As fire safety and sustainability take center stage in modern infrastructure projects, Taprath Elastomers LLP is leading the charge with cutting-edge flame-retardant compound innovations. In this exclusive interview with Wire & Cable India, Mr. Abhishek Rathi, Founder and Director, shares how the company’s advanced LSZH/HFFR formulations meet high-speed extrusion compatibility and address the cable industry’s evolving needs. Notably, Taprath’s Electron Beam Cross-linkable (EBXL) flame retardant compounds offer superior compatibility with e-beam crosslinking technology, ensuring enhanced flame resistance and mechanical integrity. With a strong focus on compliance, processability, and next-gen materials, Taprath continues to be a trusted partner in global wire and cable advancement.
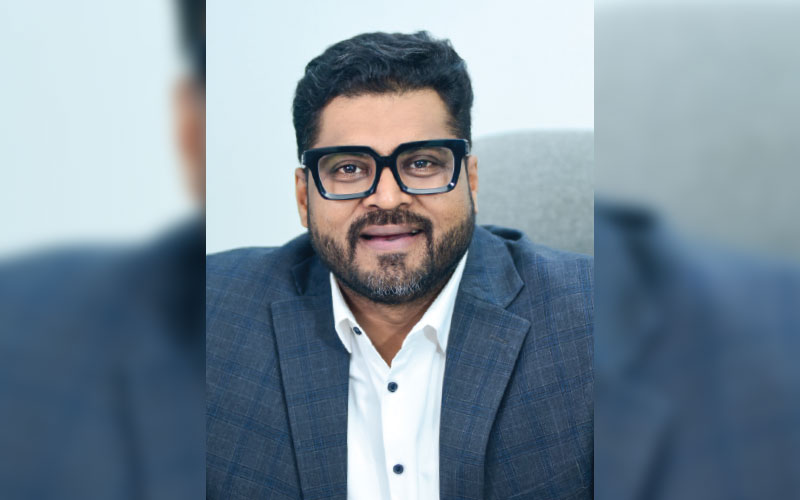
Wire & Cable India: As infrastructure projects like metro rails and smart cities expand with stricter fire safety protocols, which of your current compounds are specifically engineered to meet cable manufacturers’ fire performance requirements, and what cable types or sectors are they most suited for?
Abhishek Rathi: At Taprath, we’ve engineered a range of compounds to align with the evolving fire safety demands of infrastructure projects like metro rails, smart cities, and high-rise buildings. Our flagship solution in this space is our flame retardant (FR) LSZH/HFFR compounds, designed to ensure low smoke, zero halogen, and excellent flame resistance — crucial for public safety. These compounds are most suited for building wire, control and instrumentation cables, low voltage power cables, data and telecom cables, as well as railway signalling and metro applications.
In addition, our FR masterbatches for XLPE cables, offer outstanding flame retardancy for insulated power cables, making them ideal for tunnels, underground networks, and densely populated urban zones.
By offering both thermoplastic and cross-linkable solutions, Taprath supports cable manufacturers in meeting EN 50399, IEC 60332-1/3 and other key global standards (FT4, CPR Euro-class up to Cca) without compromising mechanical or electrical performance.
Watch: Top Cable Companies in India
WCI: The transition toward halogen-free solutions continues in the cable industry despite processing challenges in tropical manufacturing environments. How are you leveraging halogen-free flame retardants, mineral fillers like ATH or MDH, or phosphorus-based systems in your fire-safe formulations to align with cable manufacturers’ processing capabilities and fire safety needs?
AR: We recognise that the push toward halogen-free solutions—while critical for environmental and human safety—poses real processing challenges, especially in tropical and high-humidity manufacturing environments.
To overcome these hurdles, our LSZH/HFFR compounds are carefully formulated using optimised mineral fillers like ATH (Aluminium Trihydrate) and MDH (Magnesium Hydroxide) to deliver robust flame retardancy. These systems are fine-tuned for- low moisture absorption, improved dispersion, thermal stability during extrusion.
