Since the 2022 regulation updates, Havells India has aligned its compound sourcing with both Indian and international fire-resistance standards. There’s a shift from traditional PVC to advanced LSZH and HFFR compounds, prompting Havells to partner with multiple domestic and global specialized suppliers. The company upgraded its compounding and extrusion systems to handle complex, cross-linkable halogen‑free formulations. With a new facility in Tumakuru and expansion of Alwar facility, Havells is also striking the balance between R&D and supply chain. In an exclusive interview with Wire & Cable India, Mr. Milind Joshi, Senior Vice President, Cable Division, Havells India, shares insights about the intricate demands of the industry and the development of the most critical fire resistant– F120 category cable.
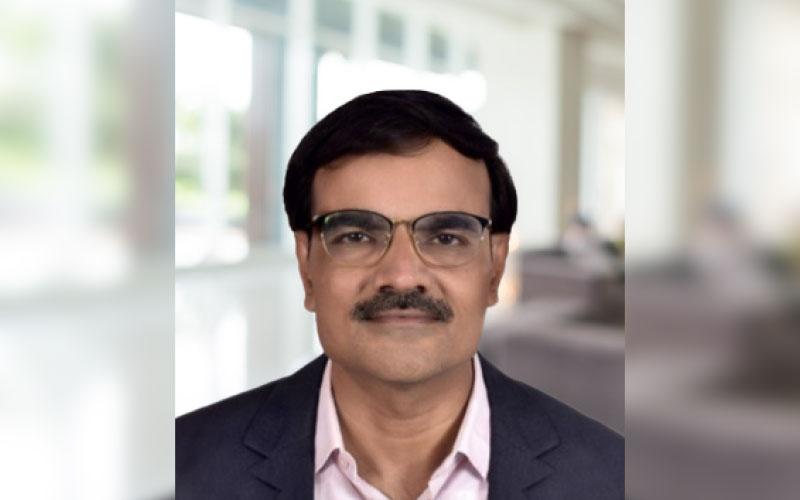
Wire & Cable India: Which Indian and international fire-resistance standards most influence your material selection process, and how have these affected compound sourcing since the 2022 safety regulation amendments?
Milind Joshi: The Indian wire and cable industry’s material selection is now primarily governed by a convergence of Indian and international standards. Domestically, IS 17048:2018 (halogen free flame retardant cables), IS 694, and IS 7098 set the baseline for fire safety in building and power cables. Whereas internationally, BS 7846, BS 6387, BS 8491, BS EN 50200, BS EN 60332-3-24 are used for fire resistant cables, IEC 60332 (tests on electric cables under fire conditions), IEC 60754 (halogen acid gas emission), and IEC 61034 (smoke density) are widely referenced, especially for projects with global stakeholders or export requirements.
Since the 2022 amendments to electrical safety regulations, there has been a significant increase in the enforcement of these standards, directly impacting compound sourcing strategies across the industry. Manufacturers are now required to source advanced HFFR and LSZH compounds, often necessitating partnerships with specialized suppliers who can guarantee compliance and consistent quality. At Havells, we have expanded our supplier base to include both leading domestic and international compound producers, ensuring that our material inputs meet the latest regulatory and performance benchmarks.
Watch: Top Cable Companies in India
WCI: Reports suggest a shift away from traditional PVC compounds. Are you implementing similar transitions in your manufacturing operations?
MJ: The shift away from traditional PVC compounds is a well-documented trend, driven by the need to mitigate the risks associated with corrosive emissions during fire incidents. Hence, the industry is increasingly adopting LSZH and HFFR compounds, which not only comply with stringent fire safety norms but also align with sustainability goals.
We have mirrored this industry transition by prioritizing the development and deployment of FRLS-H and HFFR cables, particularly for high-occupancy and critical infrastructure projects. This is evident in our product portfolio, which now features a significantly higher proportion of LSZH and HFFR offerings. However, it is important to note that the pace of this transition is often dictated by project specifications, regulatory mandates, and customer awareness.
