Mikrotek Machines Limited, having a monthly capacity of 40,000 wire drawing dies, has made significant strides with the creation of high-speed wire polishing machines tailored for super fine wire sizes. The company has also developed Tungsten Carbide (TC) die working machines capable of handling wire sizes as small as 0.1 mm and Diamond Coated (DC) dies designed specifically for steel wire drawing, compacting and stranding of cables. In an exclusive interview with Wire & Cable India, Mr. B. Kamal Babu, Managing Director, Mikrotek Machines Limited, shares insights into these innovations and how they drive the wire drawing operations.
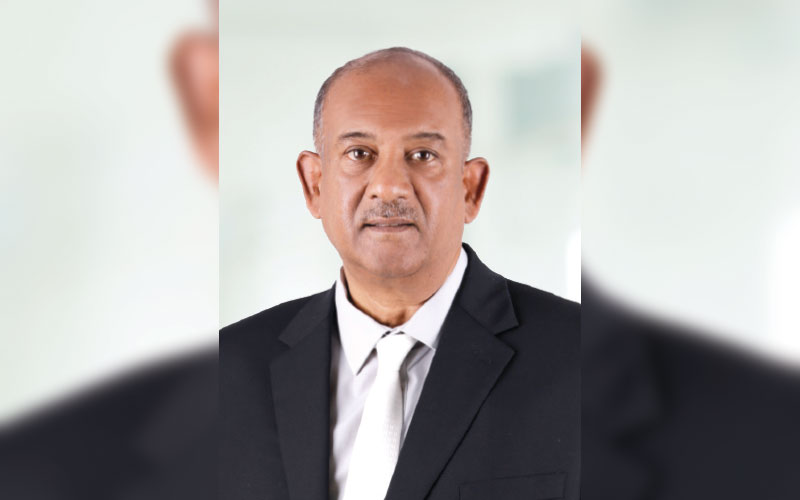
Wire & Cable India: Please tell us about your company’s history, significant milestones, and crucial achievements.
Kamal Babu: Mikrotek Machines Limited was founded in 1993, by technocrat Mr. B. Kamal Babu, who was specially trained in Germany and Switzerland in bringing the latest technology to India. The company has set up over 1,000 die shops globally and sold more than 3,000 plus die polishing machines which is a record achievement for a single company.
Headquartered in Bengaluru, Karnataka, Mikrotek specializes in manufacturing wire drawing dies and die polishing equipment. With over 32-year of experience, the company has established itself as a leader in high precision wire drawing dies and tooling, catering to both domestic and international markets.
Starting with a production capacity of a mere 750 dies per month, Mikrotek now boasts its production capacity of 40,000 dies per month, which is the one of the largest production facilities globally.
For over 30 years, we have been delivering our premium wire drawing dies with trusted quality and precision, directly contributing to a better wire surface, accuracy, and metallurgical properties.
Mikrotek has established a majority of die rooms in the wire industry in India, solidifying its position as a dominant player partnering with several drawing plants.
Mikrotek has won several prestigious awards, including: “Most Promising Manufacturer” by IBN7 and CNN IBN, “Quality Manufacturer” award from International Product and Services, four international awards from the International Wire and Machinery Association.
Watch: Top Cable Companies in India
WCI: What sets your dies apart in terms of material composition, performance, and longevity?
KB: Mikrotek’s wire drawing dies stand out due to their superior diamond selection, performance, and longevity.
We use only high quality diamonds in our dies. For example, our natural diamond dies are made from Kimberly Process certified flattened diamond crystals with pre-ground 111 plane orientation. Our polycrystalline diamond (PCD) blanks are sourced from popular manufacturers, mainly Sandvik Hyperion and other reputed manufacturers. We make sure each and every raw material received to us is inspected thoroughly before issuing to the manufacturing processes.
Our Solid Rock Technology for diamond mounting ensures maximum strength and thermal stability, resulting in blemish-free wire surfaces and good lustre. Our strict quality control allows us to inspect each and every die at every significant step in the processing of these dies and before dispatch to the customer.
Mikrotek provides comprehensive reconditioning and repolishing services that restore dies to near-new condition, extending their lifespan. This provides a big boost in the Indian cable industry to operate their high speed machines with highest efficiency.
Our dies are tailored to specific customer needs with the help of our technical experts, enhancing durability and performance over time.
