In an exclusive interview with Wire & Cable India, Mr. Arun Kumar Sahu, General Manager at Shakun Polymers, highlights the company’s ECOTEK series of HFFR compounds– designed for critical infrastructure such as metro rails, smart cities, power, telecom, and fibre-optic cables. These formulations employ ATH/MDH mineral fillers to achieve ~35 % limiting oxygen index (LOI) and a 300 °C thermal index, while supporting extrusion in tropical climates. Their silane-crosslinkable HFFR grades enable high-speed extrusion and compatibility with e-beam processes, ensuring mechanical integrity and efficiency.
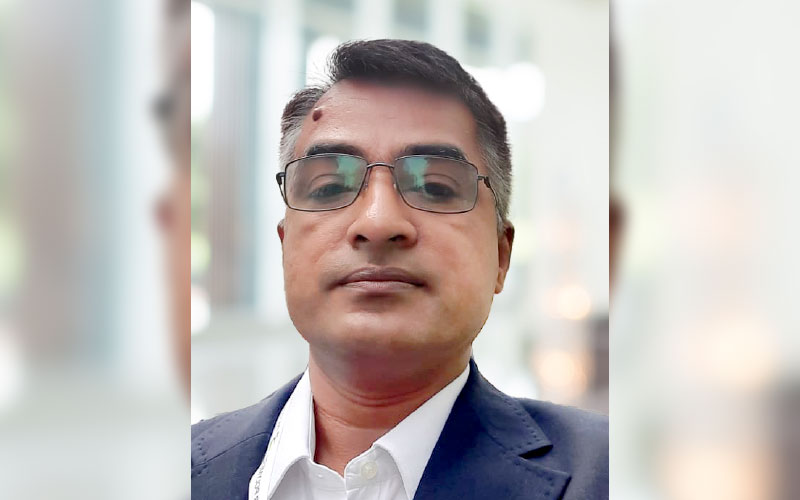
Wire & Cable India: As infrastructure projects like metro rails and smart cities expand with stricter fire safety protocols, which of your current compounds are specifically engineered to meet cable manufacturers’ fire performance requirements, and what cable types or sectors are they most suited for?
Arun Kumar Sahu: Shakun Polymers offers a range of compounds tailored to meet the stringent fire performance demands of infrastructure projects like metro rails and smart cities. Our Halogen-Free Flame Retardant (HFFR) compounds, such as Shakun’s ECOTEK series grades, are engineered for excellent fire safety, low smoke emission, and reduced toxicity—critical for high-risk environments. These compounds are ideal for power cables, telecommunication cables, and fibre optic cables, serving sectors like transportation, urban infrastructure, and energy distribution. These products align with international fire safety standards, ensuring reliability and performance in demanding applications.
WCI: The transition toward halogen-free solutions continues in the cable industry despite processing challenges in tropical manufacturing environments. How are you leveraging halogen-free flame retardants, mineral fillers like ATH or MDH, or phosphorus-based systems in your fire-safe formulations to align with cable manufacturers’ processing capabilities and fire safety needs?
AKS: The cable industry’s shift toward halogen-free solutions is driven by safety and environmental concerns, but processing challenges in tropical climates, such as high humidity, require robust formulations. Shakun Polymers leverages halogen-free flame retardants and mineral fillers like Aluminium Trihydrate (ATH) and Magnesium Di hydroxide (MDH) to create fire-safe compounds. For example, ECOTEK series – Thermoplastic/Thermosetting products incorporates high loadings of flame-retardant mineral fillers, achieving a Limiting Oxygen Index (LOI) of about >35% and a temperature index of 300°C. These fillers release water vapor at high temperatures, cooling the material and suppressing flammable gases. While phosphorus-based systems are not explicitly mentioned, our formulations likely include special additives to enhance fire performance while maintaining processability, which further makes our compounds user-friendly.
Watch: Top Cable Companies in India
WCI: Cable manufacturers report varying levels of success with newer fire-resistant compounds in high-speed production environments. How do your fire-retardant compounds perform in high-speed extrusion or when used with crosslinking processes like e-beam or silane grafting?