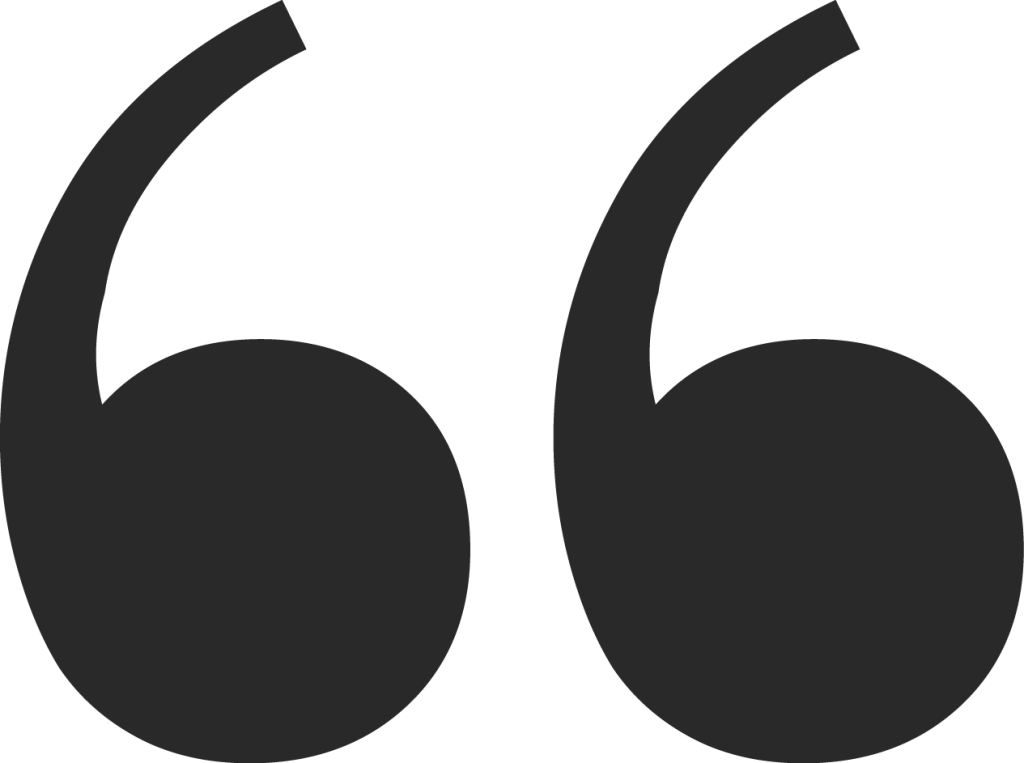
There is growing industry interest in bio-based and recyclable insulation materials, such as PLA and bio-PE. At Havells, we have initiated R&D in this area, but widespread adoption faces significant technical and commercial hurdles.
WCI: Did new fire-resistant compounds create challenges in your extrusion or compounding lines, especially given India’s climate?
MJ: The integration of advanced fire-resistant compounds, such as cross linkable halogen-free materials and high-filler blends, has necessitated significant manufacturing adaptations across the industry. These materials often present challenges in terms of achieving uniform dispersion, maintaining extrusion stability, and ensuring consistent product quality—especially under India’s high ambient temperature and humidity conditions.
We have addressed these challenges through targeted investments in state-of-the-art compounding and extrusion technology, as well as the implementation of advanced process controls. These measures have enabled us to maintain high standards of quality and performance, even as we transition to more complex material formulations. This experience reflects broader industry practices, where continuous process optimization and staff training are essential to successfully adopting new fire-resistant materials.
WCI: How do your fire safety material requirements differ between projects for Indian Railways, commercial real estate, and data centers?
MJ: Material requirements are highly project-specific and this is an industry-wide practice. For Indian Railways and metro projects, cables must meet the highest standards for flame retardancy, low smoke, and zero halogen emissions, given the confined and high-risk environments. However, in commercial real estate, the focus is on FRLS-H and HFFR cables to protect occupants and assets. Data centers, meanwhile, demand cables with superior fire survival and minimal smoke/toxicity to safeguard critical infrastructure. Taking a segmented approach, we tailor our offerings for each segment. Havells is also offering Fire Survival Cable F2 & F120 Category which is duly complied with LPCB and BASEC.
Both our offerings nominated with “Fire Safe” & “Fire Safe Plus” are recognized by LPCB & also mentioned in the “RED Book live”.