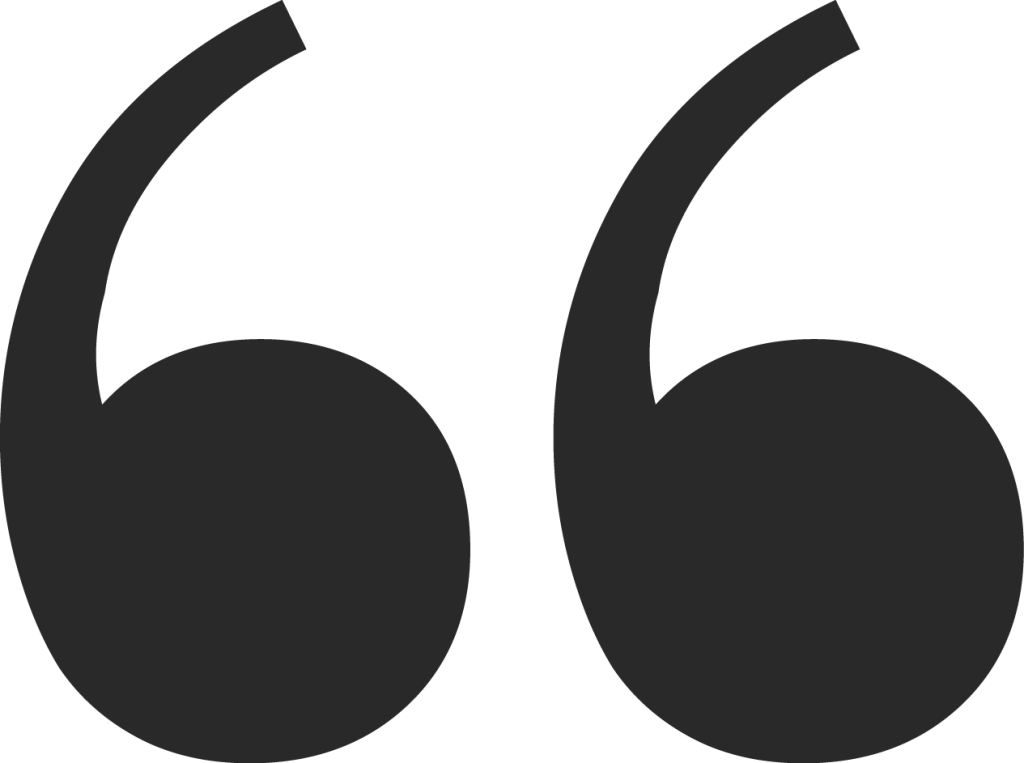
Mikrotek provides comprehensive reconditioning and repolishing services that restore dies to near-new condition, extending their lifespan.
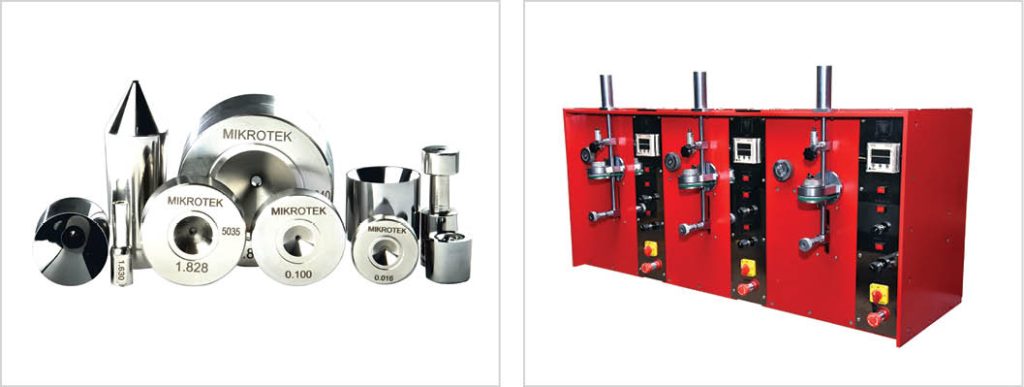
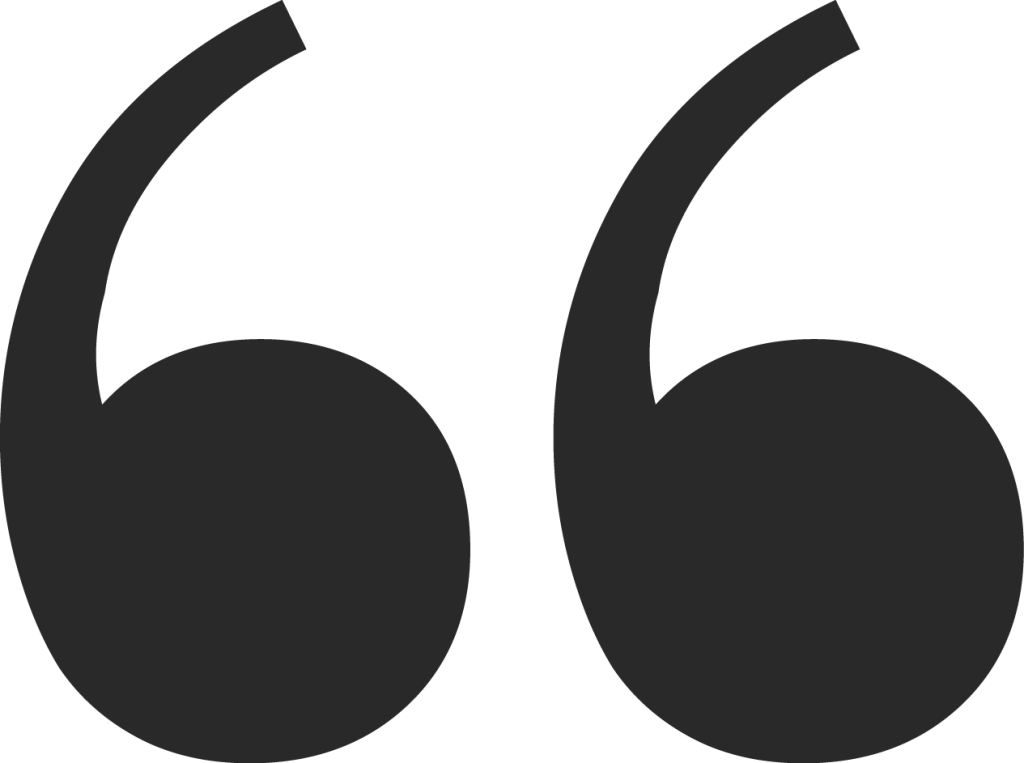
The Solid Rock Technology for diamond mounting ensures maximum strength and thermal stability, resulting in blemish-free wire surfaces and good lustre.