AKS: Our fire-retardant compounds are optimized for high-speed extrusion and compatibility with crosslinking processes such as e-beam and silane grafting. We have range of silane cross-linkable HFFR compounds, excelling in high-speed production, maintaining dimensional stability, and minimizing defects like drooling. By leveraging reactive extrusion technology, our compounds integrate seamlessly with crosslinking methods, enhancing mechanical and thermal properties. This ensures cable manufacturers achieve both efficiency and uncompromised flame retardancy, meeting the demands of modern production lines.
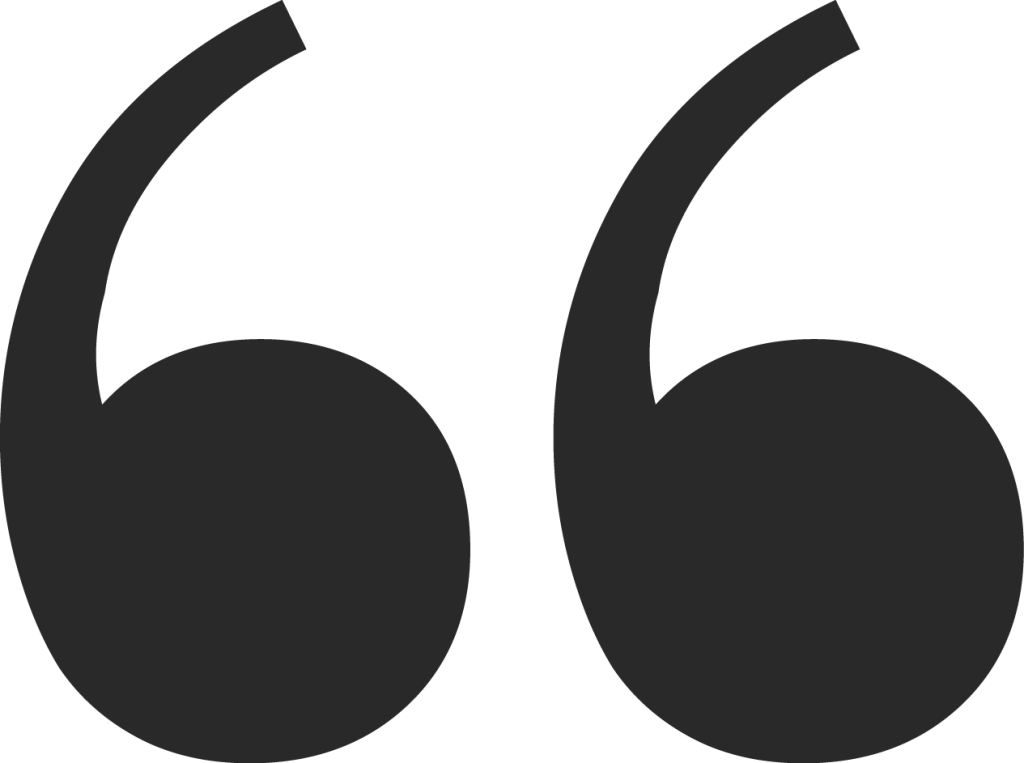
Cable manufacturers praise our compounds for meeting international fire safety standards and their processability in high-speed extrusion, ensuring reliable performance in real-world applications.
WCI: Metro rail projects increasingly specify low smoke and toxicity requirements alongside mechanical durability standards. What breakthroughs have you made to help cable manufacturers in reducing smoke density and toxicity without compromising mechanical integrity in LSZH compounds?
AKS: Shakun Polymers has pioneered advancements in Low Smoke Zero Halogen (LSZH) compounds that can be applicable for metro rail specifications. Our ECOTEK series – Thermoplastic/Thermosetting products compound, formulated with thermoplastic polymers and inorganic fillers, significantly reduces smoke density and toxicity during combustion. Cables manufactured using these compounds, tested to various flammability standards IEC 60332-1, 2 and 3 etc, ensures low smoke generation while retaining flexibility, tensile strength, and durability. Our R&D efforts focus on optimizing the balance between flame retardancy and mechanical integrity, enabling cable manufacturers to meet both safety and performance requirements in demanding applications.
WCI: The tender specification process for infrastructure projects often requires collaborative material development. Can you share a recent example where you developed or customized a fire-retardant compound for a cable manufacturer’s specific project or tender requirement?
