RR Kabel is steadily transitioning to Low Smoke Zero Halogen (LSZH) materials across its cable manufacturing operations. Partnering with domestic and international suppliers, RR Kabel is formulating advanced compounds that meet stringent international safety standards. In an exclusive interview with Wire & Cable India, Mr. Shreegopal Kabra, Promoter & President of RR Global, shares that the company, leveraging its R&D and in-house compound manufacturing and testing facilities, is exploring ceramic-reinforced compounds, along with bio-based, biodegradable insulation materials and cellulose-based compounds, underscoring RR Kabel’s vision to lead the industry into a safer, greener, and more sustainable future.
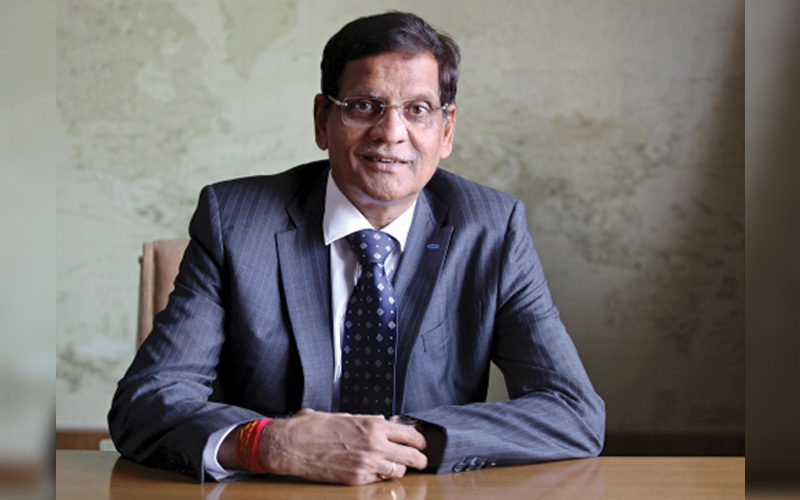
Wire & Cable India: Which specific Indian and international fire-resistance standards most significantly influence your material selection process, and how have these affected your compound sourcing since the 2022 electrical safety regulation amendments?
Shreegopal Kabra: Our compound sourcing has consistently aligned with key fire-resistance standards. These include IS 17505-1: for thermosetting insulated fire survival cables (up to 1100 Vac / 1500 Vdc) with low smoke and corrosive gas emissions; BS 7846: covering thermosetting insulated armoured fire-resistant cables (600/1000V); BS 7629-1: for fire-resistant screened cables (300/500V) used in fixed installations like fire alarms; and IS 17048: for LSZH single and multi-core wires and cables.
These standards emphasize fire resistance, low smoke emission, and zero halogen properties, pushing us to shift towards high-performance thermosetting and LSZH compounds.
When sourcing, we prioritize materials that meet stringent criteria for fire resistance, almost zero toxicity & zero smoke, ensuring both compliance and enhanced safety in critical applications like fire alarms, power cables, and general wiring.
Collectively, these standards have not only reshaped our compound sourcing strategy—focusing on certified, high-performance, and sustainable materials—but also helped us future-proof our products against evolving safety expectations in infrastructure, industrial, and residential applications.
WCI: Industry reports indicate a major shift toward LSZH materials among leading manufacturers, with premium brands reaching significant implementation, especially in their building wire segments. Within your fire-retardant cable portfolio, which specific material systems (such as LSZH, halogen-free flame retardants, or thermoset compounds) deliver the optimal balance of BIS compliance, performance and production efficiency in the Indian market?
SK: We adhere to IS 17048 standards for Halogen Free Flame Retardant (HFFR) cables. Within our fire-retardant cable portfolio, we have adopted Low Smoke Zero Halogen (LSZH) material systems as our preferred solution—particularly for building wires, panel wires, and commercial infrastructure applications.
This strategic shift not only ensures compliance with BIS regulations but also addresses the increasing industry demand for safer, low-toxicity cable solutions. LSZH materials deliver an optimal balance of safety, performance, and production efficiency, making them the ideal choice for today’s safety-conscious Indian market.
