Bansal Wire Industries has recently inaugurated India’s largest steel wire manufacturing facility in Dadri, UP, and has launched high-performance products like steel cords, hose wires, IHT wires, OHT wires, and LRPC wires. In an interview with Wire & Cable India, Mr. Pranav Bansal, Managing Director & CEO at Bansal Wire Industries Limited reveals the company’s plan to invest INR 3,500 crore over five years in speciality steel wire production and capacity expansion. As part of this strategy, the company will establish new greenfield projects in the western and southern regions, a fully integrated manufacturing facility in western India and explore expansion into eastern India to build a robust, pan-India manufacturing and distribution footprint.
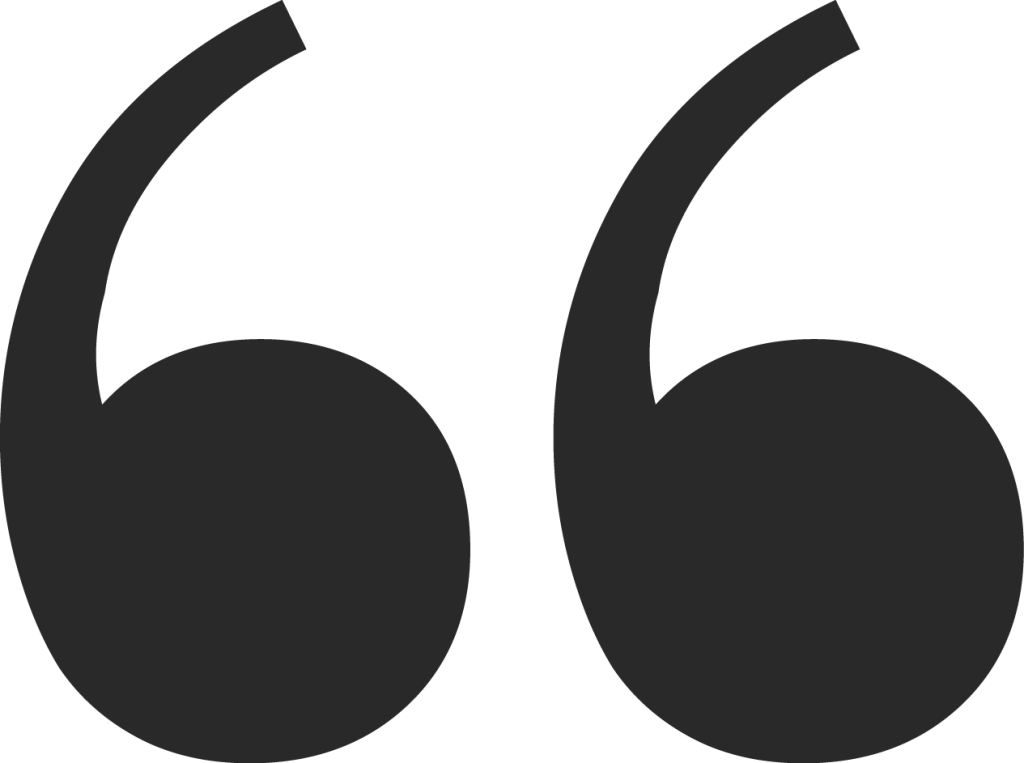
The company is launching its indigenous R&D center in Dadri, equipped with precision instruments and high-speed testing and development equipment, to boost advanced product development and process optimization.
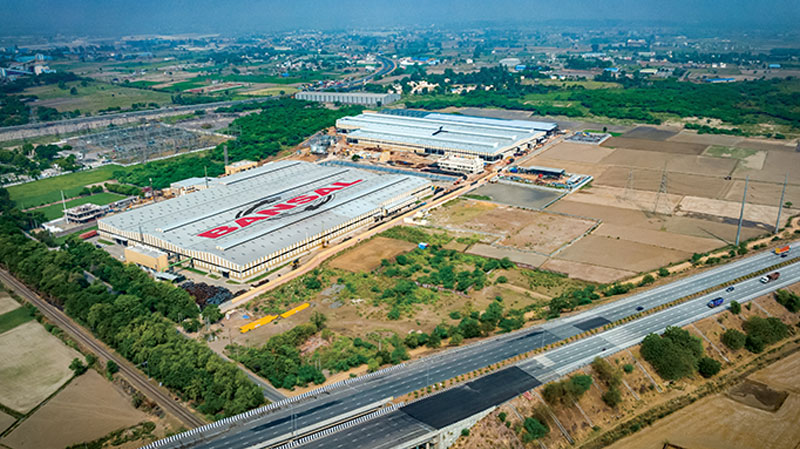
Wire & Cable India: Can you elaborate on the current trends shaping the steel wire industry in India?
