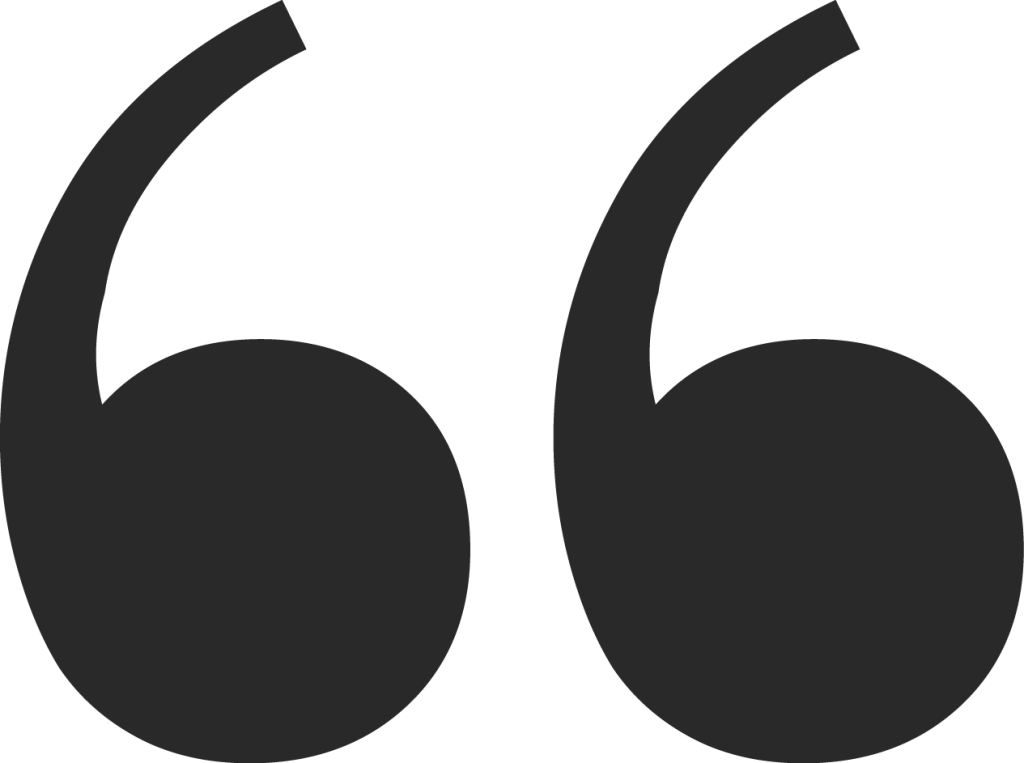
To support long-term performance and reliability of cables in harsh environments, we offer
high-performance heat stabilizers, especially lead-free calcium-zinc (Ca/Zn) systems.