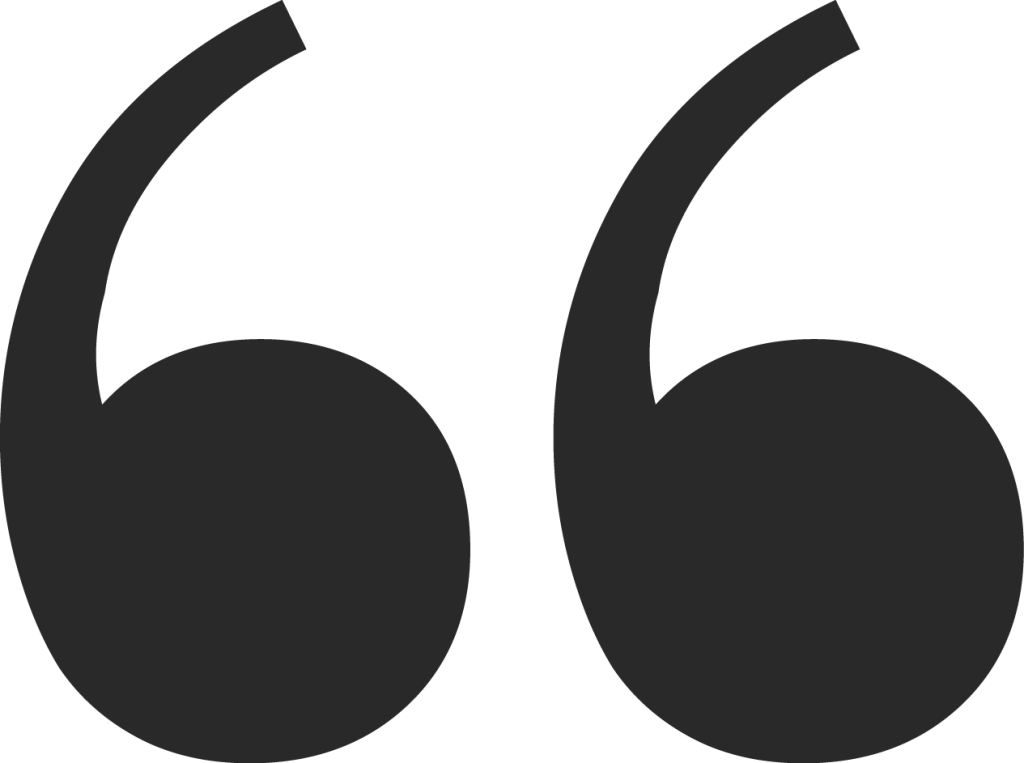
We have developed one of the most critical fire resistant F120 Category Cable, which is mostly used in tunnels, data centers, and inside building premises including hospitals.
WCI: How extensively does your R&D team engage with compound producers for specific tenders? Any recent examples?
MJ: Havells’ R&D function is deeply integrated into our product development and tender strategy, especially within our cables business, which spans both power and flexible cables. As infrastructure projects grow more complex and specialized, our team regularly collaborates with material and compound producers to ensure that our offerings meet evolving regulatory standards and customer expectations—particularly around safety, performance, and sustainability.
We are engaging with IIT to strengthen our inhouse XLPE compound parameters with the global standards and doing endurance and morphological characteristics of cable.
In FY 2024-25, our cables division achieved revenues of INR 7,184 crore, reflecting the increasing demand driven by rapid electrification, the growth of data centres, and the expansion of sectors like railways, metros, and telecom. To support this demand and address capacity constraints, we commissioned a new manufacturing facility in Tumakuru and are further expanding our Alwar plant. These developments are backed by strategic investments of INR 450 crore focused on producing higher-sized cables—often required in large-scale infrastructure tenders. Such investments are underpinned by our R&D-led approach to innovation and material development. This synergy between R&D and supply chain partnerships ensures Havells remains agile and responsive in delivering value-driven, compliant solutions across key public and industrial sectors.
WCI: What trade-offs have proven most challenging when balancing fire performance, mechanical properties, and cost?
MJ: Balancing fire performance with mechanical properties and cost is a persistent challenge for the industry. Enhanced fire retardancy often results in increased stiffness, reduced flexibility, and potential installation difficulties. Additionally, advanced compounds tend to be more expensive, posing a challenge in India’s price-sensitive market.
As an industry leader, we address these trade-offs through the optimization of polymer blends and filler systems, supported by rigorous R&D and in-house testing. We aim to deliver cables that meet or exceed fire safety standards while maintaining the flexibility and durability required for practical installation. This balancing act is a common focus across the sector, with ongoing innovation aimed at minimizing compromises and ensuring value for end-users.