Watch: Top Cable Companies in India
WCI: Industry reports suggest a gradual shift away from traditional PVC compounds in various cable applications, with first-tier manufacturers decreasing usage by a significant proportion. Are you implementing similar transitions in your manufacturing operations? What specific combination of factors—BIS regulations, export requirements, metro rail specifications, or technical advantages—drives these material decisions?
SK: We are progressively phasing out traditional PVC compounds and actively transitioning to Low Smoke Zero Halogen (LS0H) materials across our cable manufacturing operations. This strategic shift reflects both the evolving needs of the industry and our commitment to delivering safer, more advanced cable solutions. This shift is driven by:
BIS Regulations: With ongoing updates to BIS standards, there is an increased focus on fire safety, reduced smoke emission, and the use of halogen-free materials. LS0H compounds enable us to stay ahead of these regulations by offering superior flame resistance and a lower environmental impact.
Export Market Demands: International markets—particularly in Europe and the Middle East—enforce strict safety and environmental requirements, including RoHS, REACH, and CPR compliance. Adopting LS0H materials ensures our cables meet these standards, enhancing their suitability to meet EPD (environmental product declaration) and competitiveness in the global market.
Metro Rail and Urban Infrastructure Projects: Major infrastructure projects such as metro rail networks, airports, and commercial complexes now mandate cables that minimize toxic smoke and support safe evacuation during fire emergencies. LS0H cables are specifically engineered to meet these requirements, making them the preferred choice for such critical applications.
Technical Advantages: Beyond regulatory compliance, LS0H materials offer excellent thermal stability, low corrosive gas emission, and extended service life. These attributes translate into improved performance and reliability, particularly in high-risk or densely populated environments.
Our transition to LS0H is not merely about regulatory compliance—it is a proactive step to enhance safety, support sustainable infrastructure development, and ensure our products are well-positioned for both domestic and international markets.
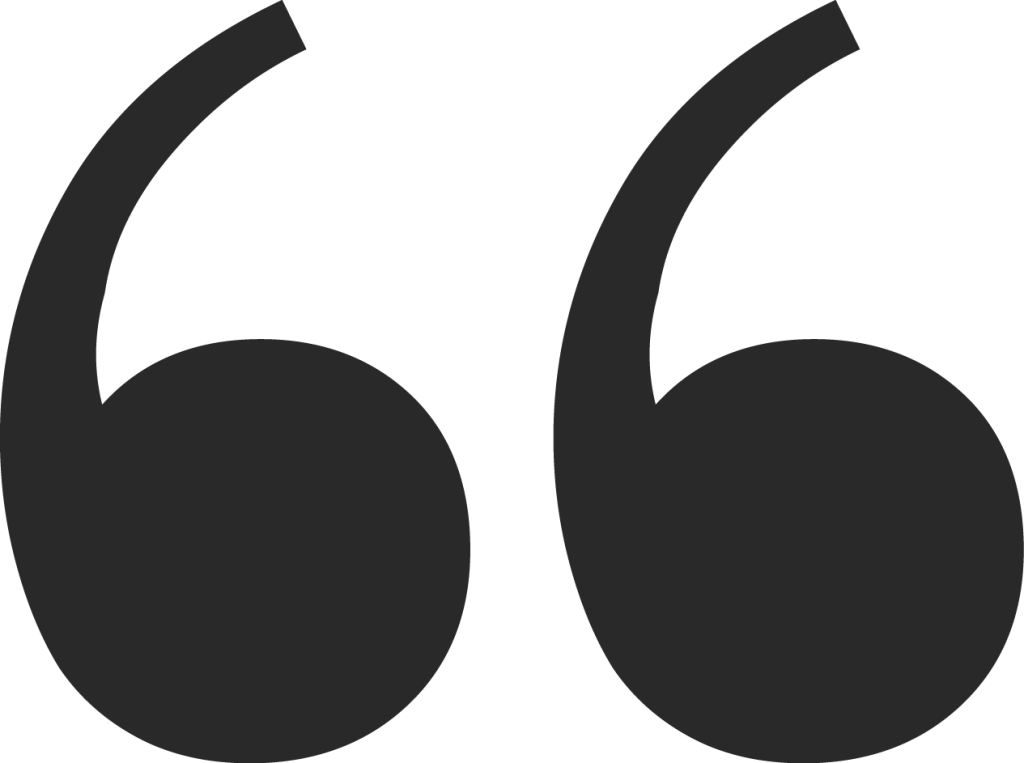
End users and original equipment manufacturers (OEMs) are now looking beyond basic fire resistance, and are asking for additional certifications like halogen-free (LS0H) materials, RoHS & REACH compliance, CPR classifications, and even recyclable insulation and sheathing.