Pranav Bansal: The Indian steel wire industry is undergoing significant transformation, driven by robust economic growth, evolving market needs, and proactive government initiatives. The strategic thrust under the ‘Make in India’ campaign—supported by import restrictions and higher tariffs—is offering a competitive edge to domestic manufacturers, encouraging both scale and self-reliance.
India’s focus on large-scale infrastructure development—such as highways, metro rail projects, logistics hubs, industrial corridors, and smart cities—is a major catalyst for steel wire demand. These wires are essential for reinforcement, structural applications, fencing, fasteners, and general engineering use.
The growing electric vehicle (EV) segment is further boosting the demand. Steel wires are extensively used in automotive components such as seat structures, suspension systems, and safety reinforcements. As EV adoption scales up, the need for high-performance and lightweight wire products will grow significantly.
Across industries, there is a clear shift toward high-strength, corrosion-resistant wires suited for demanding environments—such as marine, construction, and critical infrastructure—where performance and safety are non-negotiable.
Technological modernization is reshaping manufacturing practices. Adoption of smart technologies such as Artificial Intelligence (AI), robotics, and the Internet of Things (IoT) is enhancing efficiency, reducing defects, and enabling faster, more precise production with customized outputs.
Sustainability is emerging as a core industry priority. Steel wire manufacturers are taking steps to reduce carbon emissions, recycle scrap metal, eliminate hazardous processes, and use renewable energy sources. This shift aligns with global trends toward green manufacturing and responsible production.
Government schemes like the Production-Linked Incentive (PLI) for specialty steel and the National Steel Policy 2017, which aims to increase per capita steel consumption, are expected to accelerate investment, innovation, and demand in the steel wire industry.
Watch: Top Cable Companies in India
WCI: Please tell us about the impact of the Union Budget FY2025–26 on the steel wire industry?
PB: The Union Budget FY2025–26 presents a growth-conducive framework for the steel wire industry. A significant allocation toward infrastructure development is expected to directly boost demand for steel wires across core sectors such as roads, highways, bridges, ports, logistics parks, power grid modernization, and transportation networks.
Most impactful are the investments in metro systems, dedicated freight corridors, and public infrastructure, all of which require specialized steel wire products for construction and safety-critical applications.
The budget also reinforces support for the MSME sector, offering tax benefits, reduced compliance costs, and financial incentives. These measures are crucial for steel wire manufacturers, many of whom operate in this segment, ensuring smoother operations and healthy working capital cycles.
Overall, the budget is seen as a strong enabler for expansion, capacity augmentation, and domestic value addition in steel wire production.
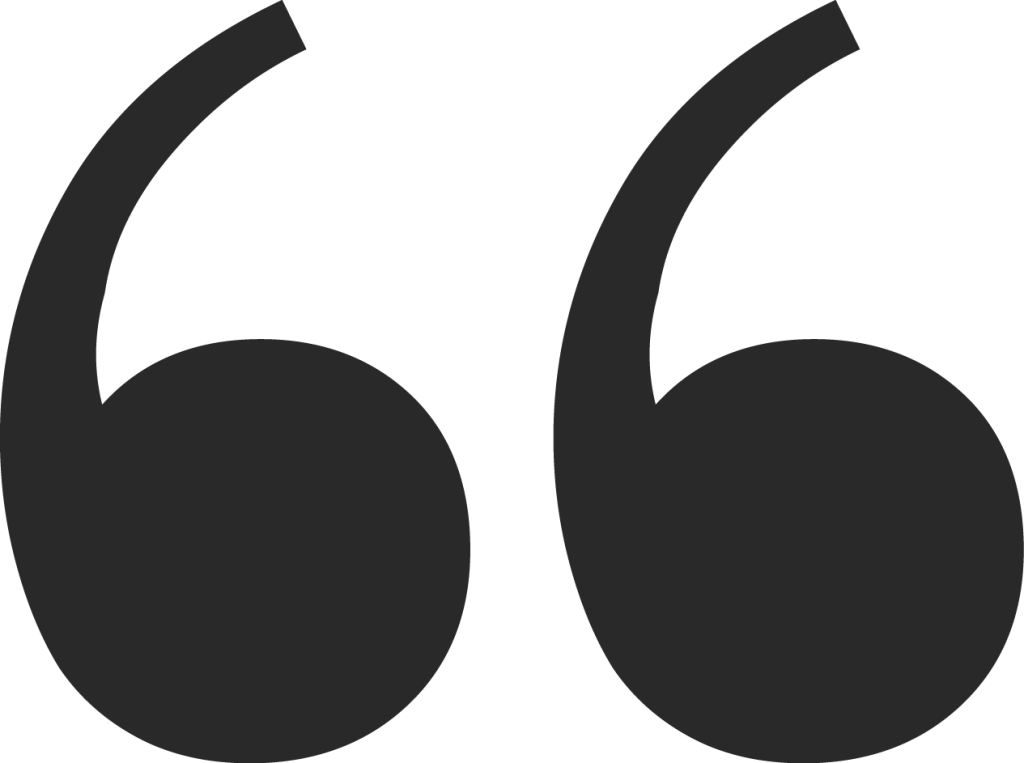
Industry 4.0 adoption through automation, real-time data tracking, and R&D investments is helping manufacturers innovate with new wire types, surface treatments, and performance-specific products.