What sets our compounds apart is their processability on standard cable extrusion lines, with excellent surface finish, dimensional stability, and throughput — even under challenging humidity conditions.
Our in-house R&D ensures the formulations meet IEC 60332, EN 50267, and IEC 61034 requirements, while maintaining compatibility with existing manufacturing infrastructure. This balance of performance, safety, and manufacturability makes our solutions ideal for cable makers seeking to align with global fire safety norms without retooling their lines.
WCI: Cable manufacturers report varying levels of success with newer fire-resistant compounds in high-speed production environments. How do your fire-retardant compounds perform in high-speed extrusion or when used with crosslinking processes like e-beam or silane grafting?
AR: Taprath’s fire-retardant compounds are specifically engineered to excel in high-speed extrusion environments and advanced crosslinking processes such as electron beam (e-beam).
Our formulations are designed for thermal stability and excellent flow properties, ensuring smooth extrusion without degradation or surface defects, even at elevated line speeds. This enables manufacturers to maintain high throughput without compromising cable quality.
For cross linked cables, our electron beam cross-linkable (EBXL) flame retardant compounds provide superior compatibility with e-beam crosslinking technology. These compounds enhance their flame retardancy and mechanical integrity after crosslinking, meeting stringent fire safety standards required in sectors like railways, automotive, and smart infrastructure.
Additionally, our formulations minimise issues such as volatilisation and gel formation, which can otherwise hamper productivity during crosslinking. This ensures consistent processing and reliable final product performance.
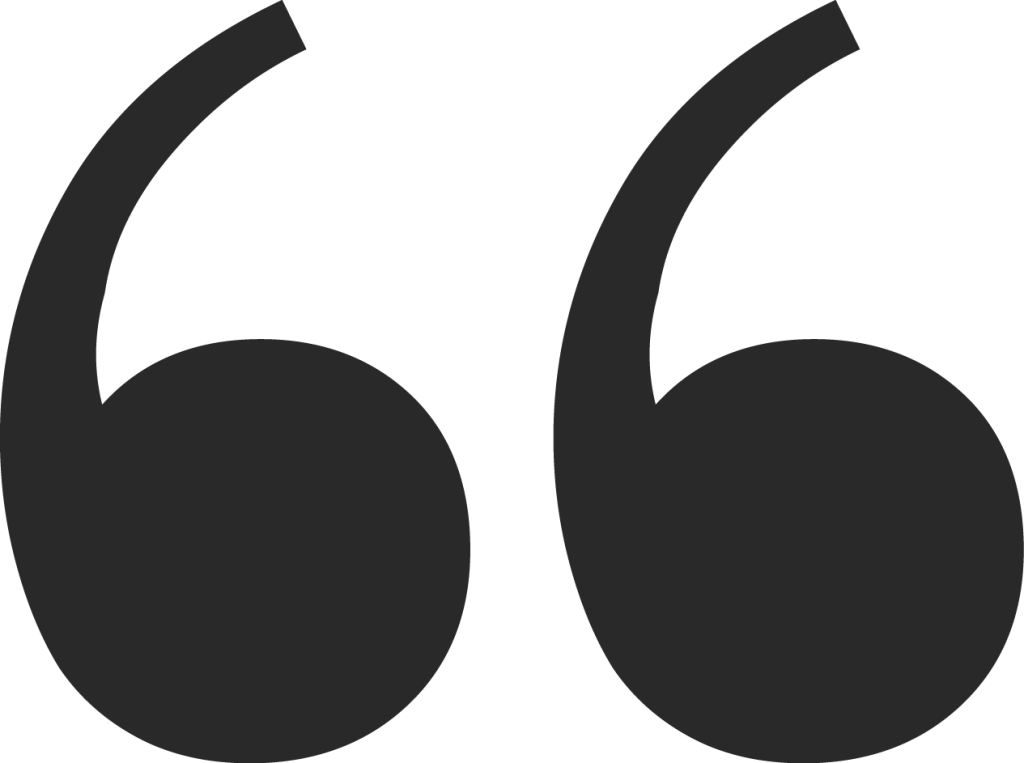
What sets our compounds apart is their processability on standard cable extrusion lines, with excellent surface finish, dimensional stability, and throughput — even under challenging humidity conditions.