AKS: Shakun Polymers excels in collaborative material development for infrastructure project tenders. A notable example is the development of type ST-12 compound as per IEC 60840, which required meeting stringent performance criteria. This project involved close collaboration with a cable manufacturer to ensure the compound met tender specifications, demonstrating our ability to deliver tailored solutions for specific project needs.
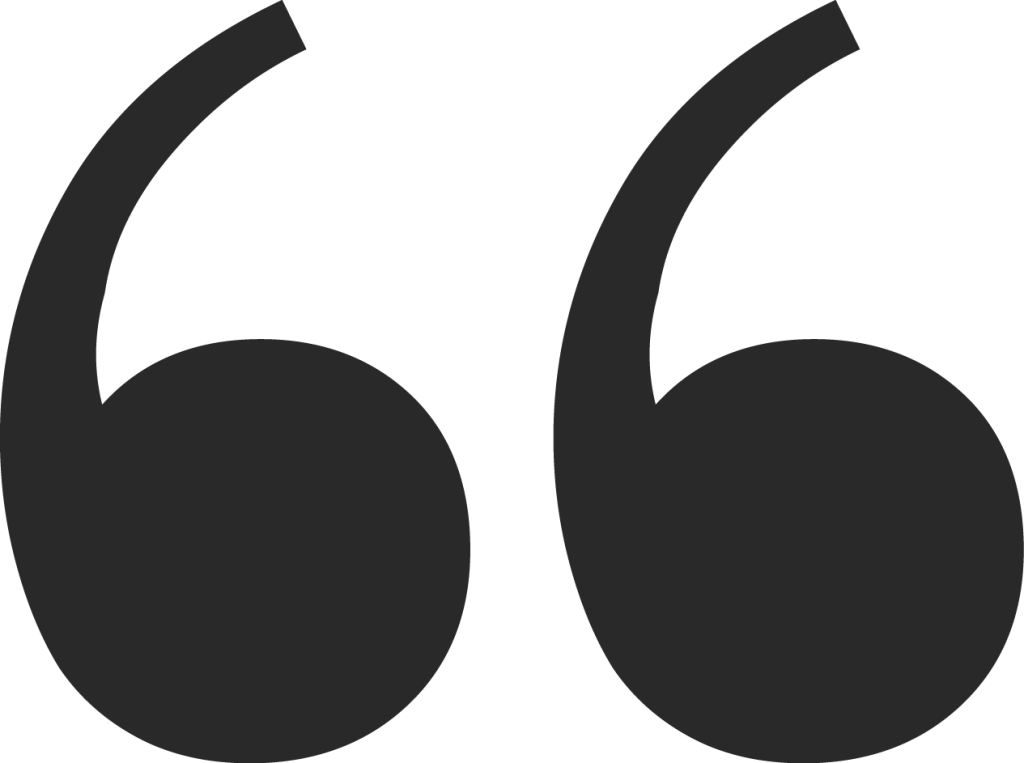
Our investments are focused on semicon compounds, specialty XLPE compounds, EPR, EPDM and rubber-based Silicon compounds. This investment plan will further help us increase our presence in domestic and international markets.
WCI: Circular economy principles are reshaping material selection processes throughout the value chain. How are you addressing environmental concerns in fire-retardant compounds—whether through halogen-free formulations, recyclable blends, or bio-based additives?
AKS: Shakun Polymers will align itself with circular economy principles as the industry evolves by offering halogen-free formulations that eliminate toxic halogen gas emissions during combustion. Our compounds are RoHS compliant and meet REACH regulations, ensuring environmental responsibility. While recyclable blends and bio-based additives are not currently the industry standard nor we witness demands as of today. However, our R&D team is well equipped to serve such requirements in exploring sustainable alternatives to further reduce environmental impact, supporting the cable industry’s shift toward greener materials in coming future.
WCI: The gap between laboratory certification and field performance remains a discussion point in industry forums. What kind of feedback do you typically receive from cable manufacturers regarding fire performance in terms of what works well, and what still needs improvement?
