Fine Products Private Limited, a manufacturer of Low Smoke Halogen- Free (LSZH) and flexible PVC Compounds, shares how they are addressing the evolving demands of cable manufacturers by engineering advanced Zero Halogen and FRLS compounds, optimizing processes for tropical conditions, and embracing eco-conscious innovation. With a strong focus on updated formulations, controlled manufacturing, and continuous R&D, the company ensures its fire-retardant solutions meet global and domestic standards while maintaining mechanical integrity. From material sourcing to real-world performance, Fine Products’ commitment to safety, sustainability, and customization stands remains a priority. In an exclusive interview with Wire & Cable India, Mr. Dev Bengani, Director, Fine Products Private Limited shares the nuanced process that prioritises customisation, sustainability and safety in its operations.
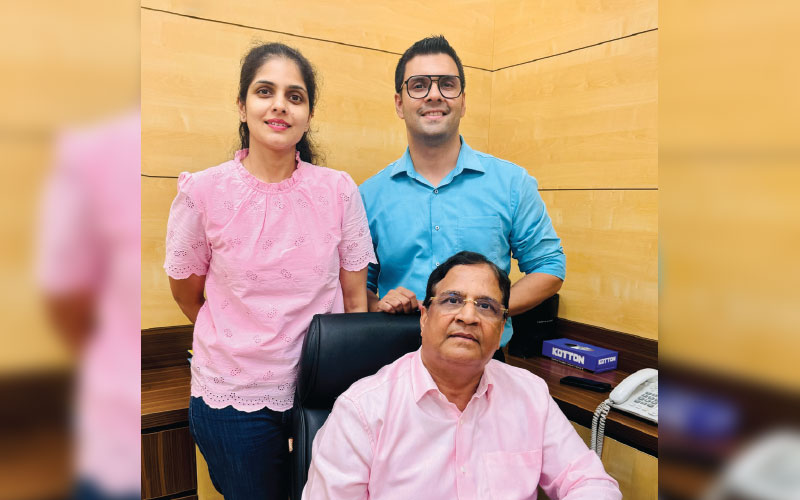
Wire & Cable India: As infrastructure projects like metro rails and smart cities expand with stricter fire safety protocols, which of your current compounds are specifically engineered to meet cable manufacturers’ fire performance requirements, and what cable types or sectors are they most suited for?
Dev Bengani: With the growth of metro rails and smart cities emphasizing stricter fire safety standards, our zero halogen compounds are the go-to solution where public safety is paramount– such as in metros, hospitals, and hotels. These compounds emit minimal smoke and negligible toxic halogen gases, ensuring human and environmental safety. For applications where public exposure is limited, we also offer FRLS (Flame-Retardant Low Smoke) PVC grades.
WCI: The transition toward halogen-free solutions continues in the cable industry despite processing challenges in tropical manufacturing environments. How are you leveraging halogen-free flame retardants, mineral fillers like ATH or MDH, or phosphorus-based systems in your fire-safe formulations to align with cable manufacturers’ processing capabilities and fire safety needs?
DB: International buyers are very cautious of the question asked here, but lately this can be found in many domestic players as well. Time is changing and so is the demand.
We at Fine Products Private Limited, understand this and it’s our habit to use a good product, good machine, apt & controlled process, and educated work force, making the outcome automatically shine bright. You need to be updated with all these and that’s a never-ending continuous process. We follow this from the very beginning, be it with the new sourcing of advanced chemicals or latest technology for production and lab.
In a nut shell we like to be updated cautiously, so it hardly takes time to align with the new demands and requirements. ATH or MDH are few of the many chemicals but they need to be understood and used in a very proper manner to get the desired results. Good working conditions, good machinery and proper testing at every stage of production is important.