WCI: Metro rail projects increasingly specify low smoke and toxicity requirements alongside mechanical durability standards. What breakthroughs have you made to help cable manufacturers in reducing smoke density and toxicity without compromising mechanical integrity in LSZH compounds?
AR: Taprath has made significant strides in developing LSZH compounds that balance stringent low smoke and toxicity requirements with robust mechanical durability — essential for metro rail and other critical infrastructure projects.
Our breakthrough lies in the strategic formulation of advanced halogen-free flame retardants combined with synergistic additives that not only suppress smoke generation but also reduce toxic gas emissions during combustion.
We use high-purity mineral fillers like ATH and MDH, carefully optimised to maintain excellent tensile strength, elongation, and abrasion resistance, ensuring cables withstand the mechanical stresses of installation and long-term operation.
WCI: Global export markets demand varying certification standards while domestic requirements continue evolving. Are your compounds developed and certified in direct response to cable manufacturers’ compliance needs for CPR Euroclass B2ca, C1A, or other international fire safety standards? How do you support them in regional compliance efforts?
AR: We understand that cable manufacturers face a complex landscape of evolving domestic and international fire safety regulations, including CPR Euroclass standards such as B2ca and C1A. Our compounds are developed with these certifications in mind, undergoing rigorous in-house and third-party testing to ensure compliance with EN 50575 and related standards. We tailor formulations to meet specific regional requirements, balancing performance parameters like flame retardancy, smoke density, and toxicity.
Beyond product development, we actively support manufacturers through technical collaboration, offering detailed compliance documentation, guidance on testing protocols, and assistance in navigating certification processes. This partnership approach helps able makers confidently access export markets while adhering to their local regulatory frameworks.
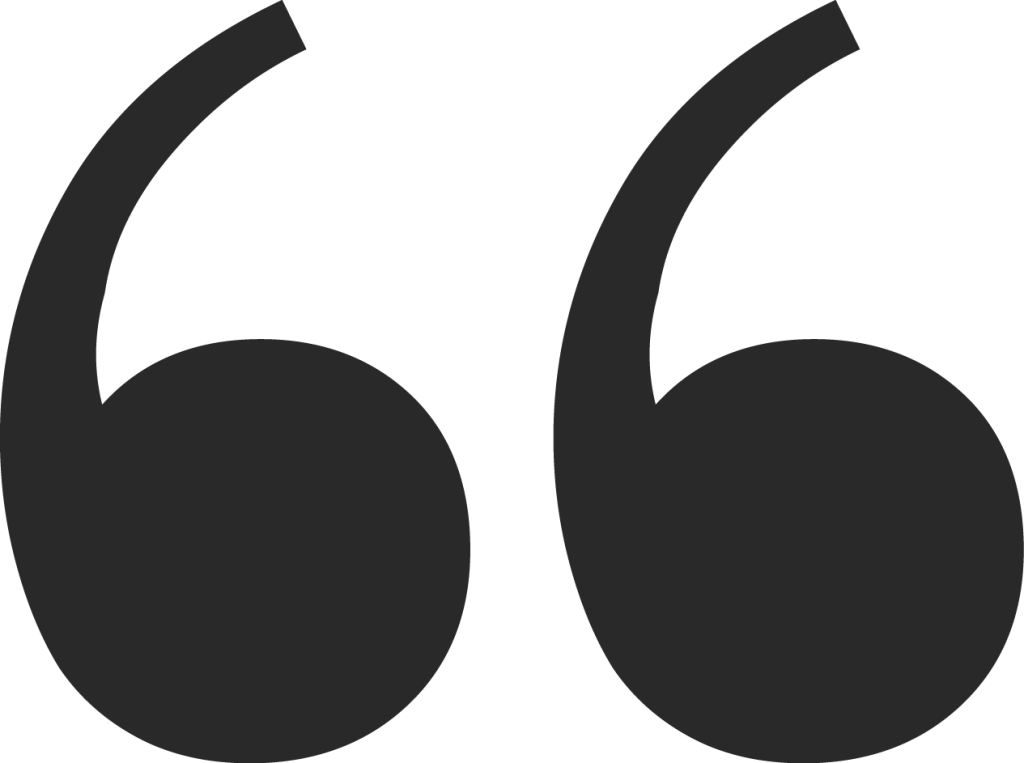
Our breakthrough lies in the strategic formulation of advanced halogen-free flame retardants combined with synergistic additives that not only suppress smoke generation but also reduce toxic gas emissions during combustion.