WCI: Manufacturing adaptations are often necessary when implementing new fire-resistant formulations. Did new fire-resistant compounds (like cross linkable halogen-free materials or blends with high filler loadings) create any challenges in your extrusion or compounding lines, particularly given India’s operating temperatures and humidity conditions?
SK: Owing to our state-of-the-art manufacturing technologies, including electron beam (E-Beam) processing, we are able to ensure high-quality crosslinking with excellent consistency.
Every new product goes through a strong R&D and product management system, which includes in-house compound manufacturing, cable design, and development.
We also carry out rigorous testing in IS/ISO/IEC 17025-accredited labs to ensure full compliance and reliable performance—even in India’s varied temperature and humidity conditions.
Our processes are well-equipped to handle these innovations, ensuring that quality and safety are never compromised.
WCI: Leading infrastructure cable suppliers have adopted segmented approaches with distinct material specifications across power, building, and telecommunications portfolios. How do your fire safety material requirements differ between projects for Indian Railways, commercial real estate developments, and data center installations? What regional considerations drive these distinctions beyond basic BIS compliance?
SK: We have adopted a segmented approach to fire safety materials, tailoring our specifications to the unique requirements of each sector. While BIS compliance forms the foundation of our process, we go beyond regulatory standards to address the specific risks, environments, and operational demands of every project.
For example, projects in the Indian Railways sector demand materials that can withstand vibration, elevated temperatures, and prolonged operational hours. We utilize high-performance, fire-resistant materials that ensure durability and low smoke emissions, particularly in enclosed or high-traffic areas.
In commercial real estate such as in high-rise buildings and commercial complexes, the priority is safe evacuation, minimal smoke, and low toxicity during fire incidents. Here, we rely on Low Smoke Zero Halogen (LS0H) materials to enhance safety in densely populated, urban environments.
In data centers, given the critical importance of uptime and the sensitivity of equipment, we select materials that provide thermal stability, low corrosive gas emissions, and fire resistance—safeguarding both people and infrastructure.
Lastly, we consider regional factors such as humidity, temperature extremes, and urban density to ensure that our fire safety solutions are not only compliant but also engineered for reliability, resilience, and long-term safety in real-world conditions.
WCI: Recent joint development agreements between polymer suppliers and cable manufacturers suggest deeper supplier-manufacturer partnerships in the Indian market. How extensively does your R&D team engage with domestic and international compound producers when developing cables for specific Indian project tenders? Could you describe a recent example where such collaboration proved particularly valuable?
SK: For us, the supplier-manufacturer partnership is not a challenge—owing to our comprehensive in-house R&D and compound manufacturing facilities, covering both thermoplastic and thermoset materials. This vertical integration gives us end-to-end control over the development process and allows us to respond swiftly and effectively to the specific requirements of Indian project tenders.
While our internal capabilities are strong, we remain open to strategic collaborations with domestic and international partners whenever such partnerships enhance our ability to deliver safer, more efficient, and higher-performing cable solutions.
WCI: Enhanced fire performance often affects other material properties; for example, enhancing fire retardancy in cable materials can impact flexibility. When balancing fire performance against mechanical properties and cost factors crucial in the Indian market, which specific trade-offs have proven most challenging, and how have you addressed them?
