In this exclusive interview with Wire & Cable India, Mr. Lalit Bansal, Managing Director, Universal Polychem India Private Limited sheds light on the company’s advancements in fire-safe and high-performance cable compounds. With a focus on LSZH, FRLS, HR, and XL-ZHFR compounds, the company caters to critical infrastructure and smart city demands. Their compounds are engineered for high-speed extrusion and silane crosslinking, and extreme temperature resilience. Emphasizing sustainability, they offer recyclable, halogen-free, and bio-based solutions aligned with global compliance standards. Backed by strong R&D and customer collaboration, Universal Polychem is also exploring smart materials for the next generation of multifunctional and self-monitoring cable systems.
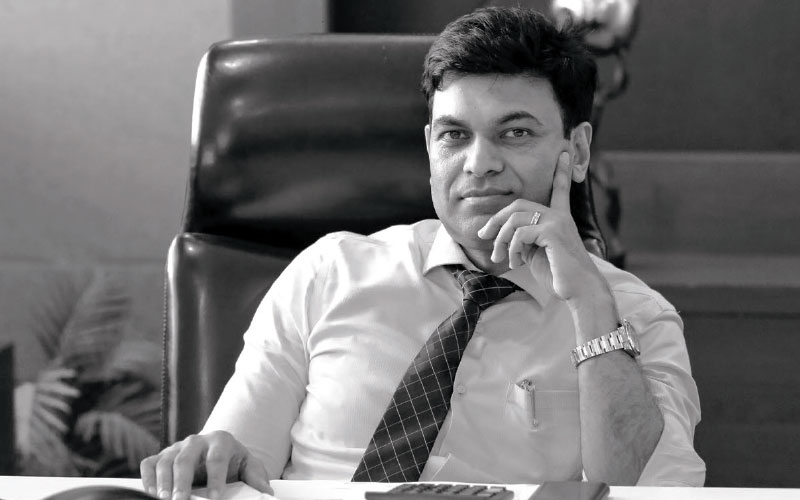
Wire & Cable India: As infrastructure projects and smart cities expand with stricter safety protocols, which of your current compounds are specifically engineered to meet cable manufacturers’ enhanced performance requirements, and what cable types or sectors are they most suited for?
Lalit Bansal: At Universal Polychem India Private Limited, we develop compounds that meet the highest safety standards for modern infrastructure. Our LSZH compounds are fire-resistant, low smoke and zero halogen compounds, making them ideal for high-rise buildings, airports, and tunnels. FRLS compounds offer flame retardancy with low smoke emission, specifically designed for residential, commercial, and industrial applications. For high-temperature environments, our HR compounds provide resistance up to 135°C, making them suitable for cables used in industrial and energy sectors.
Additionally, our XL-ZHFR compounds are cross-linked, zero halogen and flame-retardant compounds, tailored for high-performance cables in energy, transport, and critical infrastructure. These compounds ensure safety, performance, and compliance with stringent safety protocols.