WCI: The tender specification process for infrastructure projects often requires collaborative material development. Can you share a recent example where you developed or customized a fire-retardant compound for a cable manufacturer’s specific project or tender requirement?
AR: Taprath prides itself on close collaboration with cable manufacturers to develop tailored fire-retardant compounds that precisely meet tender specifications for infrastructure projects. A recent example is our work with a leading appliance cable manufacturer who required a customised insulation compound that combined enhanced flame retardancy with improved flexibility and mechanical strength, while also adhering to strict low-smoke and toxicity norms.
Our R&D team worked hand-in-hand with their engineering and quality teams to optimize the formulation, ensuring compatibility with their extrusion and crosslinking processes, compliance with relevant fire safety standards, and robust performance under high-speed production conditions. The result was a compound that not only fulfilled the tender requirements but also improved overall cable durability and manufacturability, helping our customer secure the contract and accelerate project timelines.
WCI: Advanced material science applications are beginning to appear in commercial fire-resistant formulations. Are you working with nano-fillers, intumescent systems, or synergistic blends that go beyond traditional ATH-based flame retardants, specifically to enhance fire resistance in cables?
AR: We continually invest in advanced material science to push the boundaries of fire-resistant cable formulations beyond traditional ATH-based systems.
Our research focuses on synergistic blends that combine mineral fillers with nano-fillers and intumescent additives, enhancing flame retardancy while maintaining mechanical integrity and processability. These innovations help improve char formation for superior barrier effects during fire exposure, reduce total heat release and smoke density, and enhance thermal stability at elevated extrusion temperatures. By integrating these advanced materials, we provide cable manufacturers with next-generation compounds that meet increasingly stringent fire safety regulations and support high-performance applications such as metro rails, smart cities, and renewable energy sectors.
WCI: Circular economy principles are reshaping material selection processes throughout the value chain. How are you addressing environmental concerns in fire-retardant compounds—whether through halogen-free formulations, recyclable blends, or bio-based additives?
AR: At Taprath, sustainability is a core pillar of our innovation strategy, especially in developing fire-retardant compounds that align with circular economy principles.
We prioritise halogen-free formulations to reduce environmental and human health impacts, using mineral fillers like ATH and MDH that are abundant and non-toxic. Our compounds are designed for compatibility with recycling processes, enabling cable manufacturers to reclaim and reuse materials more effectively.