SK: Our ongoing R&D and innovation in our in-house compound manufacturing and testing processes enables us to ensure that there are no compromises in our offerings. We focus on customizing solutions based on where and how the cable will be used. This way, we can maintain safety without compromising on flexibility or cost.
For more demanding applications, we also work closely with top-quality material suppliers from Europe, the UK, and the USA. Their expertise helps us create advanced compounds that meet high safety standards while still performing well in the field. Overall, it’s about finding the right mix for each use-case—keeping our cables safe, reliable, and cost-effective.
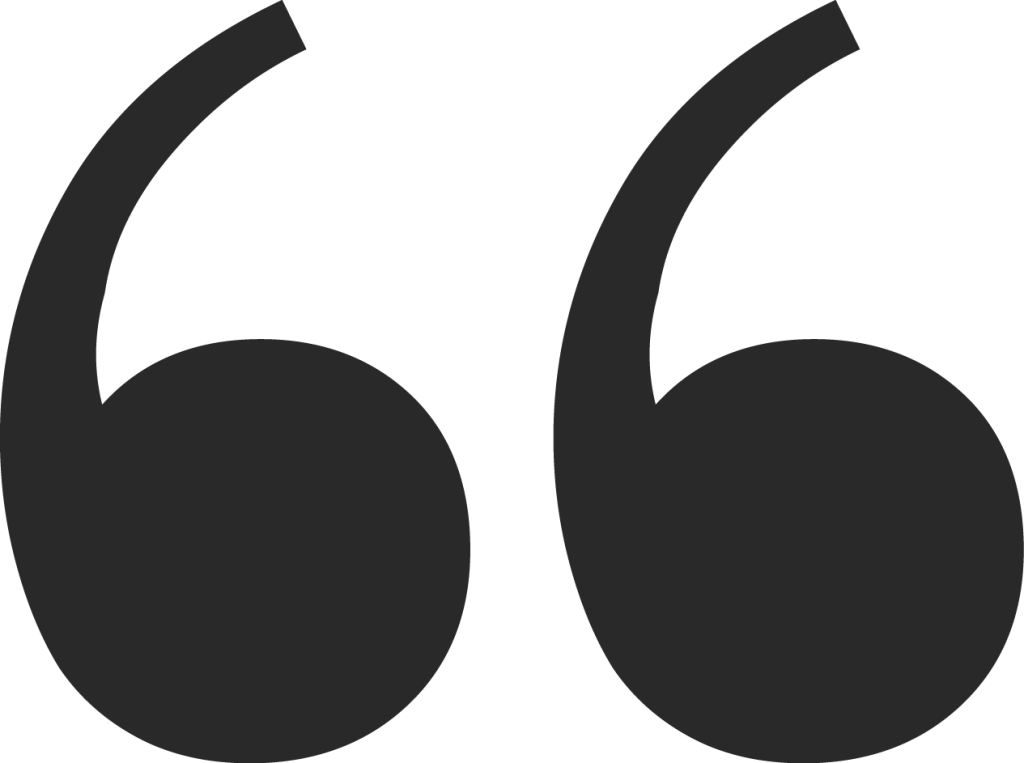
In India, the demand for stricter certifications is being driven mostly by export-focused manufacturers, data centers and IT parks, and high-end commercial real estate and smart buildings.
WCI: Project specifications increasingly include specific fire-resistance requirements beyond standard compliance. Have end users or OEMs started demanding specific certifications or materials—like halogen-free, REACH-compliant, or recyclable options—for fire-resistant cables? Which specific client segments in India are driving more stringent certification requirements, and how has this affected your material qualification and testing processes?
SK: End users and original equipment manufacturers (OEMs) are now looking beyond basic fire resistance, and are asking for additional certifications like halogen-free (LS0H) materials, RoHS & REACH compliance, CPR classifications, and even recyclable insulation and sheathing. This is especially common in infrastructure and export-oriented projects, where system compliance with standards like ISO 9001, ISO 14001, and ISO 45001 is also expected.