WCI: How competitive are Indian manufacturers in the global market, and what factors contribute to or hinder their global success?
PB: Indian steel wire manufacturers are rapidly enhancing their competitiveness on a global scale by improving quality, maintaining cost leadership, and integrating advanced technologies.
There is a strong focus on quality-centric production. Manufacturers are investing in world-class testing facilities, robust quality control systems, and automation. Adherence to global standards such as ISO, ASTM, and EN is enabling Indian companies to confidently cater to international markets.
Technological upgrades are gaining momentum. Industry 4.0 adoption—through automation, real-time data tracking, and R&D investments—is helping manufacturers innovate with new wire types, surface treatments, and performance-specific products.
India’s inherent cost advantages—such as lower land cost, power costs, and manpower costs—provide a natural edge. Combined with improved efficiency and precision manufacturing, Indian firms are positioned to deliver competitive pricing without compromising quality.
The state-of-the-art equipment, like cold drawing lines, continuous casting systems, and automated coiling units, are further enhancing output, minimizing waste, and driving operational excellence.
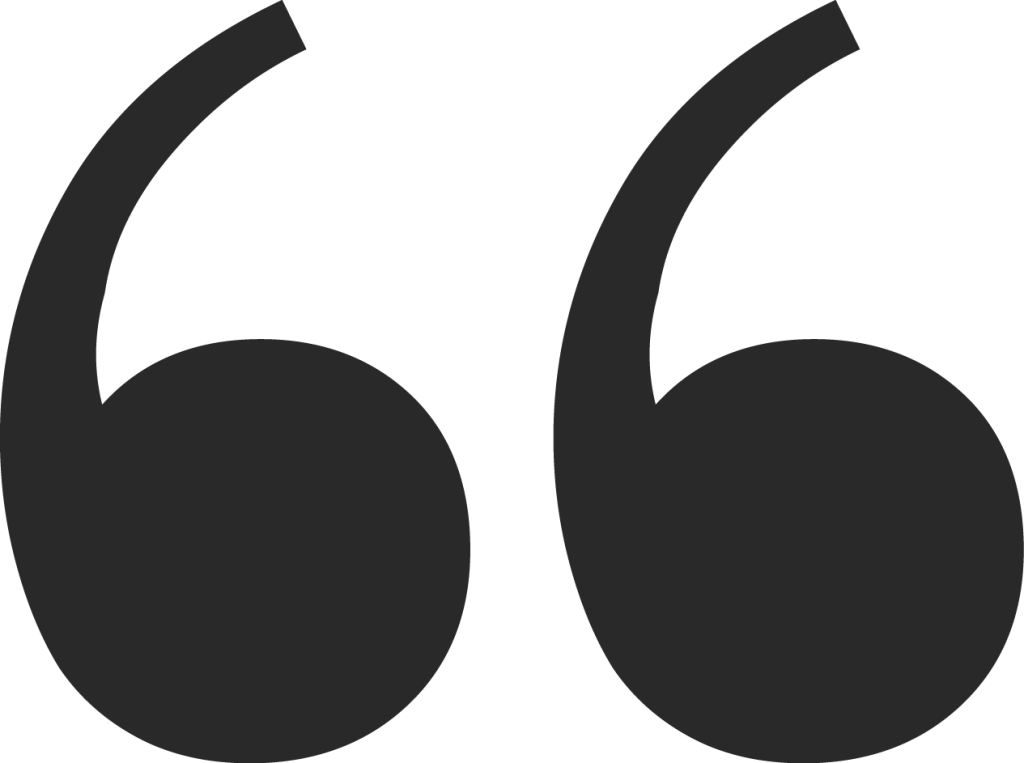
There is a clear shift toward high-strength, corrosion-resistant wires suited for demanding environments such as marine, construction, and critical infrastructure.
