Laser Power & Infra Private Limited is advancing its cable manufacturing strategy through advanced material choices and closer collaboration with compound suppliers. In this exclusive interaction with Wire & Cable India, Mr. Praveen Paul, Vice President, Laser Power & Infra Private Limited, outlines how the company is transitioning from PVC to LSZH and HFFR compounds to meet stringent BIS norms, especially for sectors like Indian Railways, metro rail, and data centers. He also highlights the company’s focus on in-house R&D, evolving client demands for REACH-compliant and recyclable materials, and the operational challenges of maintaining fire-resistant performance under India’s varied field conditions—all while integrating circularity into manufacturing.
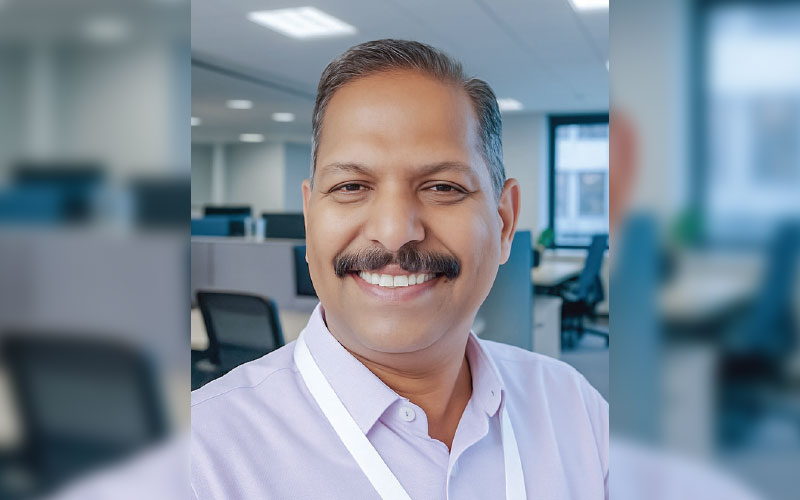
Wire & Cable India: Which specific Indian and international fire-resistance standards most significantly influence your material selection process, and how have these affected your compound sourcing since the 2022 electrical safety regulation amendments?
Praveen Paul: We comply with IS 7098 (Parts 1 & 2), IEC 60502-1 & 2, ASTM D2863, ASTM D2843, IEC 60754-1, SS 424-14-75, IEC 60332-1, IEC 60331-2, and IEEE 60383.
While no significant changes directly affecting compound sourcing were introduced in the 2022 amendments, the overall regulatory trend toward stricter fire safety has influenced our material selection and testing protocols.
WCI: Within your fire-retardant cable portfolio, which specific material systems deliver the optimal balance of BIS compliance, performance, and production efficiency in the Indian market?
PP: We primarily utilize low smoke zero halogen (LSZH) and halogen-free flame retardant (HFFR) compounds. These materials offer superior fire performance with minimal toxic emissions, align with BIS requirements, and meet growing demand from infrastructure and metro rail sectors. They offer an optimal balance between regulatory compliance, performance, and cost-effectiveness in the Indian context.
Watch: Top Cable Companies in India
WCI: Are you transitioning away from PVC in some applications? What drives these decisions at Laser Power & Infra Private Limited?
PP: Yes, we are steadily moving away from traditional PVC towards FRLSH and halogen-free compounds, particularly for insulation and outer sheath applications. Key drivers include updated BIS norms, metro rail and real estate specifications, and heightened fire safety requirements from export clients.
WCI: Did new fire-resistant compounds pose any manufacturing challenges in India’s climate conditions?
PP: Transitioning to halogen-free and cross-linkable fire-retardant materials has significantly improved our fire safety performance. However, it required equipment upgrades, climate control adjustments, and operator retraining to ensure extrusion consistency and maintain product integrity under Indian environmental conditions.
WCI: How do your material requirements vary across Indian Railways, commercial real estate, and data centers?
PP: Our material selection strategy is tailored to the specific requirements of each application segment. For Indian Railways, we use low smoke zero halogen (LSHZ) cables in tunnel environments and flame retardant low smoke halogen (FRLSH) cables for underground installations. In commercial real estate projects, the choice between LSZH and FRLSH depends on the installation type– whether cables are laid in ducts or exposed to open air.
For data centers, we deploy specialized solar or DC cables with enhanced fire-resistant properties to meet stringent safety demands. Additionally, regional material choices are often influenced by client or utility-specific safety mandates that go beyond standard BIS compliance.