In India, the demand for stricter certifications is being driven mostly by export-focused manufacturers, data centers and IT parks, and high-end commercial real estate and smart buildings
As customer’s expectations evolve, it defines the way we handle material approvals and testing. We’ve upgraded our in-house test protocols to include checks like halogen content analysis, smoke density, toxicity levels, and REACH chemical screening.
We also work with third-party labs to certify our materials as per international standards and have put in place strong traceability and documentation systems to ensure every batch meets compliance—especially for exports.
As fire safety and environmental standards get tougher, we’re staying one step ahead with the right processes and partnerships in place.
WCI: Safety performance varies across different aspects of fire resistance. Based on your internal testing and field feedback from Indian installations, which specific aspects of fire-resistant performance remain most challenging to address consistently?
SK: Based on our in-house testing and real-world feedback from installations, there are a few areas of fire-resistant performance that continue to be the most challenging to address consistently.
One key challenge is maintaining circuit integrity during a fire—ensuring that the cable continues to function long enough to support emergency systems like alarms and lighting. Another challenge is controlling smoke and toxic fumes. It can be tough to get the right balance of low smoke, low acid release, and the right heat and oxygen resistance, especially when cables are packed closely together or used in closed spaces. We also see challenges in managing flame spread when multiple cables are bundled together, which is common in large installations like commercial buildings or metro systems.
These are complex requirements, but our ongoing R&D, material innovation, and strict testing protocols help us keep improving and delivering safer, more reliable cable solutions.
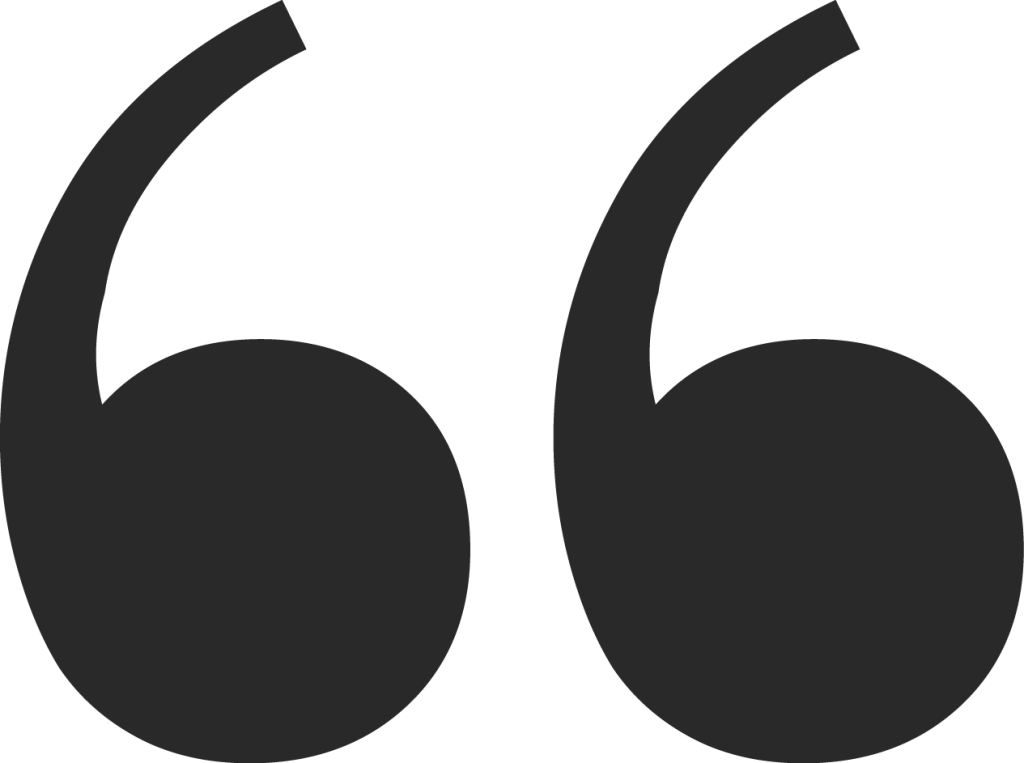
We remain open to strategic collaborations with domestic and international partners to enhance our ability to deliver safer, more efficient, and higher-performing cable solutions.
