Teknor Apex, a custom compounder, is addressing fire safety with advanced compounds such as Halguard® LS HFFR, Flexalloy® PVC elastomers, and FireGuard® PV, engineered to deliver exceptional fire safety, mechanical strength, and processing efficiency. The company is also driving sustainable innovation through solutions like BioVinyl® and Cycle-Tek®, while leveraging AI-driven R&D to accelerate material development. In an exclusive conversation with Wire & Cable India, Mr. Mike Patel, Director of Marketing, Teknor Apex, shares the need for next-gen materials that combine sustainability, safety, and high-speed processability– pointing to the future of compounding.

Wire & Cable India: As infrastructure projects and smart cities expand with stricter safety protocols, which of your current compounds are specifically engineered to meet cable manufacturers’ enhanced performance requirements, and what cable types or sectors are they most suited for?
Mike Patel: Teknor Apex offers advanced compounds that help cable manufacturers meet evolving fire safety standards. Our Halguard® low smoke, halogen-free flame retardant (LS HFFR) compounds are suited for building, transit, and industrial cables where low toxicity and smoke suppression are essential. Flexalloy® PVC elastomers offer excellent low-temperature flexibility and toughness, making them ideal for demanding environments such as industrial automation and electric vehicle charging. For plenum-rated installations, FireGuard® PVC compounds provide exceptional flame resistance and smoke suppression to enable compliance with stringent fire safety requirements in commercial buildings and data centers.
WCI: How do your compounds perform in high-speed extrusion or when used with crosslinking processes like e-beam or silane grafting?
MP: Teknor Apex Halguard® LS HFFR compounds, Flexalloy® PVC elastomers and FireGuard® LS FR PVC compounds are optimized for high speed extrusion. However, the actual extrusion performance is also dependent on the extruder size as well as the design of the extruder screw, crosshead and tooling which have to be optimized for each product family. The more flame retardant compounds are highly filled resulting in increased viscosity which can have a negative impact on extrusion speed. However, with scientific raw material selection, we have developed LS HFFR compounds which can be extruded at high speeds and enable cables to meet specified performance requirements.
Watch: Top Cable Companies in India
WCI: What breakthroughs have you made to help cable manufacturers in reducing smoke density and toxicity without compromising mechanical integrity in LSZH compounds?
MP: Our extensive R&D activities for LS HFFR compounds have resulted in developing a range of formulations which enabled cable constructions for various building applications to meet flame and smoke requirements for EU CPR Class B2ca, s1. At the same time, these cables meet applicable requirements of IEC 61156 (copper) or IEC 60794 (fiber optic). The scientific selection and balance of raw materials along with optimized blending and melt mixing have been critical to the successful performance of these compounds.
WCI: Are your compounds developed and certified in direct response to cable manufacturers’ compliance needs? How do you support them in regional compliance efforts?
MP: Our compounds are developed with global and regional compliance in mind, with many Halguard® LS HFFR, Flexalloy® PVC Elastomers, and FireGuard® LS FRPVC grades tested to meet key standards such as IEC and UL. We start with VOC inputs from customers and support them by aligning formulations to their certification performance targets providing technical and regulatory data as well as customization and on-site technical support (when feasible) to facilitate compliance across different markets.
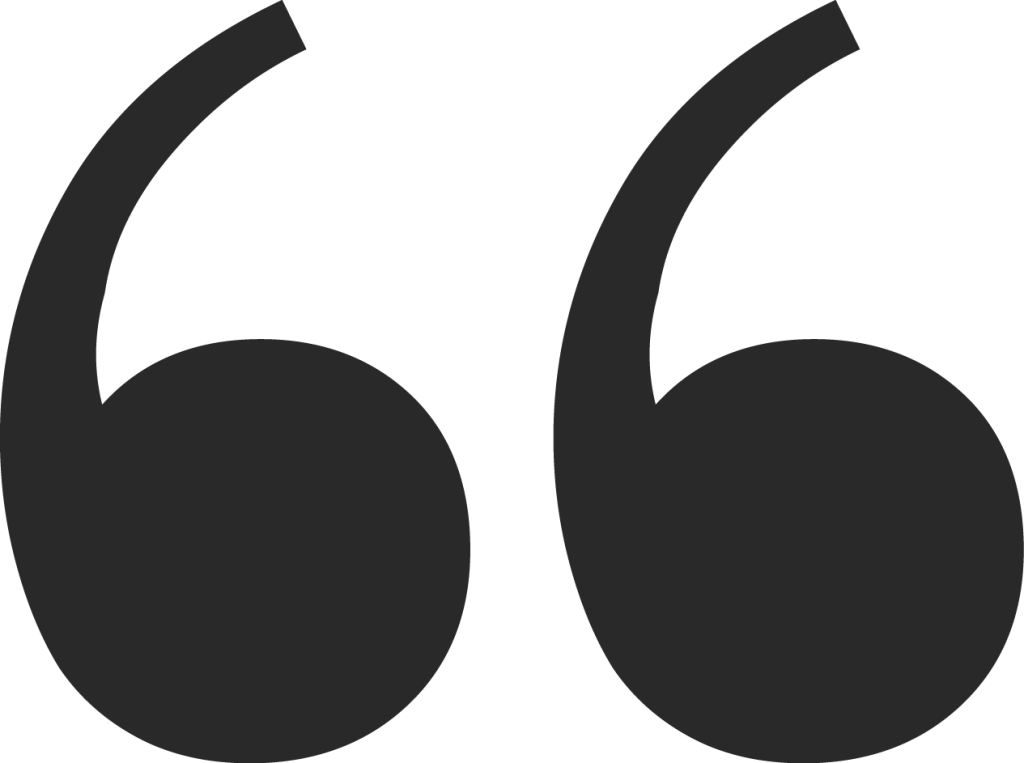
We have been able to develop and launch a range of sustainable next generation compounds for our BioVinyl® product line which is based on bio-based plasticizer and bio-attributed resin.
