As India modernizes its infrastructure, fire safety in cables is becoming a key priority driven by new regulations and growing fire risks. This story explores how manufacturers and compounders are shifting to halogen-free and recyclable materials while balancing cost, compliance, and environmental demands to build a safer future.
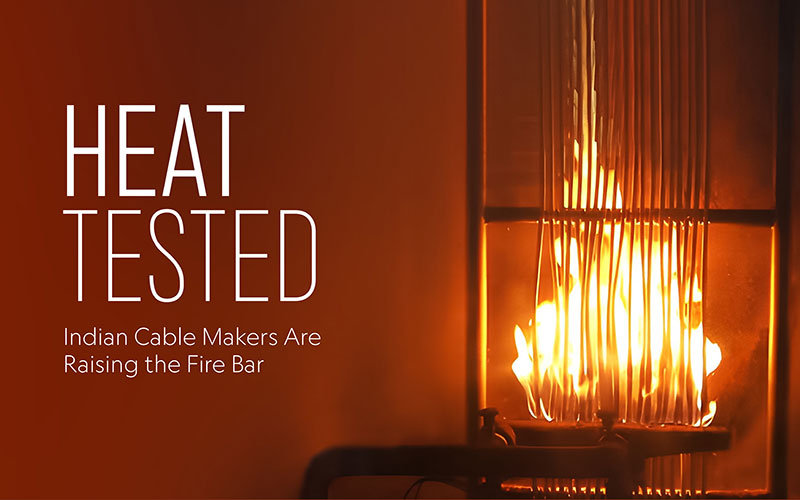
Fire safety is no longer a matter of regulatory compliance alone. Now, it’s fundamental to modern infrastructure planning and electrical system design. In buildings, tunnels, metros, airports, and factories, where thousands of meters of cable snake invisibly through ceilings, walls, and conduits, the performance of those cables in the event of fire can decide not just property damage, but lives saved or lost.
India’s fast-paced urbanization demands immediate attention to fire-safe and dependable cabling. However, challenges remain, from fragmented awareness to inconsistent enforcement of safety norms. “The 2022 amendments to India’s electrical safety regulations elevated the threshold for flame retardance and smoke density, compelling us to re-evaluate our entire compounding strategy,” informs Anil Gupta, CMD, KEI Industries.
Technical Aspects of Fire-Safe Cables
At the core of fire-safe cable technology lies the use of specialty compounds and fire-tested designs that either resist ignition, limit flame propagation, or reduce the emission of smoke and toxic gases. Fire-safe cables are typically categorized as flame-retardant (FR), flame-retardant low smoke (FRLS), halogen-free flame-retardant (HFFR or LSZH), and fire-survival types as defined under IS 17505-1 for thermosetting insulated low smoke cables designed to maintain circuit integrity during fire.
FR cables are designed to resist the spread of fire by self-extinguishing when the source of fire is removed. FRLS cables go a step further by reducing the emission of thick, black smoke and corrosive gases, which helps improve visibility and safety during evacuation. LSZH or HFFR cables, often used in sensitive environments like hospitals, data centers, and transport systems, emit negligible smoke and zero halogens, drastically lowering the toxic impact during combustion.
Cable fire safety performance is validated through standardized tests. These include flame retardance tests such as IS 10810 (Part 53) for single cables, and international standards like IEC 60332 for flame propagation, IEC 61034 and EN 50268 for smoke density, and IEC 60754 for halogen content. IS 17048:2018 in India addresses halogen-free flame-retardant cable performance.
In Europe, EN 50575 under the Construction Products Regulation (CPR) classifies cables from Aca (non-combustible) to Eca (low fire performance) based on reaction-to-fire characteristics. International equivalents such as BS 7846 and BS 7629-1 define fire-resistant construction for armoured and screened cables in fixed installations like alarms and emergency lighting.
As Anil Gupta affirms, “The most influential standards guiding our material selection are the revised IS 7098 (Part 1 & 2), IS 17048, IEC 60332, and IEC 61034.”
Watch: Top Cable Companies in India
Compounding Fire Performance
A fire-safe cable’s fundamental characteristic is its unique compound formulation, specifically the chemical composition of its insulation and sheathing. Compounders have the critical responsibility of developing polymer blends that optimize fire performance while retaining mechanical strength, electrical insulation, and processability.
A number of Indian and global compounders are actively contributing to this effort. Several domestic players such as DDEV, Fine Products, Universal Polychem, Taprath, and Duplast, have developed halogen-free and flame-retardant (HFFR) compounds based on polyolefins, EVA, and thermoplastic elastomers. These materials are engineered to reduce smoke and toxic gas emission while meeting performance benchmarks such as EN 50268 and IEC 61034.