WCI: Which aspects of fire-resistant performance remain most challenging to address consistently?
MJ: Consistently achieving low smoke emission and minimal acid gas release during fires is a persistent challenge for the entire industry. Field feedback from installations across India often highlights variability in these parameters, especially under real-world conditions. Manufacturers, including Havells, are investing in advanced material science and process controls to improve consistency, but this remains an area of ongoing development sector wide. We have developed one of the most critical fire resistant F120 Category Cable, which is mostly used in tunnels, data centers, and inside building premises including hospitals.
Also Read: Laser Power and Infra Levels Up Fire Safety with FRLSH Cables And Compound Supplier Collaborations
WCI: Looking toward next-generation fire-safe materials, which performance attributes would deliver the greatest value?
MJ: The industry is closely watching the emergence of advanced ceramic-reinforced and smart compounds that offer higher temperature ratings, better mechanical robustness, and improved recyclability. For India’s climate and infrastructure needs, materials that combine superior fire survival with high durability and sustainability will deliver the greatest value.
WCI: Have you investigated biodegradable or bio-based insulation materials? What hurdles remain?
MJ: There is growing industry interest in bio-based and recyclable insulation materials, such as PLA and bio-PE. At Havells, we have initiated R&D in this area, but widespread adoption faces significant technical and commercial hurdles. Most bio-based materials currently struggle to meet India’s stringent fire safety and durability standards, and cost remains a barrier for large-scale use. This is a challenge recognized across the sector, with ongoing research and collaboration aimed at overcoming these obstacles.
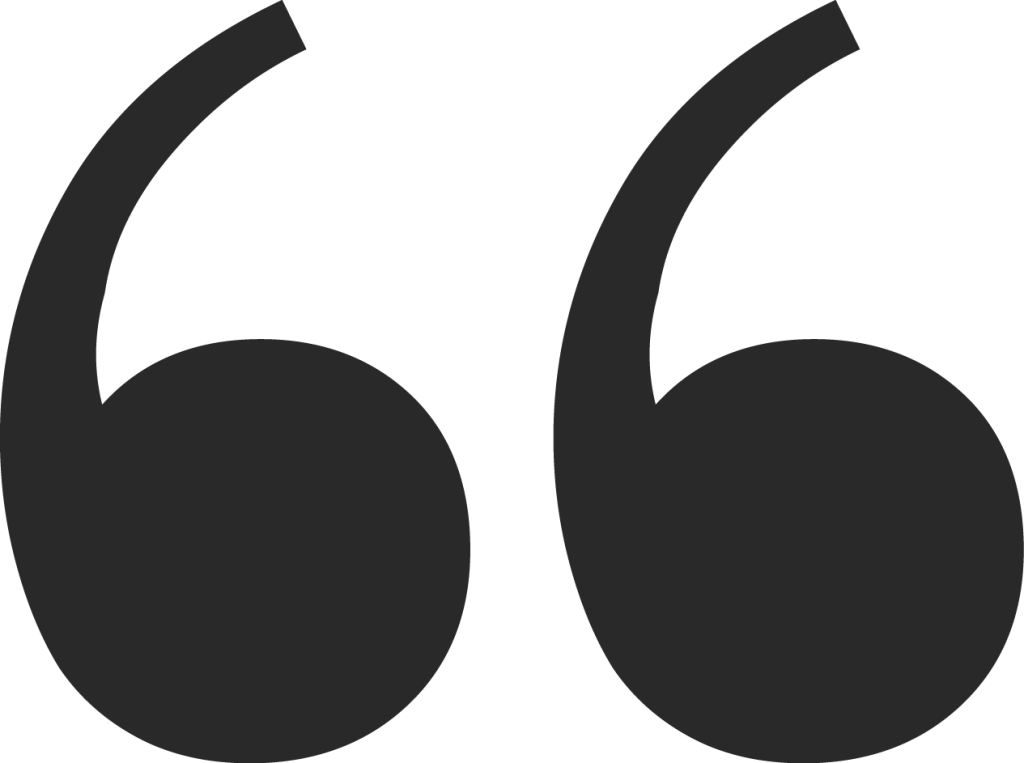
We aim to deliver cables that meet or exceed fire safety standards while maintaining the flexibility and durability required for practical installation.