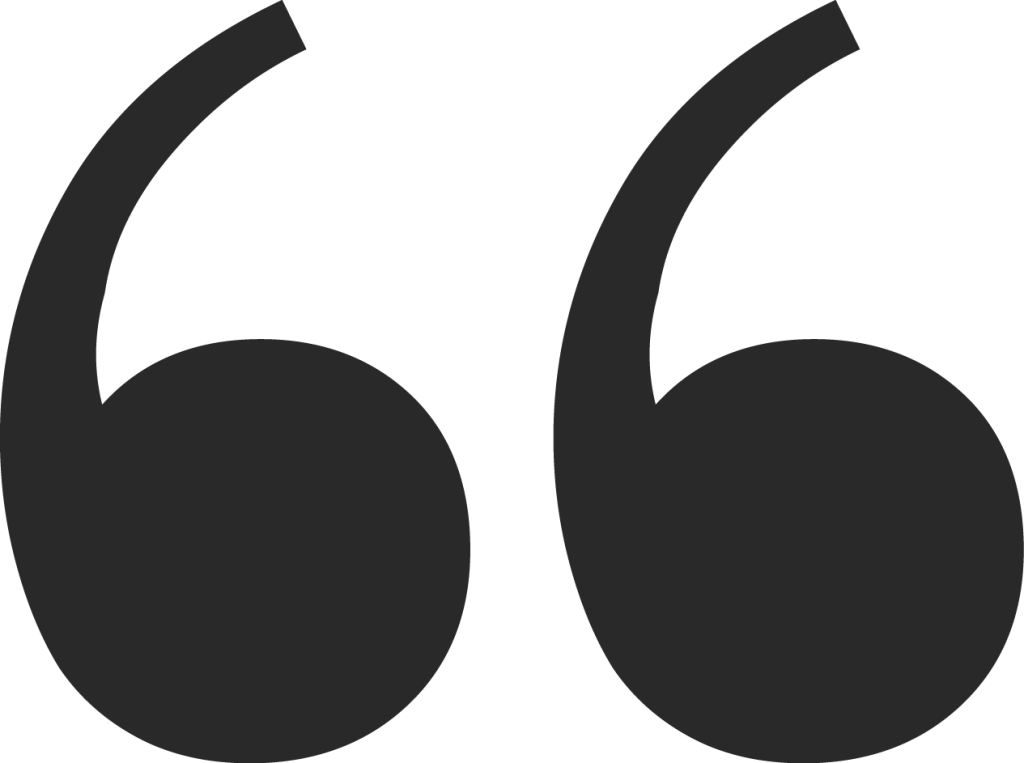
Our Zero Halogen compound as well as PVC compound emit gasses as per pollution norms, recycled water is used here and nothing is dumped in soil as well, thus we make sure that our every step taken does not harm the environment in any way, they are also reusable, thus, no waste is produced in their making.
WCI: Cable manufacturers report varying levels of success with newer fire-resistant compounds in high-speed production environments. How do your fire-retardant compounds perform in high-speed extrusion or when used with crosslinking processes like e-beam or silane grafting?
DB: At this particular moment, we are into making thermoplastic compounds only, cross-linking compounds comes for sure but a bit later. Speed has never been an issue with our compounds i.e. a slower or a high speed, it works just fine be it the finish or the properties, they are just apt.
WCI: Metro rail projects increasingly specify low smoke and toxicity requirements alongside mechanical durability standards. What breakthroughs have you made to help cable manufacturers in reducing smoke density and toxicity without compromising mechanical integrity in LSZH compounds?
DB: Chemicals play an important role, choosing the correct one is a tedious job and luckily, we have the right people around to perform this very adequately. Chemicals and solvents need to be properly immersed in the formulation, which means that the correct process plays a huge role. Yes, mechanical properties do change a bit but using the right composition and the process, this can be minimised. We certainly follow some laid down procedures strictly, be it the procurement part or the process part and as said earlier our customers don’t find it difficult to mingle with us. We listen to them, understand the concern, give them a solution to try it first and then on getting proper feedback, we deliver, no rush. It takes time and we are available.
Watch: Top Cable Companies in India
WCI: The tender specification process for infrastructure projects often requires collaborative material development. Can you share a recent example where you developed or customized a fire-retardant compound for a cable manufacturer’s specific project or tender requirement?
DB: There is no particular example. Instead we supply to cable manufacturers and their requirements always change as per the project they are working on, like for DMRC, properties required are altogether different from those of other projects, be it overseas as well. Mechanical properties also vary with each client i.e. some want a better tensile property or elongation or tear resistance along-with the fire retardant properties. Each time the recipe has to be curated as per the need of the client and the project they are working on, its location and this is very crucial for compounders like us. Certain times it can be for cities with a high temperature or some place with a cold atmosphere, a formula is curated keeping all these in mind as well.
WCI: Advanced material science applications are beginning to appear in commercial fire resistant formulations. Are you working with nano-fillers, intumescent systems, or synergistic blends that go beyond traditional ATH-based flame retardants, specifically to enhance fire resistance in cables?
DB: In our industry, staying updated is essential. We often experiment with various chemicals, all of which are thoroughly tested in our lab to evaluate performance. ATH has consistently delivered reliable results over the years, but it’s important to give new entrants a fair chance, which makes trying them necessary. Sometimes these trials succeed, sometimes they don’t, but ongoing research is vital. It’s not optional; it’s a core part of our work.