AKS: Cable manufacturers praise our compounds for meeting international fire safety standards and their processability in high-speed extrusion, ensuring reliable performance in real-world applications. Our compounds are designed to withstand harsh conditions like elevated temperatures, higher humidity, and mechanical stress. We are addressing this by refining formulations to enhance long-term stability, bridging the gap between lab certification and field performance.
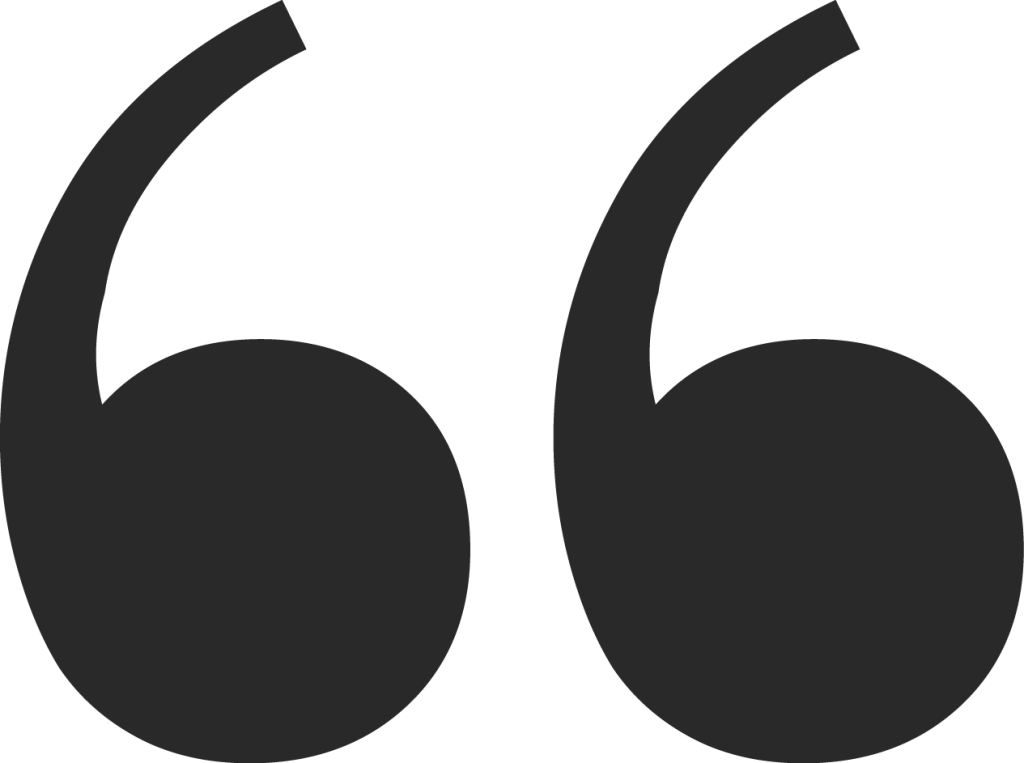
We have a high-performance, oil-resistant SHF2 compound designed for offshore, marine, and oil & gas
cable applications.
WCI: Material science innovation continues driving performance advances while addressing processing challenges. From a compounder’s perspective, what’s the next big leap needed in fire-safety material science to meet the cable industry’s evolving needs?
AKS: The next leap in fire-safety material science lies in multifunctional compounds that combine superior flame retardancy with enhanced thermal stability, mechanical strength, and sustainability. At Shakun Polymers, we are committed to driving these advancements, ensuring our compounds meet the cable industry’s future safety and environmental challenges.
WCI: What kind of growth are you expecting for your company?
AKS: In addition to our existing production capacity of about 50,000 MT per annum, we have done investments to bring our capacities to 1,00,000 MT per annum. Our investments are focussed on Semicon compounds, specialty XLPE compounds, EPR, EPDM and rubber-based Silicon compounds. This investment plan will further help us increase our presence in domestic and international markets. Currently, our capacities are equally divided for local and export business and we anticipate to continue this perfect balance as we are witnessing huge demands from India and other regions, both.
Also Read: Teknor Apex’s Advanced Fire Safety With Halguard®, FireGuard® and Flexalloy®
WCI: Are there any speciality solutions offered by Shakun Polymers?
