In the wake of the recent updates to BIS IS 7098 fire-resistance parameters, the wire and cable industry faces heightened challenges, including a significant rise in compliance testing costs. As safety standards evolve to meet the demands of increasingly complex infrastructure and extreme operating conditions, APAR Industries Limited emerged as a leader in pioneering advanced cable technologies that deliver superior fire performance, durability, and sustainability. In this exclusive interview with Wire & Cable India, Mr. Shashi Amin, CEO, Cable Solutions at APAR Industries Limited, shares insights into how the company is innovating its material science and manufacturing processes to meet and exceed these stringent standards. From adopting cutting-edge halogen-free flame-retardant systems to collaborating closely with global and domestic polymer suppliers, APAR’s initiatives are setting new benchmarks for cable safety and reliability in India’s diverse and demanding environments.
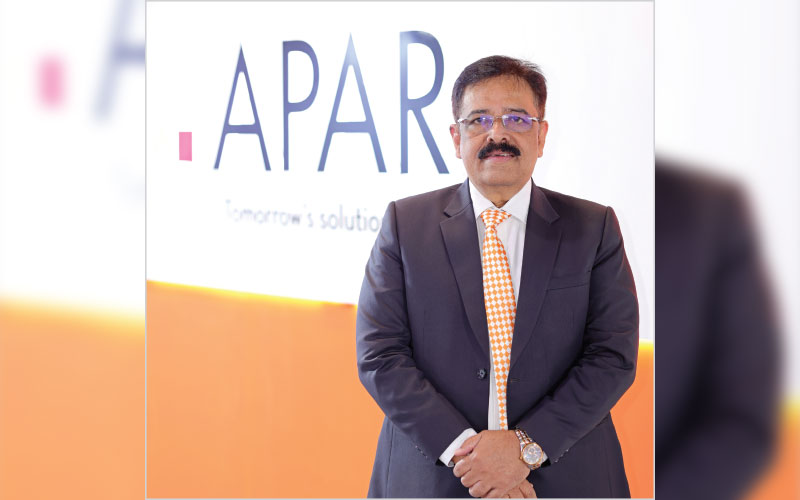
Wire & Cable India: Which specific Indian and international fire-resistance standards most significantly influence your material selection process, and how have these affected your compound sourcing since the 2022 electrical safety regulation amendments?
Shashi Amin: The evolving fire-resistance standards — both in India and globally — have redefined how we approach material science. The 2022 amendments to IS 17048, IS 694, and IS 17493, along with global benchmarks like IEC 60332, IEC 60754, and EN 50575 (CPR), have raised the bar for fire safety, smoke density, and toxic gas emissions.
In response, we’ve strategically shifted to advanced halogen-free flame retardant (HFFR) systems. These materials ensure superior fire performance and offer improved thermal stability, longevity, and recyclability — critical for modern infrastructure, data centres, renewables, and transportation.
Our global sourcing partnerships now focus on suppliers at the forefront of flame-retardant chemistry, enabling us to meet regulatory demands while delivering cables that are safer, more sustainable, and globally competitive.
For APAR, regulatory changes are not mere compliance checkboxes — they are opportunities to lead with innovation, safety, and responsibility.
WCI: Industry reports indicate a major shift toward LSZH materials among leading manufacturers, with premium brands reaching significant implementation, especially in their building wire segments. Within your fire-retardant cable portfolio, which specific material systems (such as LSZH, halogen-free flame retardants, or thermoset compounds) deliver the optimal balance of BIS compliance, performance and production efficiency in the Indian market?
SA: The regulatory tightening post-2022 has made fire-retardant cable compounding a highly engineered discipline rather than a commodity exercise.
In building wire applications, our primary material platform is based on halogen-free polyolefin systems loaded with optimised MDH and ATH flame retardants. Particle size distribution, surface treatment of fillers, and polymer-filler interfacial bonding are finely controlled to achieve target limiting oxygen index (LOI ≥ 32%), low smoke density (IEC 61034), and minimal acid gas emission (IEC 60754). Processing windows are tailored for consistent extrusion rheology and high-speed line efficiency.