“With the efforts of our R&D team we have been able to work with the latest additives and base resins to achieve very low toxicity with very good mechanical performance,” says Rajesh Kothari of DDEV Group.
Shakun Polymers highlights the company’s ECOTEK series of HFFR compounds– designed for critical infrastructure such as metro rails, smart cities, power, telecom, and fibre-optic cables. “These formulations employ ATH/MDH mineral fillers to achieve ~35 % limiting oxygen index (LOI) and a 300 °C thermal index, while supporting extrusion in tropical climates”, affirms Arun Kumar Sahu of Shakun Polymers.
Global suppliers like Celanese, Teknor Apex, Finproject, and Fainplast contribute through advanced HFFR technologies and sustainable polymer innovations, often designed for export markets with strict CPR classifications such as B2ca and Cca. “Fainplast has been a global leader in producing zero-halogen flame retardant compounds for the wire and cable industry for years,” says Joshua Bruni, Fainplast.
Adriano Vezzani of Finproject adds perspective: “We have worked to evolve compound formulations alongside the use of exceptional mixing technologies, such as the co-kneader. This ensures excellent distributive mixing and optimal distribution of an ever-increasing quantity of high-quality, flame-retardant fillers.”
“The more flame-retardant compounds are highly filled resulting in increased viscosity which can have a negative impact on extrusion speed,” explains Mike Patel of Teknor Apex . “However, with scientific raw material selection, we have developed LS HFFR compounds which can be extruded at high speeds and enable cables to meet specified performance requirements.”
Luis Zalamea from Celanese emphasizes their global innovation approach: “Our formulations and raw material recommendations have been among the first ones to be considered as halogen free solutions and in some cases as viable alternatives to fluoropolymers.”
Elementis, on the other hand, is targeting environmental safety and performance with advanced fire-retardant synergists. Their CHARGUARD™ range of nanostructured organoclays is described as a PFAS-free alternative that “improve flame resistance, reduce smoke, prevent dripping during combustion, and potentially replace materials like PTFE and antimony trioxide.”
Engineering Fire-Safe Cables
Cable makers need to consider much more than materials when it comes to fire safety. The production process must support performance objectives through multi-layer cable constructions, precise conductor stranding, and advanced extrusion techniques. “New fire-resistant compounds pose challenges, especially during the initial phase of manufacturing. High filler loadings in HFFR compounds and cross-linking variability presented challenges during extrusion,” accepts Anil Gupta.
Even distribution of flame-retardant fillers, a perfectly optimized sheath, and strong adhesion between layers are crucial for product integrity during fire. Manufacturers are also investing in in-house fire testing laboratories or leveraging third-party test facilities such as ERDA, CPRI, and UL India to conduct full fire performance testing as per Indian and global standards.
Milind Joshi of Havells observes, “We have addressed these challenges through targeted investments in state-of-the-art compounding and extrusion technology, as well as the implementation of advanced process controls. These measures have enabled us to maintain high standards of quality and performance, even as we transition to more complex material formulations.”
From APAR’s perspective, Shashi Amin emphasizes the precision behind modern manufacturing: “Our compounding philosophy integrates polymer chemistry, flame retardant thermodynamics, rheological stability, and process kinetics to achieve high performance at both laboratory and production scale…”
Celanese supports such efforts through materials optimized for both chemical and physical crosslinking. “Vamac® AEM has a proven track record in the industry as being very efficient in processability whether it is via chemical (i.e. peroxide) or physical (i.e. e-beam) crosslinking,” says Nainesh Shah of Celanese.
Regulatory Framework: Where India Stands
India’s fire safety standards for cables are evolving but have yet to achieve the level of comprehensiveness and enforcement found in more mature regulatory environments. The key Indian standards governing fire performance include IS 694 for PVC cables up to 1100V, IS 7098 for crosslinked polyethylene (XLPE) insulated, thermoplastic sheathed cables used for medium voltage applications (3.3 kV to 33 kV), IS 17048:2018, which defines requirements for halogen-free flame-retardant cables, and IS 17505-1 for fire survival cables.
In addition to IS 694 and IS 7098, India has introduced IS 17505-1 for fire survival cables, aligning with application-specific international benchmarks such as BS 7846 and BS 7629-1, which are often referenced in global projects for fire alarm and emergency systems. While these standards provide a framework for manufacturers, they are often treated as optional unless specified by the client.