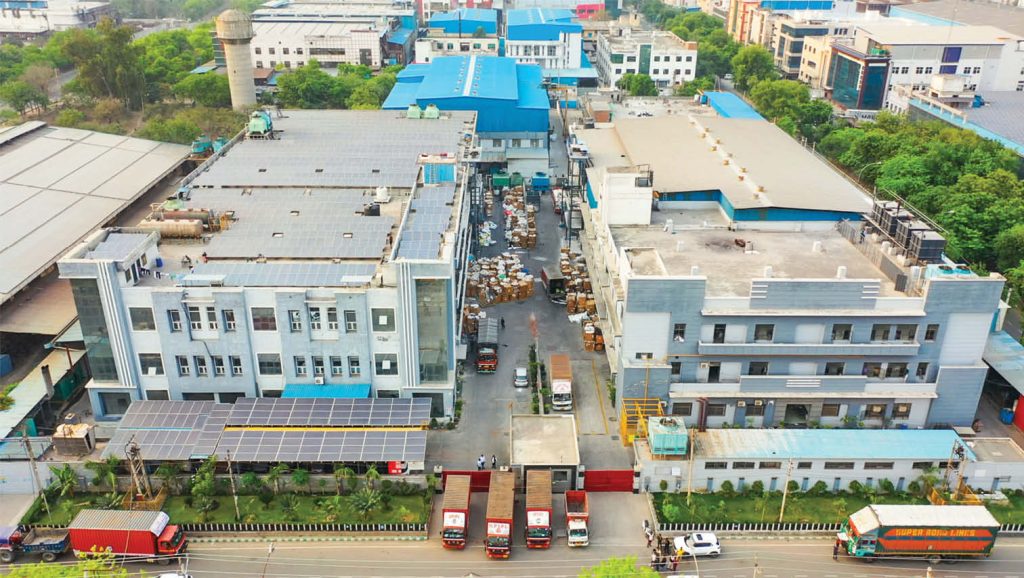
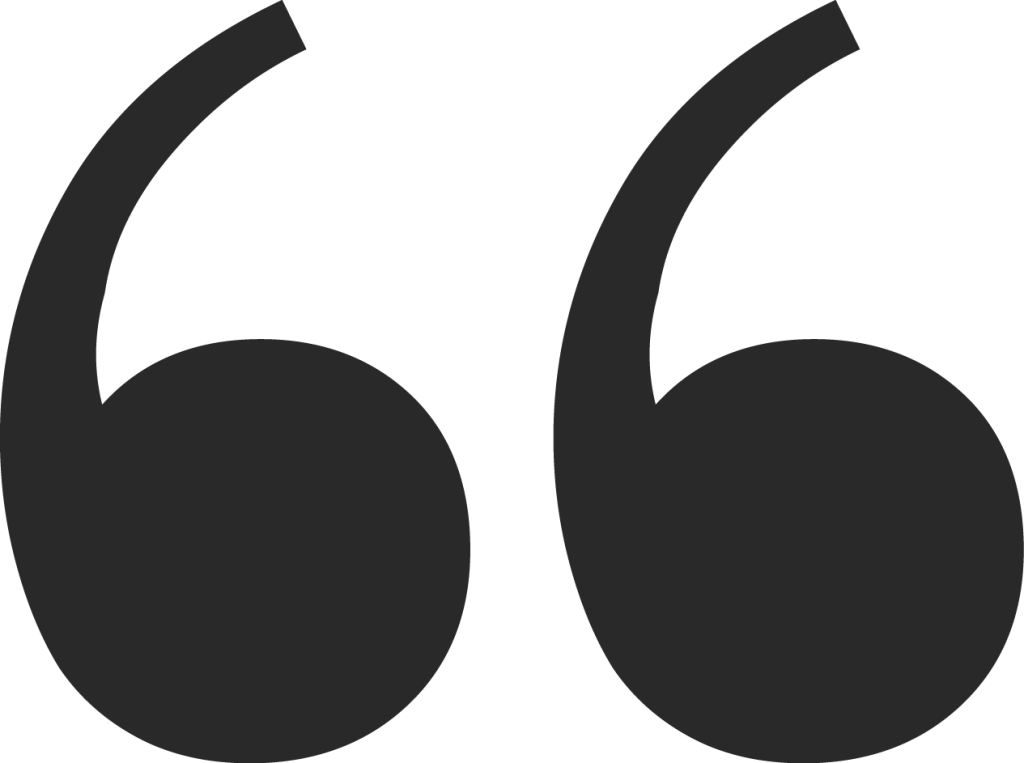
Notably, we customized XLPO compounds to withstand temperatures up to 250°C and XL-ZHFR compounds to operate safely at 250°C, ensuring the project met all technical and tender specifications.
WCI: Cable manufacturers report varying levels of success with newer compounds in high-speed production environments. How do your compounds perform in high-speed extrusion or when used with crosslinking processes like e-beam or silane grafting?