WCI: Can you share a recent example where you developed or customized a compound for a cable manufacturer’s specific project or tender requirement?
MP: Partnership is one of our core values, so collaboration comes naturally to us and our history is based on being a custom compounder. Developing custom compounds to meet specific customer requirements happens regularly in our business. Unfortunately, we are not able to share specific project details due to confidentiality constraints.
WCI: Advanced material science applications are beginning to appear in commercial cable formulations. Are you working with advanced technologies or synergistic blends that go beyond traditional compounds, specifically to enhance performance in cables?
MP: For quite a few years now, our R&D team has been using AI technology in the development of innovative material platforms for new applications as well as legacy material replacement. This has enabled faster and more precise development that is beyond traditional formulation technology. Specifically, we have been able to develop and launch a range of sustainable next generation compounds for our BioVinyl® product line which is based on bio-based plasticizer and bio-attributed resin.
WCI: Circular economy principles are reshaping material selection processes throughout the value chain. How are you addressing environmental concerns in compounds—whether through halogen-free formulations, recyclable blends, or bio-based additives?
MP: Teknor Apex is committed to sustainable innovation in wire and cable materials. We offer Halguard® low smoke, halogen-free, flame retardant (LS HFFR) compounds, Cycle-Tek® PVC compounds with recycled content and BioVinyl® compounds containing bio-based plasticizer and bio-attributed resin. These products are designed to support sustainability and circularity goals without sacrificing performance. Our commitment to sustainability is demonstrated by our membership and contributions to the Vinyl Sustainability Council (USA) as well as being an active participant in the Vantage Vinyl™ program.
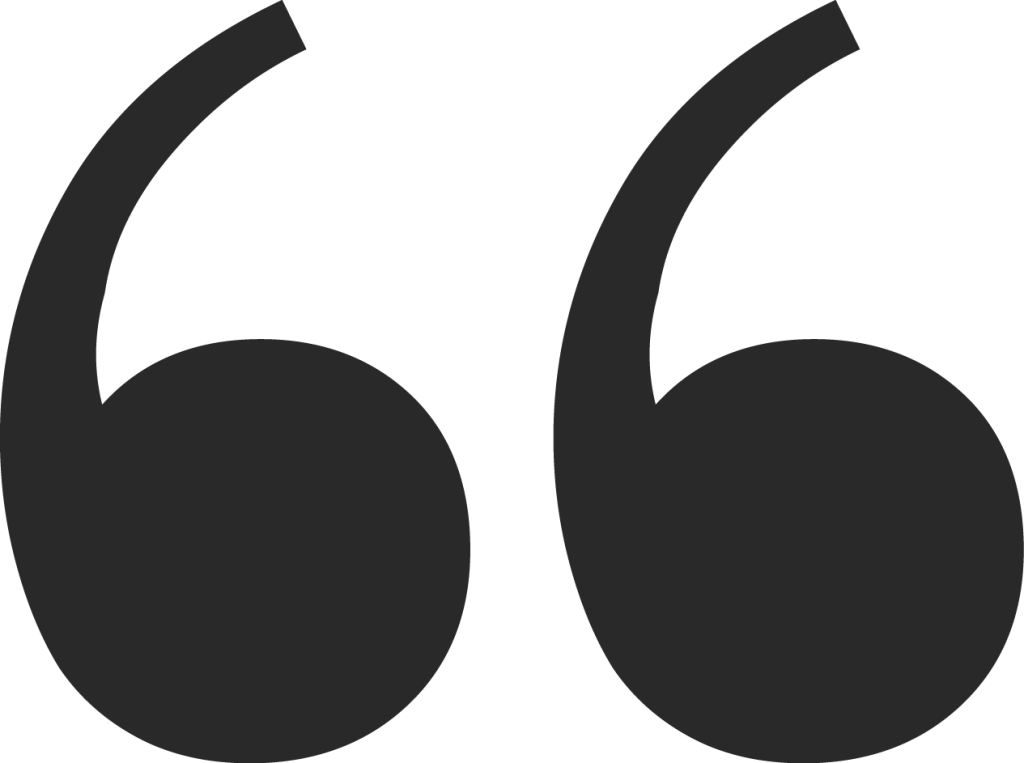
The singular development which could revolutionize the cable industry is the development of sustainable low smoke, halogen free, flame retardant compounds which can be extruded at similar speeds as PVC and enable cables to meet the highest level of flame performance – USA NFPA 262 or EU CPR Class B1ca.
WCI: The gap between laboratory certification and field performance remains a discussion point in industry forums. What kind of feedback do you typically receive from cable manufacturers regarding performance in terms of what works well, and what still needs improvement?
MP: Feedback from cable manufacturers highlights the consistency and reliability of our compounds during their production as well as cable compliance with applicable performance standards. No two cable manufacturers have exactly the same size extruder, same extrusion screw, crosshead and tooling design. So, as much as we design for processability with as broad a processing window as possible while still retaining properties, the feedback when we do receive any, is generally centered around tweaks to help address processing situations specific to their equipment setup.
Also Read: Beyond just Compounds, Fainplast Focuses on Processes, Certifications and Addressing Challenges
WCI: From a compounder’s perspective, what’s the next big leap needed in material science to meet the cable industry’s evolving needs?
MP: The next big leap will come from materials that combine higher fire performance with greater sustainability and higher processing speed. The singular development which could revolutionize the cable industry is the development of sustainable low smoke, halogen free, flame retardant compounds which can be extruded at similar speeds as PVC and enable cables to meet the highest level of flame performance – USA NFPA 262 or EU CPR Class B1ca.