WCI: How do you address the raw material price volatility in the steel industry?
PB: Raw material price fluctuations—particularly in steel scrap, iron ore, and coal—pose a persistent challenge to the industry. However, Indian manufacturers are adopting a range of strategies to mitigate this risk and maintain stability.
The price volatility of raw material has long been a structural challenge for the steel industry—particularly for value-added segments like steel wire manufacturing, where cost consistency is essential for maintaining competitiveness and fulfilling long-term supply commitments.
Building resilience through supply chain intelligence: We have evolved from transactional sourcing to strategic procurement, underpinned by market intelligence and risk assessment. By actively monitoring commodity trends and geopolitical developments, we are able to anticipate supply chain shifts and make informed, proactive purchasing decisions.
Transitioning to flexible input mix: Recognizing the rigidity in raw material consumption creates risk, we are enhancing our production systems to accommodate a flexible mix of inputs—whether it be different grades of steel rods, billets, or scrap. This adaptability allows us to pivot quickly to cost-effective alternatives without disrupting quality or timelines.
Investing in domestic integration: Our upcoming steel melt shop in the western region is a deliberate step toward greater control over our input ecosystem. By producing our own billets and intermediate materials, we reduce dependency on external market fluctuations and bring critical cost centers in-house.
Enhancing efficiency at every stage: Rather than offsetting raw material costs with price hikes, we focus on manufacturing excellence. Through precision process control, energy optimization, and waste minimization, we’re extracting more value from every ton of raw input. This allows us to absorb cost pressure without passing it downstream.
Long-term partnerships over spot transactions: We prioritize building sustainable partnerships with key suppliers, which go beyond price. These relationships are based on transparency, mutual growth, and a shared commitment to supply continuity—even in volatile cycles.
By combining operational flexibility, vertical integration, and strategic foresight, Bansal Wire Industries is not just navigating raw material fluctuations—we’re future-proofing our business against them. The goal is long-term stability, not just short-term correction, and that’s what sets resilient manufacturers apart in today’s market.
WCI: What are the recent developments and innovations at Bansal Wire Industries?
PB: At Bansal Wire Industries, innovation and scale have always gone hand in hand. We have recently established India’s largest steel wire manufacturing facility in Dadri, enabling significant horizontal and vertical capacity expansion. With a current production capacity of 3.6 lakh MTPA, the facility is poised to scale up to 4.2 lakh MTPA by H1 FY26.
We are also launching a new range of high-performance products, including: steel cords, hose wires, Induction Hardened and Tempered (IHT) wires, Oil Hardened Tempered (OHT) wires, and Low Relaxation Prestressed Concrete (LRPC) wires.
Sustainability remains a core focus. We have implemented IoT-based digital systems for real-time production data and paperless operations. We have also undertaken rainwater harvesting, and have solar energy systems, and acid-free wire rod cleaning for eco-friendly manufacturing. Moreover, we have ETP units with zero liquid discharge and green-certified machinery for environmental compliance.
Workforce development is another priority. We foster a strong organizational culture with open communication, employee engagement, recognition programs, and a focus on safety and well-being.
To support future innovation, we are launching our own indigenous R&D center in Dadri, equipped with precision instruments and high-speed testing and development equipment, to boost advanced product development and process optimization.
Also Read: Miki Wire Works: Weaving Innovation and Growth into India’s Steel Wire Industry
WCI: Please give an overview of your market footprint, key projects, and clientele?
PB: With over 85 years of legacy in the steel wire business, Bansal Wire Industries has built lasting relationships based on trust, quality, and performance. Our growth has always been customer-driven, and increasing demand from our clients led to the conceptualization and commissioning of our large-scale Dadri Unit.
We cater to a diverse array of industries, including: automotive, power and transmission, agriculture, general engineering, construction, and hardware and fasteners. Our solutions are tailored to a wide range of end-use applications, ensuring consistency, reliability, and innovation across all market segments.
WCI: What are the future growth plans and investments?
PB: Looking ahead, we have planned a total outlay of INR 3500 crore for the next 5 years for investments in speciality steel wire production and regular capacity expansion across India. This includes setting up new greenfield projects and facilities in the western and southern regions of the country.
We are developing a fully integrated manufacturing facility in western India, complete with a steel melt shop, to serve high-growth markets with faster delivery, improved logistics, and lower transportation costs. This plant will also help us efficiently cater to southern India.
Additionally, we are exploring expansion into eastern India, as part of our long-term strategy to build a robust, pan-India manufacturing and distribution footprint.