LB: Our compounds are currently optimized for high-speed extrusion. We are in the process of developing e-beam crosslinking technology, which will soon enhance our cables’ durability and performance in demanding environments. We expect this innovation to provide significant benefits, particularly in heat resistance and electrical performance, once fully integrated.
WCI: What breakthroughs have you made to help cable manufacturers in reducing smoke density and toxicity without compromising mechanical integrity in LSZH compounds?
LB: Our zero-halogen (LSZH) compounds reduce both smoke density and toxicity without compromising the mechanical strength of the cable. Our research team has developed a series of halogen-free formulation that significantly reduce the release of toxic gases during combustion, while maintaining superior mechanical properties like tensile strength and flexibility. We are constantly improving the formulation by incorporating non-toxic flame retardants and smoke-suppressing agents, ensuring that the cables remain compliant with global standards while enhancing safety in high-risk environments.
Watch: Top Cable Companies in India
WCI: Global export markets demand varying certification standards while domestic requirements continue evolving. Are your compounds developed and certified in direct response to cable manufacturers’ compliance needs? How do you support them in regional compliance efforts?
LB: Yes, our compounds are developed with a keen understanding of both global export certifications (e.g., UL, IEC, BS, CE) and domestic compliance standards in India (e.g., BIS IS 7098, IS 5831). We continuously monitor regulatory updates to ensure that our products are always ahead of the curve. To assist cable manufacturers, we provide them with the necessary support during the testing and approval processes, ensuring they meet local and international requirements. Additionally, we have a dedicated compliance team that works closely with manufacturers to streamline their certification efforts, providing technical support and guidance where needed.
WCI: The tender specification process for infrastructure projects often requires collaborative material development. Can you share a recent example where you developed or customized a compound for a cable manufacturer’s specific project or tender requirement?
LB: We recently collaborated with a leading cable manufacturer on a government infrastructure project, where the client required a custom compound for cables to withstand extreme temperatures. We developed a high-performance, temperature-resistant compound that met fire-resistance standards, with enhanced flame retardancy and mechanical resilience. Notably, we customized XLPO compounds to withstand temperatures up to 250°C and XL-ZHFR compounds to operate safely at 250°C, ensuring the project met all technical and tender specifications.
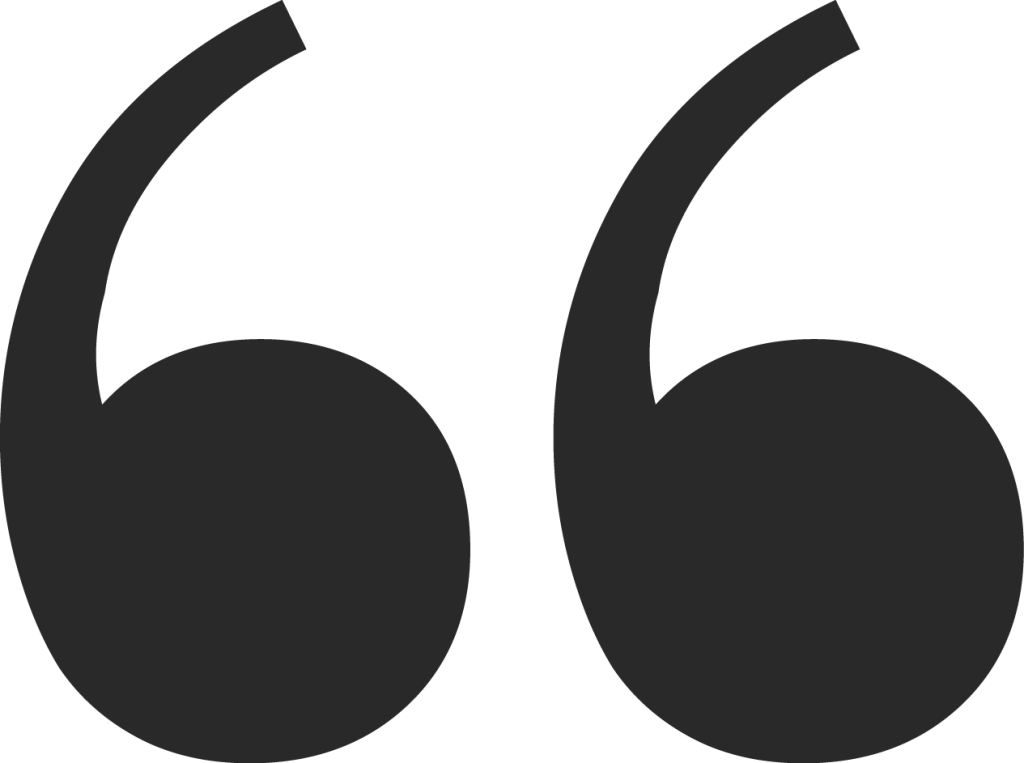
We are closely monitoring advancements in smart polymers and sensor-embedded materials that could enable cables to detect faults or degradation in real-time and trigger corrective action.
