In an exclusive interview with Wire & Cable India, Mr. Adriano Vezzani, R&D and Technical Manager Compounding, Finproject S.p.A, delves into the company’s advanced compound solutions tailored for evolving infrastructure demands. He highlights the performance of XLPO, HFFR, and XLPO-HFFR compounds in high-speed extrusion and crosslinking processes. A key aspect of Finproject’s innovation lies in its use of co-kneader technology for compound processing. He emphasizes Finproject’s commitment to global and regional compliance, supporting cable manufacturers in navigating certification standards. Additionally, Vezzani shares insights into collaborative material development for specific project requirements and the biggest challenge posed by stringent chemical regulations.
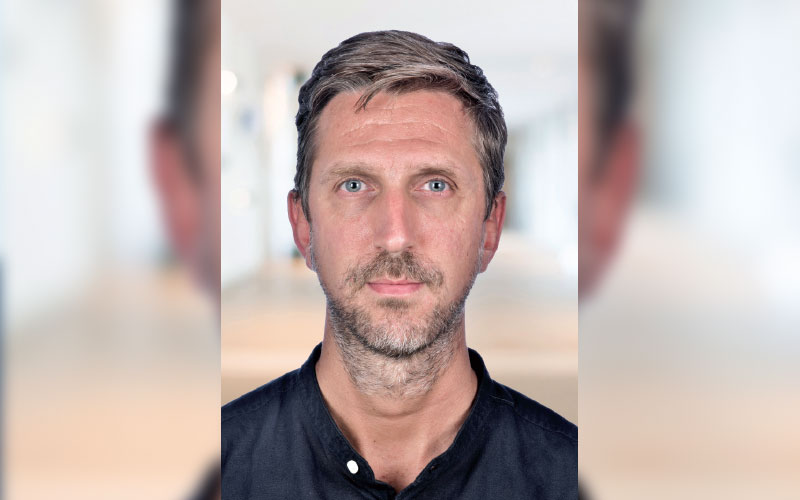
Wire & Cable India: As infrastructure projects and smart cities expand with stricter safety protocols, which of your current compounds are specifically engineered to meet cable manufacturers’ enhanced performance requirements, and what cable types or sectors are they most suited for?
Adriano Vezzani: Our product range includes XLPO, HFFR, and XLPO-HFFR compounds, which, used individually or in combination, are suitable for the most demanding applications in terms of flame retardancy, oil resistance, safety from fumes and toxicity, as well as superior electrical and thermal properties.
Cogegum, Polidan, and Polidiemme grades have been used for over 40 years in the wire and cable industry for building and construction, onshore and offshore applications, railway systems, renewable energy, automotive, and electric vehicles (EVs).
WCI: Cable manufacturers report varying levels of success with newer compounds in high-speed production environments. How do your compounds perform in high-speed extrusion or when used with crosslinking processes like e-beam or silane grafting?
AV: Finproject’s state of the art compounding technology for thermoplastic and ambient-curable compounds ensures the highest quality and consistency during cable extrusion.
At Finproject, even during the development of a new cable compound, the extrusion testing phase and qualification play a central role in guaranteeing optimal performance during large-scale cable production.
Watch: Top Cable Companies in India
WCI: What breakthroughs have you made to help cable manufacturers in reducing smoke density and toxicity without compromising mechanical integrity in LSZH compounds?
AV: We have worked to evolve compound formulations alongside the use of exceptional mixing technologies, such as the co-kneader. This ensures excellent distributive mixing and optimal distribution of an ever-increasing quantity of high-quality, flame-retardant fillers.
Following this approach, in recent years, our product range has been expanded with materials that offer outstanding mechanical properties while also improving electrical and fire-resistant characteristics. All of this is achieved without compromising low smoke emissions and low toxicity.
WCI: Global export markets demand varying certification standards while domestic requirements continue evolving. Are your compounds developed and certified in direct response to cable manufacturers’ compliance needs? How do you support them in regional compliance efforts?
AV: Our compounds are developed with a strong focus on both global and regional compliance requirements. At Finproject, we work closely with cable manufacturers to understand the specific certification standards they must meet such as UL, IEC, RoHS, REACH, CPR, and local regulations in key export markets. Our R&D and regulatory teams continuously monitor updates to these standards, to ensure our formulations are aligned with evolving compliance needs.
