Based out of Italy, Fainplast is a global leader in producing zero-halogen flame retardant compounds for the wire and cable industry. Their product line includes HFFR crosslinkable, PVC thermoplastic, PP propylplus, PE ethylplus, and XLPO special compounds, which enhance fire safety in power and communication cables used in infrastructure projects like airports, shopping malls, public buildings etc. The company collaborates closely with cable production line manufacturers to ensure their compounds perform well in high-speed extrusion and crosslinking processes. They also provide turnkey solutions to help manufacturers comply with both local and international certification standards, such as the European Construction Products Regulation (CPR). In an exclusive conversation with Wire & Cable India, Mr. Joshua Bruni, Foreign Sales, Fainplast emphasises not only the importance of flame-retardent compounds but also sheds light on the processes, certifications and challenges.
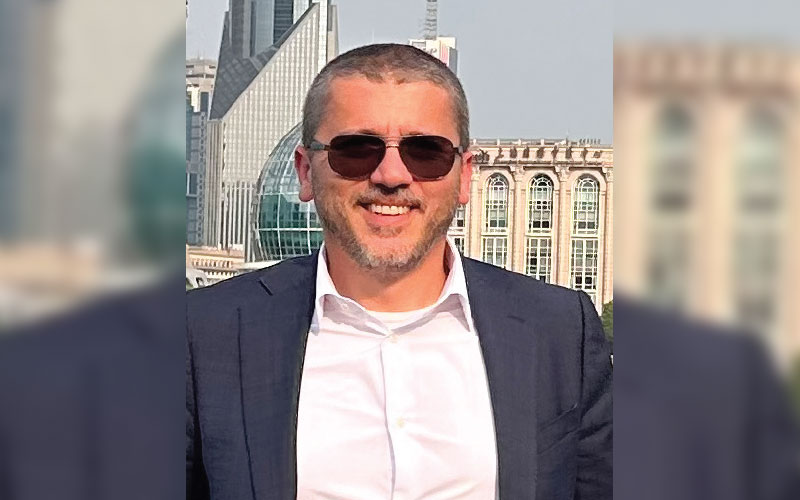
Wire & Cable India: As infrastructure projects and smart cities expand with stricter safety protocols, which of your current compounds are specifically engineered to meet cable manufacturers’ enhanced performance requirements, and what cable types or sectors are they most suited for?
Joshua Bruni: Fainplast has been a global leader in producing zero-halogen flame retardant compounds for the wire and cable industry for years. Compounds such as HFFR crosslinkable, PVC thermoplastic, PP propylplus, PE ethylplus and XLPO special enhance the fire safety of cable wire. The first regulations for the cables were empowered in Europe over 30 years ago, where several studies on fire outbreaks in public environments suggested the importance of installing halogen-free cables to reduce the death toll.
In the years, many countries, including India, have adopted similar regulations that involve a large number of energy and communication cables that must be specifically used in certain projects like airports, shopping malls, public buildings, etc.
Watch: Top Cable Companies in India
WCI: Cable manufacturers report varying levels of success with newer compounds in high-speed production environments. How do your compounds perform in high-speed extrusion or when used with crosslinking processes like e-beam or silane grafting?
JB: Most halogen-free flame retardant materials used in cables, such as those replacing PVC, are based on a halogen-free polymer combined with varying amounts of mineral flame retardants. However, the incorporation of these flame retardants can negatively affect the fluidity of the materials during the cable extrusion process. To overcome this challenge, and enable cable manufacturers to achieve the same productivity levels as with standard PVC cable production, Fainplast collaborates closely with cable production line manufacturers. Through daily efforts, we continuously enhance processing techniques. Today, we confidently assure our customers that, with our compounds, appropriate equipment, and sufficient expertise in material characteristics, they can produce halogen-free flame retardant cables at the same line speed as traditional PVC cables.
WCI: Global export markets demand varying certification standards while domestic requirements continue evolving. Are your compounds developed and certified in direct response to cable manufacturers’ compliance needs? How do you support them in regional compliance efforts?
JB: In Europe the evolution of regulations and the consequent development of the materials is steps ahead of many other markets, including the current Indian domestic demand. We are able to provide turn key solutions for the local standards, but more importantly, also for the international standard like the European Construction Products Regulation (CPR). The CPR today is probably the most demanding regulation regarding cable safety. With our products, Indian cable manufacturers can fulfill the requests of their international customers and, at the same time, gain experience and increase their know-how about certain safety matters that will likely be enforced in India and other markets in the future, thus virtually preparing for the future.