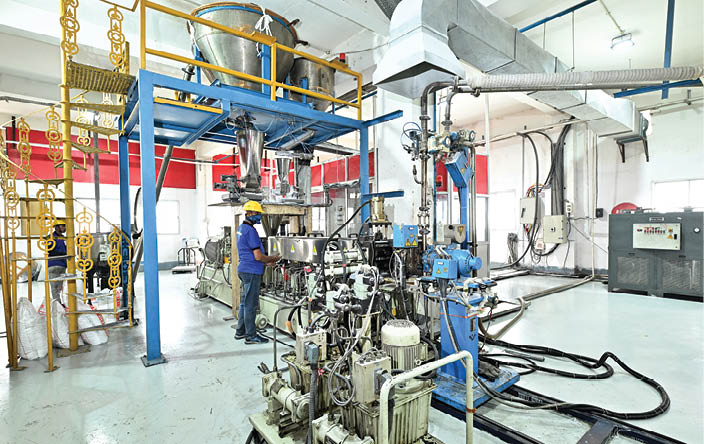
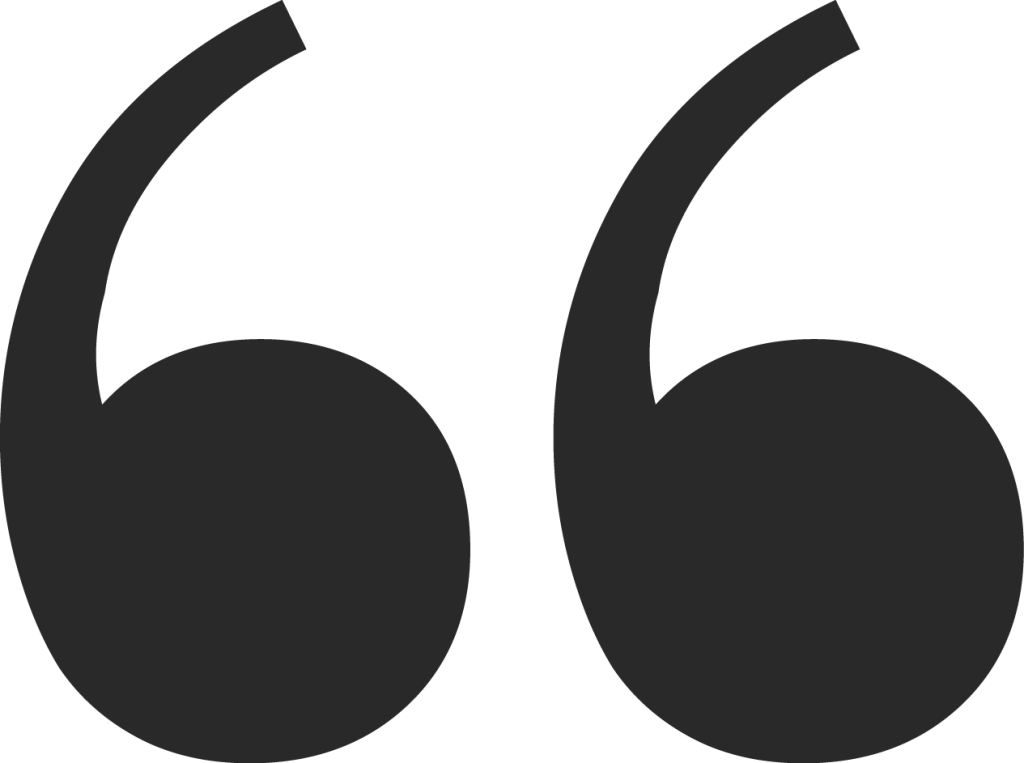
We are steadily moving away from traditional PVC towards FRLSH and halogen-free compounds, particularly for insulation and outer sheath applications.
WCI: Recent joint development agreements between polymer suppliers and cable manufacturers suggest deeper supplier-manufacturer partnerships in the Indian market. How extensively does your R&D team engage with domestic and international compound producers when developing cables for specific Indian project tenders? Could you describe a recent example where such collaboration proved particularly valuable?
PP: Although we do not have formal joint development agreements, our R&D team actively collaborates with select domestic and international compound suppliers when specific project performance criteria are involved.
One example includes custom formulations optimized for parameters such as oxygen index, smoke density, anti-tracking, thermal stability, and extrusion compatibility. Our in-house compounding facility allows rapid prototyping and iterative testing, enabling agility and IP control in development.
WCI: What trade-offs between fire safety, flexibility, and cost have been most challenging?