WCI: Advanced material science applications are beginning to appear in commercial cable formulations. Are you working with advanced technologies or synergistic blends that go beyond traditional compounds, specifically to enhance performance in cables?
LB: Yes, we are seeing a significant shift toward advanced technologies and synergistic blends that go beyond traditional compounds in the cable industry. These innovations are primarily aimed at improving performance, reliability, and sustainability, particularly for high-performance cables. In rubber compounds, we are working with high-performance EPDM blends that offer improved thermal stability and UV resistance for outdoor applications, along with carbon nanotube (CNT) integration to enhance electrical conductivity and mechanical strength for more durable, lighter cables.
In PVC compounds, our developments include halogen-free formulations for safer, low-smoke, flame-retardant applications, PVC-TPE blends for enhanced flexibility and impact resistance, and recyclable PVC that promotes sustainability without compromising performance. The cable industry is rapidly embracing these advancements to meet evolving demands, enabling cables to perform more effectively in challenging environments with improved thermal stability, mechanical strength, environmental resistance, and sustainability.
WCI: Circular economy principles are reshaping material selection processes throughout the value chain. How are you addressing environmental concerns in compounds—whether through halogen-free formulations, recyclable blends, or bio-based additives?
LB: We are fully committed to sustainability and actively contribute to the circular economy by developing halogen-free formulations, recyclable blends, and bio-based additives. Our team has been working on bio-compounds that incorporate renewable resources like plant-based plasticizers and biodegradable stabilizers. Additionally, we ensure that all our formulations are halogen-free and can be recycled at the end of the cable’s life cycle. This ensures compliance with international environmental regulations and reduces the carbon footprint of our products, supporting both manufacturers and end-users in their sustainability goals.
Also Read: Wanma’s Advanced Cable Compounds Enhance Fire Safety and Processing Efficiency
WCI: The gap between laboratory certification and field performance remains a discussion point in industry forums. What kind of feedback do you typically receive from cable manufacturers regarding performance in terms of what works well, and what still needs improvement?
LB: We regularly receive valuable feedback from cable manufacturers, particularly in terms of real-world performance. While laboratory testing provides essential certification, the actual field performance often reveals nuances related to long-term durability, flexibility under harsh conditions, and processing efficiency. Many manufacturers have expressed satisfaction with our flame retardant and smoke suppression capabilities; however, ongoing feedback highlights the need for improving weather resistance for outdoor cables, as well as enhancing processing speed in some of our compounds. This feedback is instrumental in guiding our continuous R&D efforts.
WCI: Material science innovation continues driving performance advances while addressing processing challenges. From a compounder’s perspective, what’s the next big leap needed in material science to meet the cable industry’s evolving needs?
LB: The next big leap in material science for the cable industry lies in the development of multi-functional materials that can not only withstand extreme environmental conditions but also self-monitor and self-repair under certain stressors. We are closely monitoring advancements in smart polymers and sensor-embedded materials that could enable cables to detect faults or degradation in real-time and trigger corrective action.
We remain committed to providing high-performance, safe, and sustainable solutions for our partners in the wire and cable industry.