Celanese, a global chemical and specialty materials company is driving innovation in fire-safety, halogen-free cable materials with solutions like Vamac® AEM, Hytrel® TPC-ET, and Santoprene® TPV. Designed for high-speed processing and fire performance demands, these materials support infrastructure projects with low smoke, less toxicity, and strong mechanical integrity. Backed by global R&D and sustainable options, Celanese addresses evolving industry, regulatory, and environmental requirements. In an exclusive interview with Wire & Cable India, Mr. Nainesh Shah, Application Development Leader, E&E Clean Energy– India and Mr. Luis Zalamea Ph.D., E&E Clean Energy– EMEA, share their insights about the specific products.
Wire & Cable India: As infrastructure projects like metro rails and smart cities expand with stricter fire safety protocols, which of your current solutions are specifically engineered to meet cable manufacturers’ fire performance requirements, and what cable types or sectors are they most suited for?
Nainesh Shah: Vamac® AEM and Hytrel® TPC-ET elastomers are uniquely suited to fulfil the stringent requirements of the railway industry. Excellent temperature and chemical resistance along with low smoke flammability performance make them ideal raw materials for such specialty compounds.
Vamac® Dipolymer such as Vamac® AEM DP or Ultra DX (VMX2122) are usually preferred for HFFR compounds. They provide more stable compound viscosity and better heat aging properties. Celanese has decades of experience in formulations suitable for the most demanding applications like HEV / EV battery cable, rolling stock cable, airplane cable, mining cable, off-shore oil platform cable, marine cable, military applications (e.g. submarine, fighter plane) etc.
Watch: Top Cable Companies in India
WCI: How are you leveraging halogen-free flame retardants, mineral fillers like ATH or MDH, or phosphorus-based systems in your fire-safe formulations to align with cable manufacturers’ processing capabilities and fire safety needs?
Luis Zalamea: ATH and MDH are fully compatible with Vamac® AEM formulations and have decades of excellent track record in the railway sector. Our formulations and raw material recommendations have been among the first ones to be considered as halogen free solutions and in some cases as viable alternatives to fluoropolymers. We are also proud to be among the first ones to offer Halogen free Santoprene® TPV, which offers a cost-effective alternative to HFFR TPU in certain applications where those are over specified.
Santoprene® TPVs are designed to meet customer needs for evolving electrical applications that must comply with the latest regional standards and directives. They meet emerging market trends, such as halogen-free flammability, simplified designs, enhanced electrical performance, increased flexibility, improved processing and lower cost compared to thermosets. Offering customers a significant competitive advantage, Santoprene® TPV facilitates ongoing innovation across the value chain.
WCI: Cable manufacturers report varying levels of success with newer fire-resistant compounds in high-speed production environments. How do your fire-retardant solutions perform in high-speed extrusion or when used with crosslinking processes like e-beam or silane grafting?
NS: Vamac® AEM has a proven track record in the industry as being very efficient in processability whether it is via chemical (i.e. peroxide) or physical (i.e. e-beam) crosslinking. They perform outstanding in tough scenarios of thin wall and high-speed extrusion, whilst maintaining the desired end properties. As for Santoprene® TPV, it combines the processability of thermoplastics (PP) with the performance of rubber (EPDM). Hytrel® TPC-ET has been a recognized brand in thermoplastic elastomers for thin wall extrusion, suitable for data transmission and optical fiber cables.
WCI: What breakthroughs have you made to help cable manufacturers in reducing smoke density and toxicity without compromising mechanical integrity in LSZH compounds?
LZ: We have consistently delivered top mechanical properties along with low smoke toxicity and flame retardancy. In this regard, we can provide a wealth of formulation expertise to help customers achieve their requirements.
WCI: Are your materials developed and certified in direct response to compound manufacturers’ compliance needs.
NS: Being a global company, we pride ourselves on having a world-class product stewardship team who is constantly keeping our materials in compliance with the most stringent regulations across regions. Most of our certifications, however, happen at customer level since they are directly related to cable designs and architectures.
WCI: Advanced material science applications are beginning to appear in commercial fire-resistant formulations. Are you working with nano-fillers, intumescent systems, or synergistic blends that go beyond traditional ATH-based flame retardants, specifically to enhance fire resistance in cables?