PP: We tailor our use of FR/FRLSH compounds based on specific flexibility and mechanical requirements. These materials typically offer mechanical properties comparable to PVC. So far, we have not encountered significant challenges in extrusion or flexibility within our production setup.
WCI: Are clients demanding specific certifications or materials like REACH or recyclable compounds?
PP: Yes, there’s a clear uptick in demand for halogen-free, REACH-compliant, and recyclable materials— particularly from clients like Tata Power.
This has required us to enhance our testing procedures, documentation practices, and traceability protocols to align with more stringent material qualification norms.
WCI: Which aspects of fire-resistant performance remain most challenging in Indian field conditions?
PP: Maintaining consistent fire barrier integrity under varied site conditions—especially in high temperature or underground settings—remains a challenge. For instance, BHEL and NTPC projects often mandate glass fiber tape for thermal shielding, impacting both material cost and compounding processes.
WCI: Which next-gen material features would most benefit in domestic and export markets?
PP: We seek materials that combine high-temperature resistance, superior flame retardancy, mechanical strength, and environmental compliance—without compromising on process efficiency.
Ceramic-reinforced compounds showing promise in these areas could be pivotal in scaling up our advanced fire-safe cable range for both domestic and export markets.
Also Read: Ddev’s WTR XLPE Caters to Safe Power Distribution in Humid Environments
WCI: What steps are you taking to ensure sustainability in your processes?
PP: As part of our backward integration efforts, we’ve implemented a closed-loop system that reprocesses in-house polymer waste into value-added products like packaging sheets.
This approach not only reduces landfill reliance but also supports internal material circularity. By upcycling waste, we minimize environmental impact and align with emerging e-waste and recycling regulations, positioning ourselves as a responsible, future-ready manufacturer.
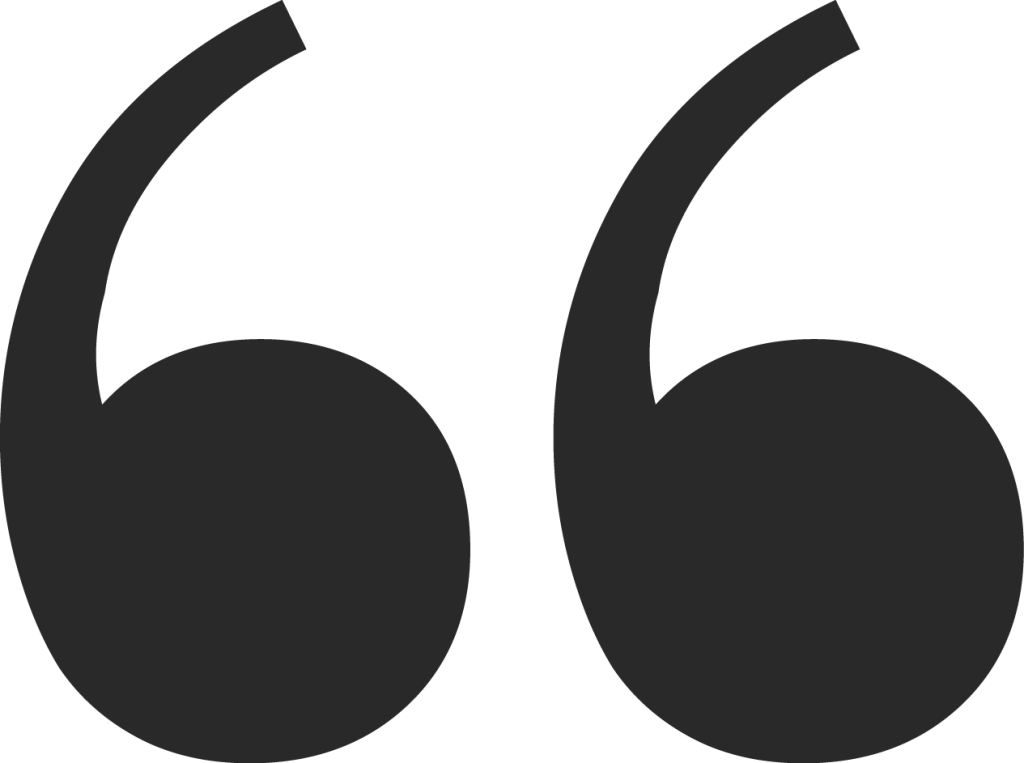
Ceramic-reinforced compounds showing promise in these areas could be pivotal in scaling up our advanced fire-safe cable range for both domestic and export market.