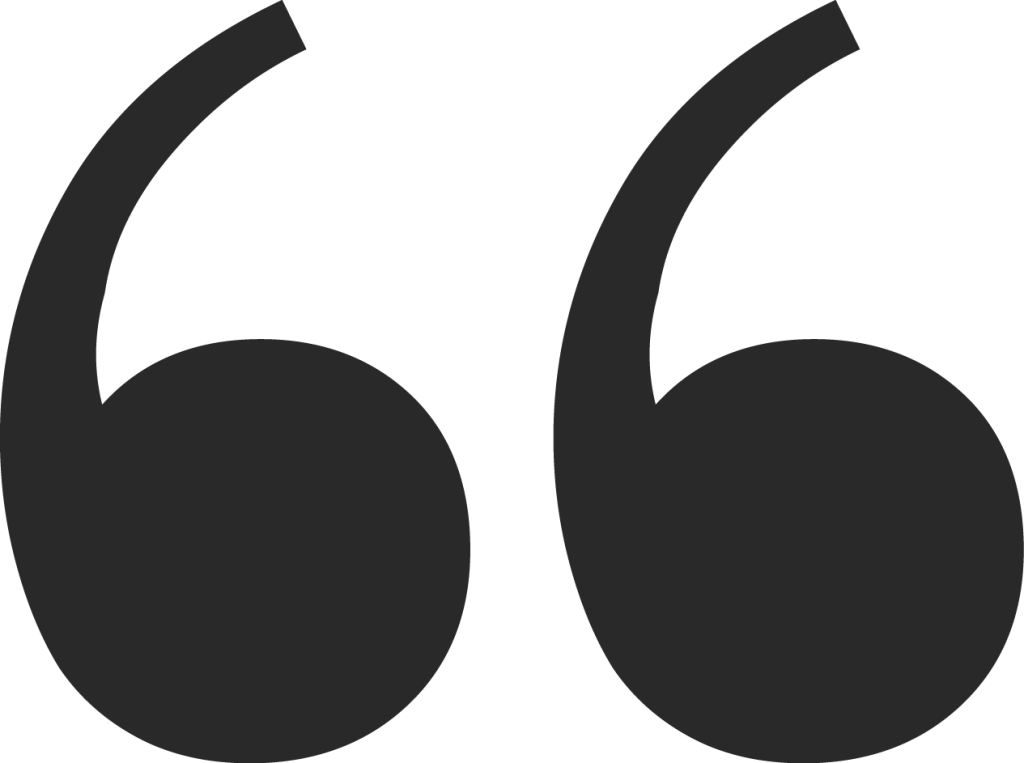
From a compounder’s viewpoint, the next big leap in fire-safety material science lies in developing multifunctional, eco-friendly formulations that combine superior flame retardancy with enhanced processability and durability.
WCI: The gap between laboratory certification and field performance remains a discussion point in industry forums. What kind of feedback do you typically receive from cable manufacturers regarding fire performance in terms of what works well and what still needs improvement?
AR: Feedback from cable manufacturers consistently highlights the strong correlation between our compounds’ lab-certified fire performance and reliable field results, particularly in controlled infrastructure environments like metro rails and smart cities.
Manufacturers appreciate our formulations’ consistent flame retardancy, low smoke emission, and mechanical durability during installation and operation. The compounds’ stability under high-speed extrusion and crosslinking also receives positive remarks.
However, there is an ongoing industry conversation about real-world variables—such as extreme environmental conditions, aging, and installation practices—that can influence long-term fire performance. Manufacturers express a need for enhanced long-term ageing resistance and improved performance under fluctuating temperature and humidity, especially in tropical climates.
Taprath is actively working to address these challenges through continuous R&D, field trials, and close collaboration with customers to refine formulations that not only meet certification standards but also excel in diverse operational conditions.
Also Read: Elementis: Fire-Retardant Synergists for Plastic Wires & Cables
WCI: Material science innovation continues driving performance advances while addressing processing challenges. From a compounder’s perspective, what’s the next big leap needed in fire-safety material science to meet the cable industry’s evolving needs?
AR: From a compounder’s viewpoint, the next big leap in fire-safety material science lies in developing multifunctional, eco-friendly formulations that combine superior flame retardancy with enhanced processability and durability.
This means creating intelligent synergistic systems that leverage advanced nano-fillers, bio-based additives, and next-generation intumescent materials to reduce environmental impact without compromising mechanical and electrical performance.
Another crucial area is improving thermal and ageing stability to ensure fire performance is maintained throughout the cable’s lifecycle — especially under harsh conditions found in tropical climates and urban infrastructure.
At Taprath, we’re focused on pushing these frontiers through ongoing R&D, partnerships, and a commitment to sustainable innovation.