For industrial and high-voltage segments, we apply XL-HFFR (crosslinked halogen-free flame retardant) formulations. Crosslinking enhances thermal stability (up to 125°C continuous operating temperature), dielectric breakdown resistance, and mechanical durability under dynamic loading, critical for mission-critical power and control circuits.
Our compounding philosophy integrates polymer chemistry, flame retardant thermodynamics, rheological stability, and process kinetics to achieve high performance at both laboratory and production scale — ensuring that APAR cables comply and outperform in India’s evolving fire safety ecosystem.
Watch: Top Cable Companies in India
WCI: Industry reports suggest a gradual shift away from traditional PVC compounds in various cable applications, with first-tier manufacturers decreasing usage by a significant proportion. Are you implementing similar transitions in your manufacturing operations? What specific combination of factors—BIS regulations, export requirements, metro rail specifications, or technical advantages—drives these material decisions?
SA: The gradual phase-out of PVC in cable applications is no longer just a trend — it’s a technical necessity, driven by evolving safety, performance, and sustainability standards. At APAR, our transition is shaped by four primary forces: BIS regulatory upgrades (IS 17048, IS 694, IS 17493); metro rail and infrastructure fire safety norms (IEC 60332, IEC 61034, IEC 60754); export compliance (EN 50575 CPR, UL 1685, IEC 60331); and lastly OEM demands for higher thermal, electrical, and environmental performance.
We balance this transition with advanced compounding, extrusion optimisation, and rheological control to maintain high production efficiency even with complex formulations. In essence, this is not a PVC replacement—it’s a precision-engineered material evolution for India’s next-generation cable requirements.
WCI: Manufacturing adaptations are often necessary when implementing new fire-resistant formulations. Did new fire-resistant compounds (like crosslinkable halogen-free materials or blends with high filler loadings) create any challenges in your extrusion or compounding lines, particularly given India’s operating temperatures and humidity conditions?
SA: The shift to high-performance fire-resistant compounds—such as XL-HFFR and high-filler LSZH—has introduced significant processing challenges, particularly in India’s high-temperature, high-humidity conditions.
High ATH/MDH loadings (>60%) increase melt viscosity, narrow processing windows, and elevate shear sensitivity. Moisture uptake leads to porosity, micro-voids, and dielectric instability. Crosslinkable systems demand precise humidity and temperature control to ensure uniform crosslinking and long-term performance.
At APAR, we’ve addressed these through advanced compounding, filler pre-conditioning, closed-loop control, optimised design, and moisture-regulated crosslinking systems. These adaptations ensure stable processing, superior product integrity, and full compliance with BIS, IEC, and CPR standards — even under India’s challenging operating environments.
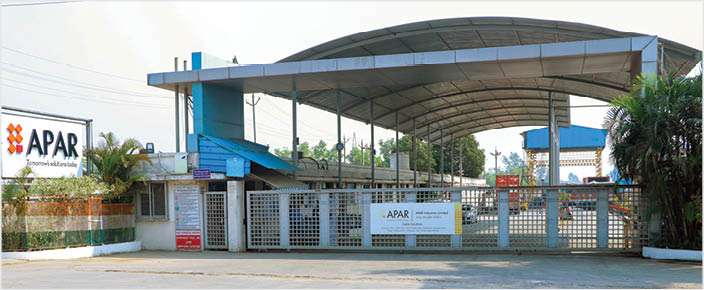
WCI: Leading infrastructure cable suppliers have adopted segmented approaches with distinct material specifications across power, building, and telecommunications portfolios. How do your fire safety material requirements differ between projects for Indian Railways, commercial real estate developments, and data center installations? What regional considerations drive these distinctions beyond basic BIS compliance?
SA: Fire safety in cables is no longer a one-formulation-fits-all approach. Each sector—railway, commercial real estate, and data centres—demands tailored material engineering beyond baseline BIS compliance.