WCI: Please shed light on your product portfolio. How do you ensure that your products & services are tailored to meet the unique needs of your customers?
KB: Mikrotek offers a large and diverse portfolio, having a comprehensive range of products including wire drawing dies, die-shop equipment, consumables, inspection equipment, etc. tailored to the wire drawing industry. The majority of this manufacturing is done in-house.
In wire drawing dies, we have natural diamond dies, polycrystalline diamond (PCD) dies, mono diamond (SSCD) dies, tungsten carbide (TC) and TC taper inserts, diamond coated (DC) dies, solid enameling dies and many more. Our dies are known for precision, durability, and cost efficiency.
In die-shop equipment, we produce a complete range of die working equipment, namely, ultrasonic die polishing machines (USBNG 250, USBNG 300), wire polishing machines (WPF1S, 2S, WPA1S, 2S, 3S and WPAB1S), TC die working machines (MTCA 10 Vertical, MTCBRG 6 Vertical, MTCHA 10, MTCG), which are used to maintain the die shops effectively.
The machines are designed for Indian working conditions, substituting imported machines. These machines are time tested and the preferred choice of the wire industry.
In consumables, we supply diamond powders, diamond suspension, and diamond paste for polishing, and accessories like grinding pins and diamond needles for grinding of TC dies.
We also supply digital diameter gauges for quick size checks and specially designed microscopes for die profile visualization.
Mikrotek specializes in turnkey projects and provides on-site die repolishing and reconditioning to repair dies to bring them to near-new condition.
The company ensures its products meet unique customer needs by a number of steps which include: Customizing dies and equipment based on specific applications; offering complete package for setting up die shops which include technical know-how, machines supply, installation, training, and periodic maintenance; partnering with wire and cable companies to improve the wire quality, die lifespan and thereby overall plant efficiency; regularly conducting technical symposiums along with industry experts near customer hotspots and sharing latest technical developments across the wire and cable industry.
Also Read: Ajex & Turner: One-Stop Powerhouse for Wire Drawing Dies
WCI: Can you share some of the innovations or recent developments undertaken by your company?
KB: Mikrotek is committed to continuous innovation and customer-centric advancements through its in-house R&D facility. Recent developments include the creation of high-speed wire polishing machines designed for super fine wire sizes, along with feedback ultrasonic generators for ultrasonic diamond die working machines.
Additionally, Mikrotek has developed tungsten carbide (TC) die working machines capable of handling sizes as small as 0.1 mm, needle grinders with 0.1-degree accuracy, GHCS sizing pins, and digital diameter gauges.
Mikrotek also supplies optical wire coloring dies that play a vital role in fiber manufacturing by color-coding individual fibers for easy identification and organization in telecom and data networks. They feature low attenuation, ensuring uniform coating without impacting signal quality, high heat and UV resistance, thanks to optimized geometry that withstands fiber drawing temperatures and environmental conditions.
Our portfolio also has split dies, which are recommended to significantly reduce the set-up time of stranding machines compared to conventional dies. The use of split dies minimizes the need to rethread the machine when changing dies.
Mikrotek continuously strives to improve its product offerings that may benefit our customers. Recently, we introduced Diamond Coated dies for steel wire drawing dies and compacting and stranding of cables. Carbon Vapor Deposition (CVD) is coated on special carbide nibs, a process where a carbon layer is deposited on the tungsten carbide die profile. This coating ensures minimum friction and a good wire surface finish resulting in up to 20x longer die life compared to bare tungsten carbide dies. Also, this has become a superior alternative to PCD dies used for stainless steel wrought drawing.
Recognizing the need for quicker response times and faster deliveries in the wire drawing industry, Mikrotek has implemented internal organizational changes to better align with customer expectations. These efforts underline Mikrotek’s dedication to improving product quality and operational efficiency for its customers.