WCI: Advanced ceramic-reinforced compounds promising higher temperature ratings suited for India’s climate variations have entered the market this quarter. Looking toward next-generation fire-safe materials, which specific performance attributes would deliver the greatest value to your production capabilities and position in both domestic and export markets?
SK: The introduction of advanced ceramic-reinforced compounds with higher temperature ratings is a timely and exciting development—especially for a country like India, where cables are exposed to extreme heat, humidity, and demanding infrastructure environments. As we evaluate the next generation of fire-safe materials, certain performance attributes stand out as especially valuable for our production needs and overall market strategy.
These are enhanced thermal stability which ensures cables perform reliably even in extreme heat conditions; superior fire resistance with Low Smoke Zero Halogen (LSZH) behavior to improve safety in enclosed or high-risk areas; strong mechanical durability at elevated temperatures, which supports long-term performance and reduces maintenance; improved electrical insulation, which is key for safety and efficiency; resistance to chemicals and UV rays, making cables suitable for harsh industrial or outdoor applications; good process compatibility and scalability, so we can adapt these materials into our manufacturing lines without major disruptions; and alignment with global environmental and regulatory standards, helping us serve both domestic and export markets more effectively.
Using these new compounds will help us create advanced, high-quality cables that are well-suited for areas like urban infrastructure, transport, renewable energy, and data centers. This will improve our products’ safety and performance, and also make us more competitive in both Indian and global markets.
WCI: Industry sustainability reports indicate exploratory work in partially bio-based insulation materials (such as PLA, bio-PE, or cellulose compounds) among market leaders. Have you investigated biodegradable or bio-based insulation materials that could meet India’s fire safety requirements? What specific technical or commercial hurdles must be overcome before adoption becomes viable in the price-sensitive Indian market?
SK: We have started exploring bio-based and biodegradable insulation materials like PLA (polylactic acid), bio-PE (bio-based polyethylene), and cellulose-based compounds. These materials are promising from a sustainability point of view and align with global environmental goals.
Bringing eco-friendly materials and advanced recovery technologies into mainstream use for electrical wires and cables in India faces several key challenges such as meeting fire safety standards, ensuring processing compatibility with current manufacturing setups, scaling up the supply chain to ensure consistent availability and the lack of clear standards or certifications in this area and of course, cost competitiveness, since the Indian market is quite price-sensitive.
We are actively evaluating these materials through ongoing research and development. While they are not yet ready for large-scale deployment, we see significant potential as technology advances and market conditions become more favorable.
We remain committed to innovation and are confident that, with continued progress, these eco-friendly solutions will become viable options for mainstream adoption in the near future.
Also Read: From Codes to Compliance: India Needs Stricter Fire Safety Regulations
WCI: The proposed amendments to E-Waste Management Rules will impact several cable material streams by 2025. How are you positioning your fire-resistant cable portfolio to address both current BIS safety standards and emerging recycling mandates? Which specific recovery technologies or material innovations show the most promise for the Indian regulatory context?
SK: The upcoming changes to the E-Waste (Management) Rules will definitely impact how cable materials are made, used, and recovered. Cable manufacturers like us will need to show not just compliance with BIS safety standards, but also meet requirements around Environmental Product Declarations (EPDs), Extended Producer Responsibility (EPR), and circular economy practices.
We’re already taking steps to get ahead of these changes by repositioning our fire-resistant cable portfolio. This includes ensuring full BIS and safety compliance, designing cables with recyclability in mind, and working closely with recyclers and policymakers to build more sustainable material recovery systems. We are actively exploring advanced recovery technologies and eco-friendly materials to position ourselves at the forefront of responsible manufacturing in India. Our approach is designed not only to comply with evolving regulations but also to set new standards for environmental stewardship as the industry advances.