Indian Railways:
Designed to meet IEC 60332-3-24, EN 45545, and RDSO norms, these offer superior flame spread control, minimal toxic effluents, and high fire survival integrity, critical for enclosed, densely populated transport corridors.
Commercial Real Estate:
For high-rise and public occupancy buildings, LSZH systems with high ATH/MDH loading meet IS 17048 and IEC 61034 standards. Focus remains on low smoke, low corrosivity, and visibility for safe evacuation during fires.
Data Centres:
Here, thermal management and uptime are paramount. We apply XL-HFFR systems, compliant with IEC 60332-1-2, 61034, and EN CPR classifications. Materials are engineered for low flame propagation, controlled heat release, and long-term operational reliability.
Regional Considerations:
India’s high ambient temperatures, humidity, and fluctuating grid conditions directly influence compound design — demanding moisture-resistant fillers, stable crosslinking kinetics, and superior thermal aging characteristics.
At APAR, application-specific compounding ensures every cable system delivers optimal fire safety, performance longevity, and compliance across India’s diverse infrastructure ecosystem.
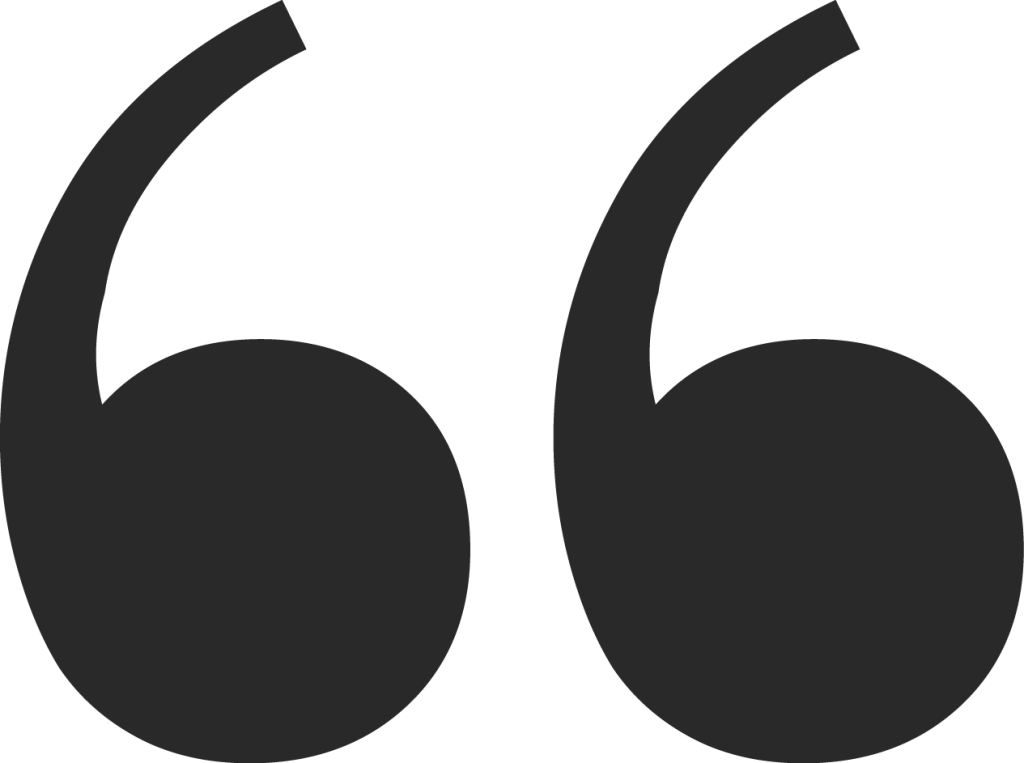
At APAR, application-specific compounding ensures every cable system delivers optimal fire safety,
performance longevity, and compliance across India’s diverse infrastructure ecosystem.