LZ: We typically do not disclose the specific components we test but suffice it to say that we have a global network of researchers that are constantly keeping us abreast by testing the latest innovations in flame retardant raw materials and additives.
WCI: Circular economy principles are reshaping material selection processes throughout the value chain. How are you addressing environmental concerns in fire-retardant compounds—whether through halogen-free formulations, recyclable blends, or bio-based additives?
NS: We have consistently demonstrated having a broad portfolio of halogen free solutions on Vamac® AEM, Hytrel® TPC and Santoprene® TPV. For the time being all of our Hytrel® can be purchased in Eco-B format, which guarantees up to 70% renewable content and we are constantly watching market interest and adoption rates to further enhance our offering in this regard.
Also Read: Finproject’s Co-Kneader Mixing Technology Enhances Compound Performance
WCI: What kind of feedback do you typically receive from your clients regarding fire performance in terms of what works well, and what still needs improvement?
LZ: We have been very active in bridging this gap by means of extensive analytical testing, starting a few years ago with cone calorimeter measurements, which have since then guided our raw material and compound development efforts. We put all this infrastructure at the service of our customers to help them achieve their goals faster and more effectively, thereby being first to market.
WCI: Material science innovation continues driving performance advances while addressing processing challenges. What’s the next big leap needed in fire-safety material science to meet the cable industry’s evolving needs?
NS: We typically do not comment on our development pipeline but suffice it to say that we currently have active projects in the flame-retardant platform aiming at applications spanning automotive, railway and data transmission.
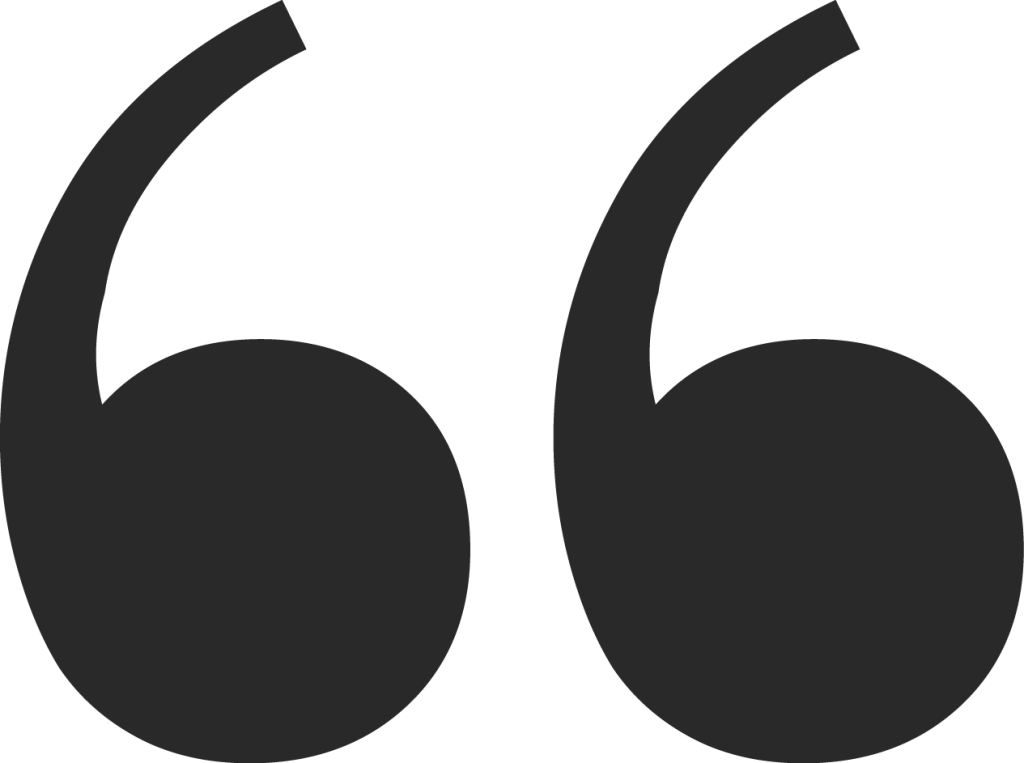
We have always focused not only on developing compounds for emerging needs of industry but also to achieve certification so that our customers are well enabled to compete at the global stage.