We support our customers through ongoing training, close collaboration, and constant updates to our technical and sales teams. This ensures we provide not only compliant materials but also reliable guidance in navigating changing regulatory landscapes.
WCI: The tender specification process for infrastructure projects often requires collaborative material development. Can you share a recent example where you developed or customized a compound for a cable manufacturer’s specific project or tender requirement?
AV: A recent example is the development of a flame-retardant HDPE sheathing for MV, HV, and EHV cables, designed to meet the requirements of IEC 60840, commonly used in high-performance power transmission. This compound was tailored for demanding installation environments, incorporating features such as enhanced UV resistance, improved abrasion resistance, and superior environmental stress crack resistance (ESCR)—all based on direct input from our key customers.
WCI: Advanced material science applications are beginning to appear in commercial cable formulations. Are you working with advanced technologies or synergistic blends that go beyond traditional compounds, specifically to enhance performance in cables?
AV: At Finproject, we continuously explore advanced technologies and synergistic polymer blends that extend beyond conventional compound formulations, with the objective of enhancing cable performance across a wide range of applications. Our development philosophy is guided by an uncompromising commitment to safety, regulatory compliance, and alignment with customer specifications.
To ensure we remain at the forefront of material innovation, we maintain ongoing collaborations with key suppliers, regularly participate in industry conferences, and foster partnerships with research institutions and universities. As a member of the Eni Versalis group, Italy’s leading chemical company, we benefit from a robust innovation network that supports our continued leadership in the wire and cable sector.
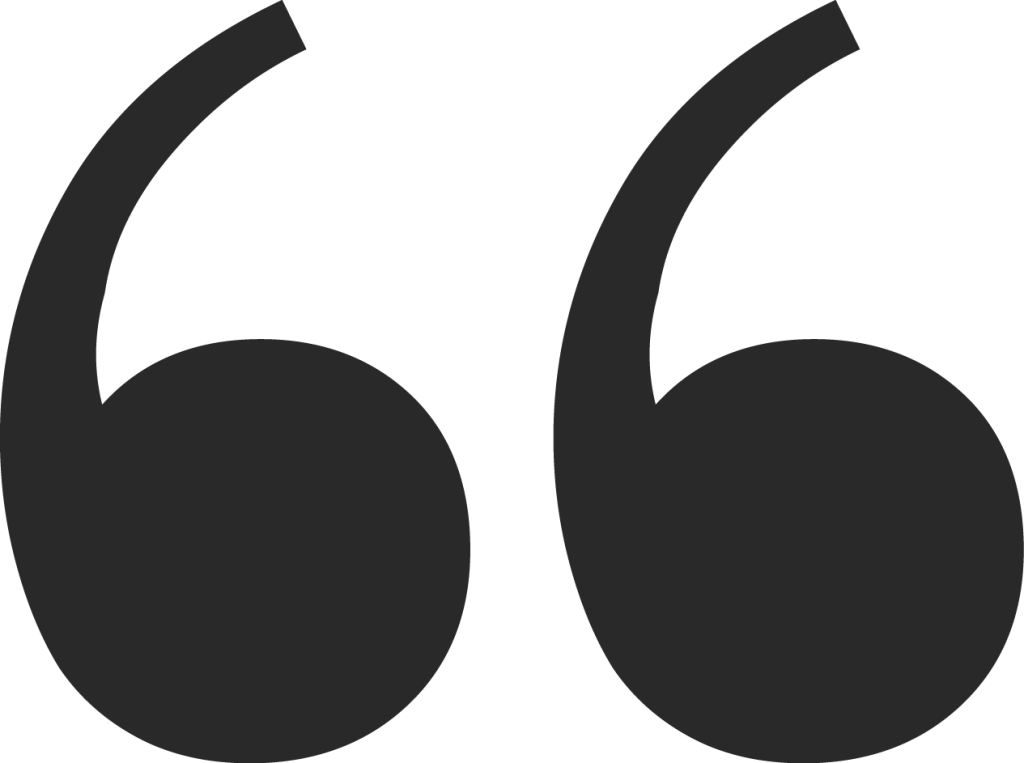
One of the most significant challenges is the need to align high-performance product development with increasingly stringent chemical regulations such as REACH (in the EU, Korea, Turkey) and CMRS in India.
WCI: Circular economy principles are reshaping material selection processes throughout the value chain. How are you addressing environmental concerns in compounds—whether through halogen-free formulations, recyclable blends, or bio-based additives?