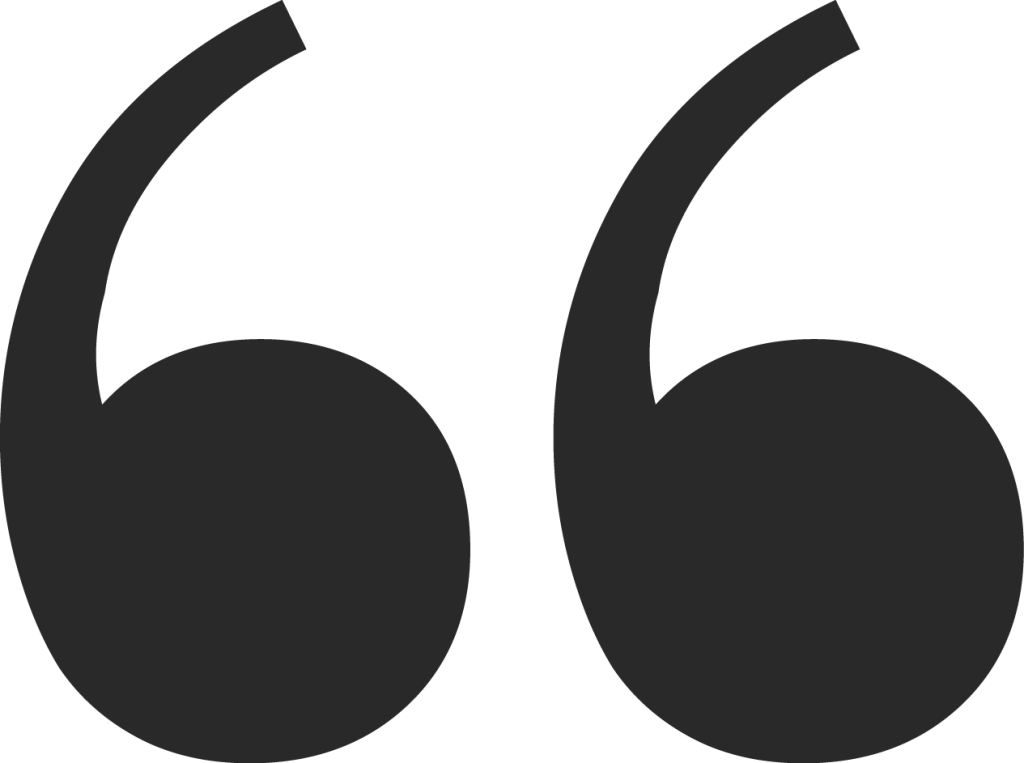
We are able to provide turn key solutions for the local standards, but more importantly, also for the international standard like the European Construction Products Regulation (CPR)
WCI: The tender specification process for infrastructure projects often requires collaborative material development. Can you share a recent example where you developed or customized a compound for a cable manufacturer’s specific project or tender requirement?
JB: We work daily on customized products, so it is common for us to study the requirements of a tender specification. And further identify with our customer the materials and production solutions that will allow them to produce a cable that fully complies with the particular specification.
WCI: Advanced material science applications are beginning to appear in commercial cable formulations. Are you working with advanced technologies or synergistic blends that go beyond traditional compounds, specifically to enhance performance in cables?
JB: As global regulations become increasingly stringent, the formulations for halogen-free flame retardant (HFFR) cables have become more complex. In many applications today, it is insufficient to rely on standard formulations, instead, it is necessary to combine various flame retardants, polymers, and a wide array of additives to create specialized compounds that enable cables to pass specific tests. This is where our extensive experience and strong commitment to research and development set us apart from many compound manufacturers who, in recent years, have begun producing HFFR compounds but lack the technical knowledge or testing equipment to evaluate complex aspects and ensure consistent quality and performance over time.
WCI: Circular economy principles are reshaping material selection processes throughout the value chain. How are you addressing environmental concerns in compounds—whether through halogen-free formulations, recyclable blends, or bio-based additives?
JB: Fainplast holds an International Sustainability and Carbon Certification and is actively engaged in reducing its carbon footprint. The company focuses on utilizing bio-based and recyclable materials in the production of cable compounds. However, the challenge lies in ensuring that these environmentally friendly solutions meet the stringent technical specifications required for cable performance.