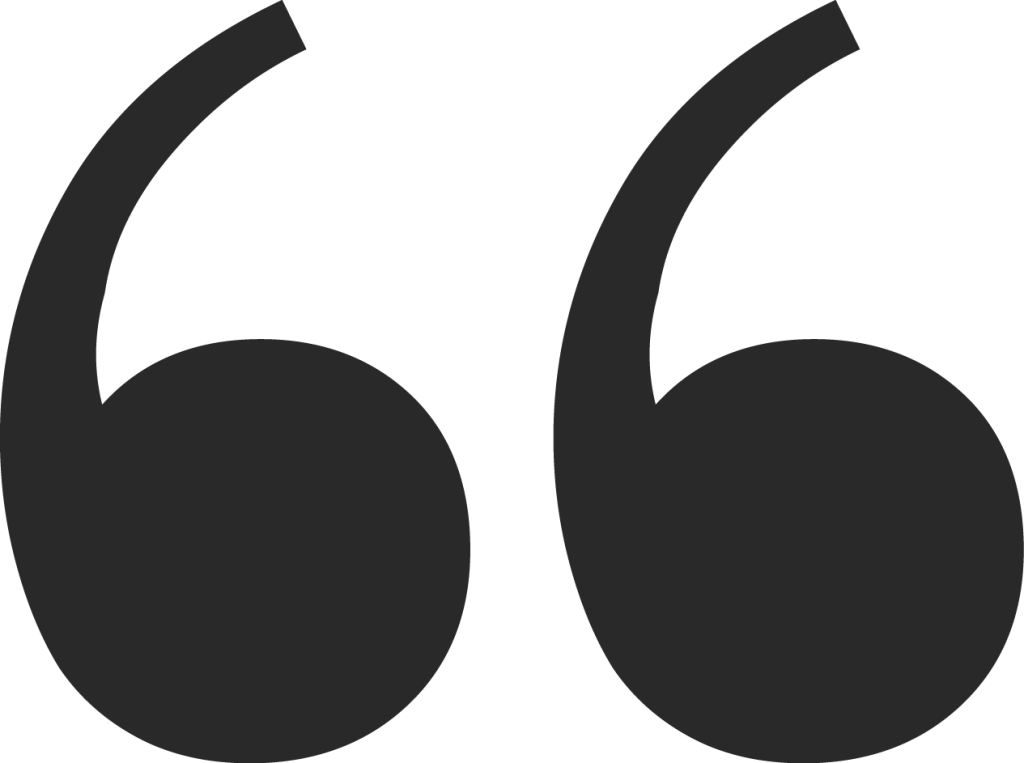
With customers demanding minimal fire, least smoke, and no poisonous gas emissions due to increasing concern for safety and environmental impact, we remain committed to meeting these expectations by constantly upgrading methods with utmost caution and care.
WCI: Circular economy principles are reshaping material selection processes throughout the value chain. How are you addressing environmental concerns in fire-retardant compounds— whether through halogen-free formulations, recyclable blends, or bio-based additives?
DB: Yes, the circular economy surely plays a very big role and it needs to be handled with care. It’s a big circle, where the process needs to be regulated and a chain is made and followed for other segments in continuation. It begins with the careful selection of the raw material, proper machine and an ambient environment where the workforce is comfortable. The ultimate result is an “eco-friendly compound” or the “green compound” as they call it now.
Our zero halogen compound as well as PVC compound emit gasses as per pollution norms, recycled water is used here and nothing is dumped in soil as well, thus we make sure that our every step taken does not harm the environment in any way, they are also reusable, thus, no waste is produced in their making.
Our first unit is into making of LSZH i.e. Low Smoke Zero Halogen compounds, where raw materials need careful attention- be their procurement stage, processing stage or the testing stage at the finished product level. This is the only product where public safety is a major concern, so only an eco-friendly compound works here.
Our second unit is into making virgin PVC as per REACH or RoHS guidelines. We make sure to use those raw materials that are safe for the environment. Our Fire-Retardant Low Smoke (FRLS) compounds and Flame-Retardant (FR) compounds play a major role here, where the chemicals bearing good fire and smoke properties are cautiously monitored and used in a correct manner. The emission of the smoke as well as fire is properly controlled and we make sure in the process that harm to the public is avoided.
WCI: The gap between laboratory certification and field performance remains a discussion point in industry forums. What kind of feedback do you typically receive from cable manufacturers regarding fire performance in terms of what works well, and what still needs improvement?
DB: Certificates from a lab should not be overlooked, they are a set of parameters that needs to be followed and an average for the lot given. Basically, a standard guideline for the product one might say.
Only after this, comes the practical implications and the actual scenario i.e. the actual performance of the product when mingled with other parts i.e. the project area and its temperature, condition of the surroundings, the capability of the people performing the job and many more. A continual improvement approach is required and thus the R&D phase is always ongoing here.
A fire can erupt because of innumerable reasons, may be some negligence while installing, an animal bite, overheating of the surroundings, too much heat or a spark in the conductors etc, so a compounder needs to be ready for any such situation while formulating the composition. The crux here is just to be updated with the requirement so the product can be made as per the need. There is no such gap but only the way to understand. Standards set the rules for upcoming outcomes.
Also Read: Royle: Extruding High Speed Business Growth From Industry 2.0 to Industry 5.0
WCI: Material science innovation continues driving performance advances while addressing processing challenges. From a compounder’s perspective, what’s the next big leap needed in fire safety material science to meet the cable industry’s evolving needs?
DB: Material science innovation continues to drive performance advances while addressing processing challenges, and from a compounder’s perspective, the next big leap in fire safety material science lies in adopting advanced chemical solutions that meet the cable industry’s evolving demands. As the latest chemicals improve properties and performance, it becomes essential to carefully select the right ones, update formulations, and align the production process– where both man and machine play critical roles.
Just as an old engine can’t power a modern Ferrari, BMW, or Mercedes, outdated systems can’t support modern materials, going with the right flow leads to applaudable results. With customers demanding minimal fire, least smoke, and no poisonous gas emissions due to increasing concern for safety and environmental impact, we remain committed to meeting these expectations by constantly upgrading methods with utmost caution and care. As said earlier, just be updated for a good cause.