AV: Our strategy in the circular economy is multi-pronged. It begins with the selection and reuse of our internal by-products in new advanced formulations, along with the adoption of polymers sourced from bio-circular and bio-based feedstocks. Additionally, we are proposing new products, such as XLPO, containing up to 50% recycled polymers from post-consumer waste.
WCI: The gap between laboratory certification and field performance remains a discussion point in industry forums. What kind of feedback do you typically receive from cable manufacturers regarding performance in terms of what works well, and what still needs improvement?
AV: Most cable producers, besides the standardized tests, have their own qualification procedures and type tests to go beyond certifications and to be ever close to what the field installation really needs. The challenge is to be able to adopt all these tips during the compound formulation and cable design to match both certification and improved cable performances.
Also Read: Taprath Elastomers Paving the Way for Next-Gen Flame-Retardant Cable Solutions
WCI: Material science innovation continues driving performance advances while addressing processing challenges. From a compounder’s perspective, what’s the next big leap needed in material science to meet the cable industry’s evolving needs?
AV: One of the most significant challenges is the need to align high-performance product development with increasingly stringent chemical regulations such as REACH (in the EU, Korea, Turkey) and CMRS in India, which aim to safeguard human health and the environment. Addressing this challenge will require strong, coordinated efforts among all stakeholders- from raw material suppliers and compounders to cable manufacturers and regulatory bodies. The shared objective must be to develop and bring to market- cables that meet high standards of quality, innovation, and technological sophistication, while continuously enhancing their safety and environmental profile.
This evolving regulatory landscape calls for a proactive and collaborative approach to ensure that the industry not only remains compliant but also continues to lead in sustainable and responsible innovation.
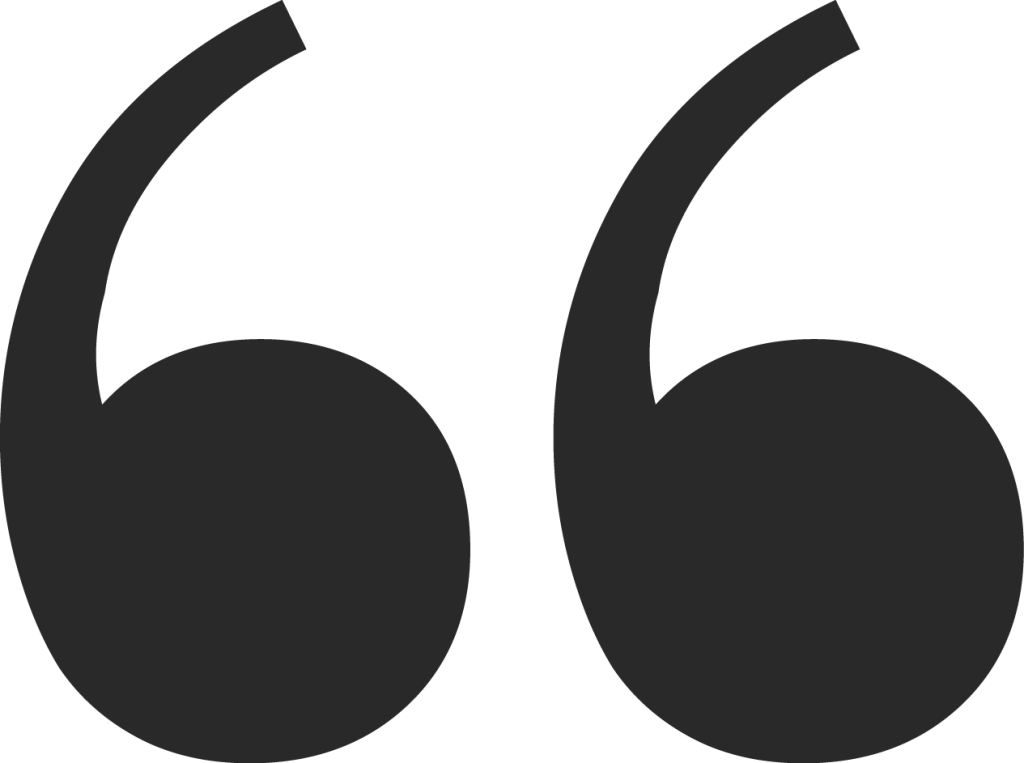
Our product range has been expanded with materials that offer outstanding mechanical properties while also improving electrical and fire-resistant characteristics.