WCI: Recent joint development agreements between polymer suppliers and cable manufacturers suggest deeper supplier-manufacturer partnerships in the Indian market. How extensively does your R&D team engage with domestic and international compound producers when developing cables for specific Indian project tenders? Could you describe a recent example where such collaboration proved particularly valuable?
SA: In today’s rapidly evolving regulatory and application landscape, cable design is no longer isolated engineering—it’s increasingly a joint materials science exercise between cable manufacturers and compound producers.
At APAR, our R&D actively collaborates with both global specialty polymer suppliers and domestic compounders during early-stage material formulation, particularly when responding to highly customised project tenders across sectors like metro rail, nuclear power, defence, and green infrastructure.
In a recent metro rail project requiring EN 45545 compliance, we jointly developed a hybrid XL-HFFR compound modified polymer matrices, and advanced coupling agents to balance flame retardancy, smoke suppression, and extrusion stability — even under India’s high humidity and temperature swings. These strategic collaborations are now central to how we deliver highly customised, fire-safe, and process-efficient cable solutions across sectors.
WCI: Enhanced fire performance often affects other material properties; for example, enhancing fire retardancy in cable materials can impact flexibility. When balancing fire performance against mechanical properties and cost factors crucial in the Indian market, which specific trade-offs have proven most challenging, and how have you addressed them?
SA: In fire-retardant cable design, enhancing flame resistance inevitably impacts other critical material properties — particularly flexibility, processability, and cost-efficiency. This balance becomes even more sensitive in India’s market, where regulatory compliance, price competitiveness, and long-term performance must coexist.
At APAR, we focus on enhancing fire performance often by higher filler loadings, which compromise flexibility, thermal aging, and dielectric strength. In India’s cost-sensitive, high-density installation environment, this trade-off is especially challenging. At APAR, we optimise formulations to reduce filler dependence while maintaining flame retardancy. Controlled formulations allow us to balance fire safety, mechanical properties, and cost across diverse sectors — from metros to mass-market housing.
WCI: Project specifications increasingly include specific fire-resistance requirements beyond standard compliance. Have end users or OEMs started demanding specific certifications or materials—like halogen-free, REACH-compliant, or recyclable options—for fire-resistant cables? Which specific client segments in India are driving more stringent certification requirements, and how has this affected your material qualification and testing processes?
SA: Today’s Indian infrastructure projects increasingly demand cables that go far beyond BIS compliance. Sectors like metro rail (EN 45545-2), data centres (IEC 60332-3, NFPA), green buildings (LEED, IGBC), and export-oriented OEMs (REACH, RoHS, CPR EN 50575) are setting much higher material and fire-performance benchmarks.
At APAR, this has reshaped both our compounding and testing approach. For halogen-free systems, we fine-tune high loadings while maintaining flexibility and processing stability. REACH and RoHS compliance drive strict control of restricted substances, with fully audited raw material sourcing. For CPR and EN 45545 projects, we apply flame retardant systems to balance heat release, smoke density — all while maintaining electrical and mechanical integrity under India’s high temperature and humidity conditions.
Our dedicated in-house NABL accredited testing infrastructure is capable of various certifications combined with full traceability protocols, allowing us to qualify materials faster while ensuring global certification readiness for every tender.
Also Read: Havells India Firms Fire Safety With Upgraded Compounding System
WCI: Safety performance varies across different aspects of fire resistance. Based on your internal testing and field feedback from Indian installations, which specific aspects of fire-resistant performance remain most challenging to address consistently?
SA: Fire-resistant cable performance is multi-dimensional — covering flame propagation, smoke density, toxicity, heat release, and circuit integrity under fire. While formulations have matured, certain parameters like consistent smoke density control (IEC 61034); Heat Release Rate (HRR) Stabilisation (EN 50399 / CPR); long-term circuit integrity (IEC 60331); and surface quality and process stability still pose consistent challenges in India’s complex operating environment.