AKS: We have a high-performance, oil-resistant SHF2 compound designed for offshore, marine, and oil & gas cable applications. As a silane-grafted, moisture-curable, halogen-free, and flame-retardant material, it meets IEC 60092-360 standards for inner sheathing and jacketing in power, control, and instrumentation cables. Key features include Oil Resistance, Zero Halogen & Low Smoke compliant with IEC 60754-1, 2, Flame Retardancy, High Thermal Stability and Non-Corrosivity. Our portfolio also includes specialized grade for Photo Voltaic Insulation and Sheathing application. It is a high-performance, zero halogen, flame-retardant compound designed for solar photovoltaic (PV) cables, supporting the global push for sustainable energy. Developed through R&D starting in 2017 and launched in 2020, this compound, paired with the high-performance catalyst, meets stringent TUV standard when conducted on cable. It offers durability, excellent Processability, and global acceptance from territories like Brazil, Turkey, the Middle East, Europe, and South Africa.
WCI: What is your perspective on India’s power sector growth?
AKS: India’s power demand is projected to double from 2023 to 2030, with the Central Electricity Authority forecasting a peak demand of 366 GW by 2030, up from 243 GW currently, showing an increase of 50%. This is alongside plans to increase power generation capacity to 900 GW. The cable industry is poised for significant growth, and we have planned substantial investments to capitalize on this opportunity.
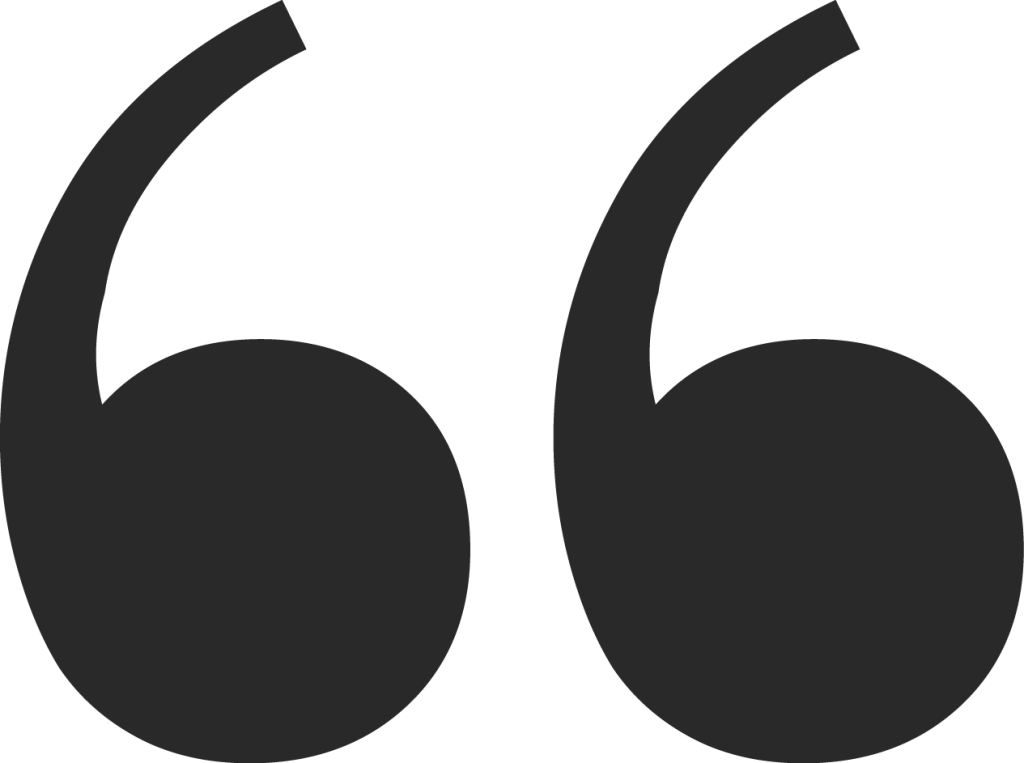
We have a high-performance, oil-resistant SHF2 compound designed for offshore, marine, and oil and gas cable applications. As a silane-grafted, moisture-curable, halogen-free, and flame-retardant material, it meets IEC 60092-360 standards for inner sheathing and jacketing in power, control, and instrumentation cables.