In comparison, global frameworks are significantly more prescriptive and enforced. The European Union’s Construction Products Regulation (CPR) mandates performance-based classification and labeling for cables used in buildings, ensuring transparency in fire behavior. This includes reaction-to-fire testing under EN 50399, covering parameters like flame propagation, total heat release, and smoke opacity. In the U.S., fire safety for cables is covered under UL 2196, NFPA 70, and NFPA 130 for fire-resistive and transit-specific applications. These are often mandatory, with third-party certification and visible markings.
Internationally, fire-resistant performance is further validated through standards such as BS 6387, BS 8491, and BS EN 50200, which evaluate cable integrity under fire, water, and mechanical impact. These are often specified in critical safety infrastructure in the UK and international projects requiring PH30/60/90 classifications.
In this evolving landscape, manufacturers are stepping up. “For APAR, regulatory changes are not mere compliance checkboxes; they are opportunities to lead with innovation, safety, and responsibility,” says Shashi Amin of APAR.
In a strong call to action, Anurag Agarwal of Polycab India writes, “Stricter regulations, better enforcement, and a collective commitment to safety can help prevent tragedies. By addressing the root causes of fire accidents, particularly electrical safety lapses, India can protect lives, safeguard property, and build public trust in its fire safety systems.”
The Market Outlook: Progress with Pressure
In the Indian cable industry, the adoption of LSZH cables is visible but slow. The broader market shift is slow. While premium segments of the market, such as metros, airports, hospitals, and data centers are increasingly specifying FRLS or LSZH cables, broader adoption is constrained by cost concerns and limited regulatory pressure.
Nonetheless, government initiatives such as Smart Cities, Digital India, and high-speed rail corridors are driving demand for safer electrical infrastructure, pushing both manufacturers and compounders to elevate their product offerings.
The leading companies, however, are readily embracing the challenge and proactively improvising their HFFR formulations, probably because they realize the criticality or they serve niche clients who can’t do without these. “We are phasing out traditional PVC compounds and actively transitioning to Low Smoke Zero Halogen (LS0H) materials across our cable manufacturing operations,” says Shreegopal Kabra, RR Kabel.
Beyond their fire-safety advantages, LSZH and HFFR compounds are increasingly being viewed through the lens of environmental responsibility, with manufacturers and compounders aligning these materials to evolving goals of recyclability, ROHS compliance, and overall sustainability.
A major factor driving the shift is the risk posed by traditional materials. “The shift away from traditional PVC compounds is a well-documented trend, driven by the need to mitigate the risks associated with corrosive emissions during fire incidents,” notes Milind Joshi of Havells.
Laser Power & Infra’s Praveen Paul notes a complementary shift: “There’s a clear uptick in demand for halogen-free, REACH-compliant, and recyclable materials.”
Rajesh Kothari echoes this sustainable direction: “We as a group of companies are very much aligned to the sustainability aspects. We are working on recipes where the recycles can be used.”
Bio-based compounds and fire retardancy may prove difficult to reconcile. Milind Joshi argues, “Most bio-based materials currently struggle to meet India’s stringent fire safety and durability standards, and cost remains a barrier for large-scale use. However, he quickly adds, “This is a challenge recognized across the sector, with ongoing research and collaboration aimed at overcoming these obstacles.”
Celanese also brings sustainability into sharp focus with renewable content innovation. “For the time being all of our Hytrel® can be purchased in Eco-B format, which guarantees up to 70% renewable content and we are constantly watching market interest and adoption rates to further enhance our offering in this regard,” says Nainesh Shah.
Also Read: KEI Industries Drives Infra-Growth With Halogen Free, Flame Retardant ‘Viksit Wires’
Toward a Safer Cable Ecosystem
Fire safety in cables is no longer just a functional upgrade; it is a foundational requirement for resilient and future-ready infrastructure. Compounders are innovating to deliver high-performance, halogen-free materials.
Manufacturers are upgrading production lines and testing capabilities. Policymakers and consultants are beginning to push for performance-based standards. Yet, the path forward will require coordinated action across the ecosystem—from regulators and builders to OEMs and end-users.
Shashi Amin sums it up aptly: “In India’s harsh operating environment, material science, process engineering, and real-world testing must operate in perfect sync.”
As the industry looks ahead, advanced ceramic-reinforced compounds, designed to withstand higher operating temperatures, have entered the Indian market, offering a promising solution for infrastructure exposed to harsh thermal and environmental fluctuations. “Ceramic-reinforced polymer blends with reduced filler dependency are particularly promising. They align with both India’s heat-intensive environments and Europe’s evolving green regulations,” feels Anil Gupta.
Next-generation materials are designed for superior fire resistance, robust mechanics, and lasting durability. India’s competitiveness hinges on prioritizing key performance attributes like thermal resistance, low smoke, recyclability, and cost-effective processing in its evolving market.