Additionally, the cable market often exhibits reluctance to bear the extra costs associated with solutions that have a lower carbon footprint. Consequently, the adoption of bio-based or recycled materials remains limited within the industry. Instead, Fainplast is committed to achieving a zero-emissions goal in its compound production. This approach aims to significantly impact global warming, provided the entire supply chain adopts similar practices.
WCI: The gap between laboratory certification and field performance remains a discussion point in industry forums. What kind of feedback do you typically receive from cable manufacturers regarding performance in terms of what works well, and what still needs improvement?
JB: The laboratory certification is always an approximation of the field performance, because it is never possible to predict the exact environment of the cables and the exact conditions in which a fire spreads. But the laboratory certifications are the only way that the certification body (that acts on behalf of the community / consumers ) has to predict the performance of the cables after they are installed. Compare the performance of different cables and make sure that the risks for everyone are limited.
Beyond this, there is always a gap between laboratory tests and real life. There are customers that are skeptical about the need for certain tests and certifications and there are cable manufactures that act unfairly and make false declarations, but I think this is normal.
Also Read: Celanese Advances Fire-Safety with Halogen-free Materials for Cables
WCI: Material science innovation continues driving performance advances while addressing processing challenges. From a compounder’s perspective, what’s the next big leap needed in material science to meet the cable industry’s evolving needs?
JB: From a compounder’s perspective, the next significant leap in material science for the cable industry lies in the development and integration of bio-based materials. While sustainability is a growing priority across the plastics sector, it poses unique challenges in the cable industry, where high-performance standards and failure tolerance are critical. Advancing bio-based compounds that can meet these rigorous technical requirements without compromising reliability will be essential to aligning innovation with environmental goals.
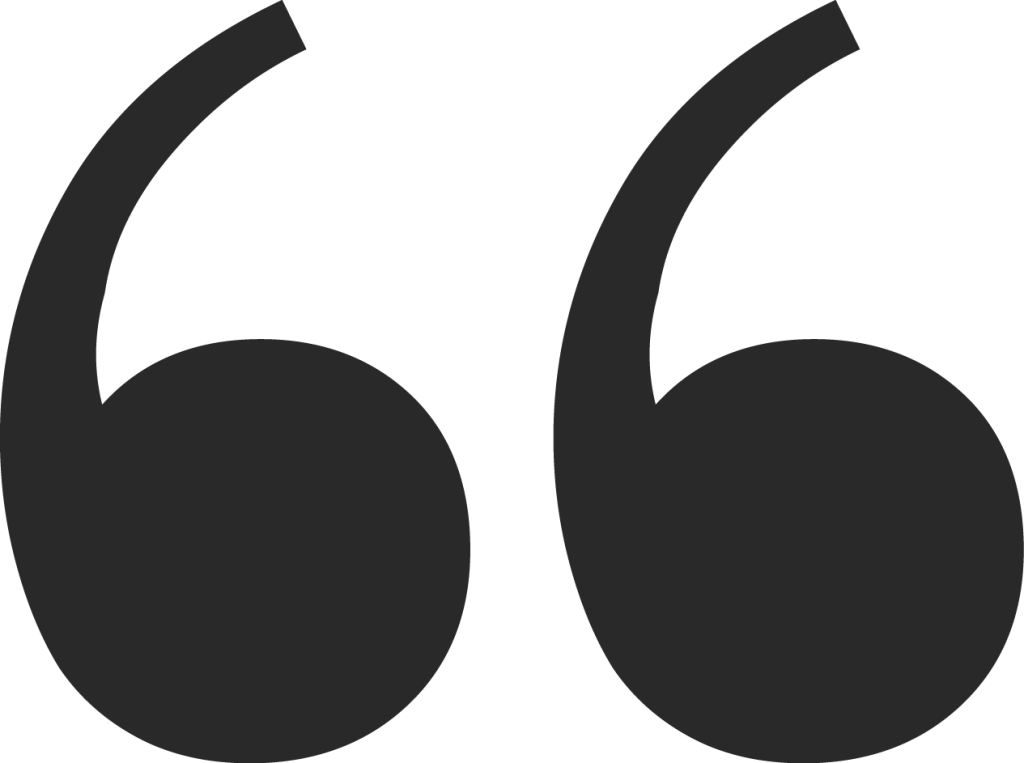
With our products, Indian cable manufacturers can fulfill the requests of their international customers and, at the same time, gain experience and increase their know-how about certain safety matters