At APAR, we mitigate these challenges through strict raw material conditioning, advanced compounding, precise controls, and full-scale internal fire testing labs that simulate real-world Indian conditions — ensuring consistent cable performance across diverse projects. Fire-resistant cable design is not just about meeting specifications once — it’s about maintaining repeatability and consistency batch after batch, project after project. In India’s harsh operating environment, material science, process engineering, and real-world testing must operate in perfect sync.
WCI: The proposed amendments to E-Waste Management Rules will impact several cable material streams by 2025. How are you positioning your fire-resistant cable portfolio to address both current BIS safety standards and emerging recycling mandates? Which specific recovery technologies or material innovations show the most promise for the Indian regulatory context?
SA: India’s amended E-Waste Management Rules are pushing cable makers to balance fire safety with recyclability. Fire-resistant cables — with high filler loadings, crosslinked layers, and mica tapes — pose recovery challenges. At APAR, we’re adopting modular designs with recyclable thermoplastic HFFR sheaths and selective crosslinking to enable partial material recovery. Trials on filler recovery and polymer separation technologies are already underway. While maintaining full BIS and IEC fire compliance, our approach ensures readiness for India’s emerging Extended Producer Responsibility (EPR) framework.
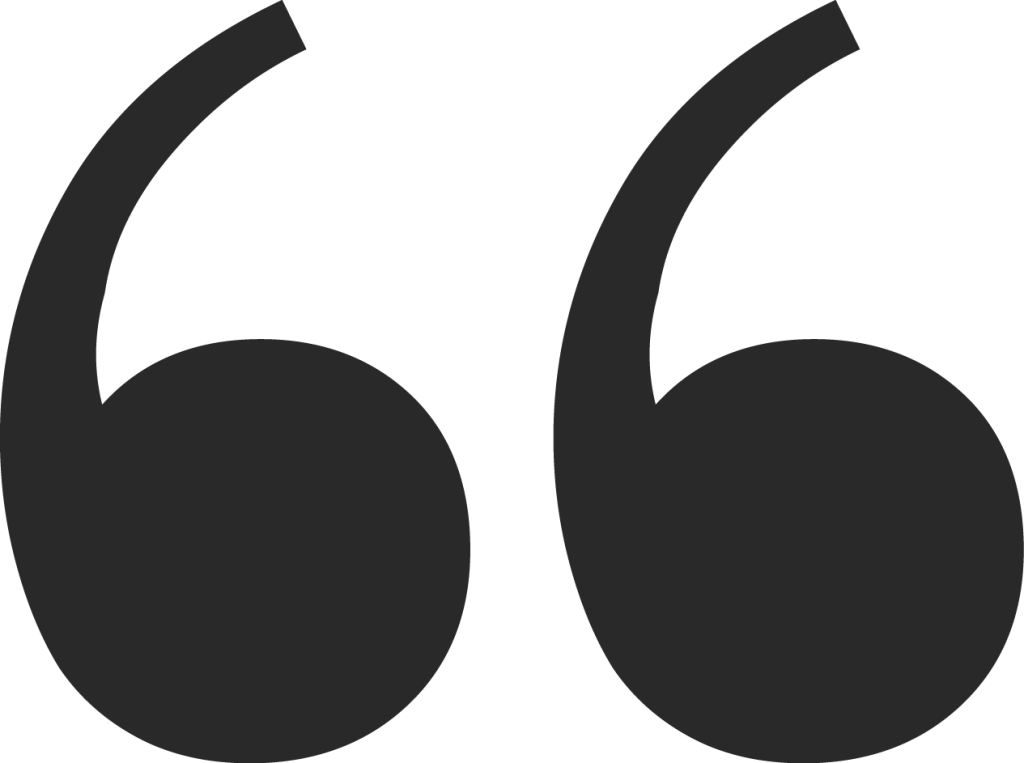
Our compounding philosophy integrates polymer chemistry, flame retardant thermodynamics, rheological stability, and process kinetics to achieve high performance at both laboratory and production scale.