Cabcon India Limited has recently introduced HTLS conductors in its portfolio to meet the evolving demands of efficient power transmission. Targeting a 20-25 percent increase in its production output in the next few years, the company plans to explore emerging opportunities both in India and high-growth international regions like Africa and the Middle East. This was shared by Mr. Madan Fomra, Managing Director, Cabcon India Limited, during an exclusive interaction with Wire & Cable India.
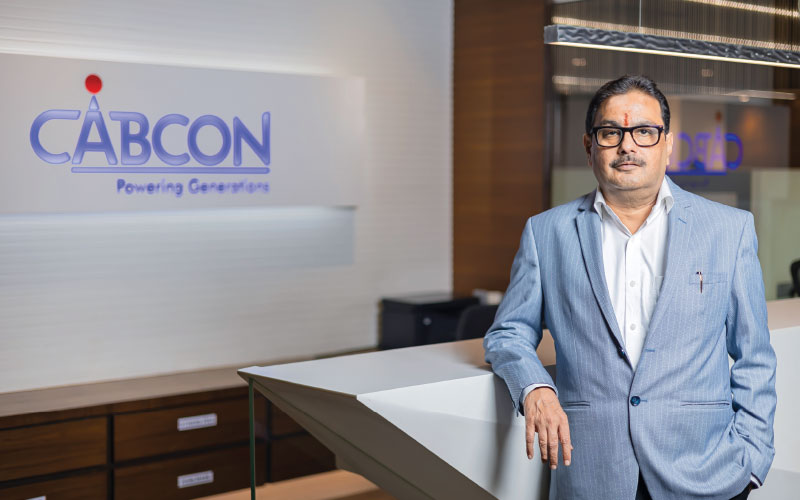
Wire & Cable India: What types of EHV cables and/or conductors do you manufacture for power transmission and distribution systems? How do they differ in terms of properties and performance?
Madan Fomra: We manufacture a comprehensive range of conductors and cables for power transmission and distribution, including all types of aluminium & alloy conductors and LT/HT power, control & AB cables. Apart from that, we have newly-added HTLS conductors to our manufacturing range. Each type is engineered to serve specific transmission needs while ensuring reliable performance and durability across varied environments. ACSR conductors remain a popular choice due to their high tensile strength and cost-effectiveness, particularly for long distance overhead lines. For areas exposed to corrosive conditions, AAAC conductors offer better corrosion resistance and a favourable conductivity to weight ratio, making them a reliable alternative.
Our latest addition, HTLS conductors, represent a significant step forward in transmission efficiency. These are designed to carry higher current loads while minimizing sag, even under elevated operating temperatures. This makes them ideal for grid upgrades and capacity enhancement projects where existing infrastructure constraints limit the feasibility of new tower installations. By allowing more power to be transmitted through existing corridors, HTLS conductors support faster execution timelines and better return on investment for utilities and EPC players.
Watch: Top Cable Companies in India
WCI: What recent innovations or advancements have developed in your technology for enhanced efficiencies in power transmission? Have you incorporated these into your products, and how do they improve performance or reduce costs?
MF: In recent years, one of the most significant advancements in our industry has been the development and integration of High Temperature Low Sag (HTLS) conductors. At our company, we have proactively adopted HTLS technology into our product portfolio to meet the evolving demands of efficient power transmission. HTLS conductors offer several compelling advantages over conventional ACSR conductors. They are designed to operate at higher temperatures of up to 210 degree celsius without significant sag, thereby allowing utilities to increase the ampacity of existing transmission lines by up to 1.5 to 2 times without the need for additional infrastructure. This directly contributes to reduced capital expenditure for utilities and enhanced transmission capacity. We are also integrating composite core materials to further improve performance and longevity in harsh environmental conditions. Additionally, the lightweight nature and higher strength to weight ratio of these conductors help minimize structural stress on towers, translating to lower maintenance and replacement costs.
WCI: What quality control processes are in place to ensure the EHV cables and/or conductors meet industry standards and meet reliability and safety benchmarks for various environmental conditions?
MF: Quality and reliability are at the core of our manufacturing philosophy, especially when it comes to Extra High Voltage (EHV) cables and conductors, which are critical to power infrastructure. To ensure our products meet the industry standards, we have implemented a rigorous quality control framework across our production and testing processes. All our incoming raw materials undergo stringent inspection and each stage of manufacturing is monitored through process checks using calibrated instruments and automated systems. Our testing protocols cover a wide range of parameters, including electrical and mechanical performance.
These tests are conducted as per relevant IS standards. Importantly, we are in the process of getting our in-house testing laboratory NABL accredited, which will solidify our commitment towards best testing practices and will add a layer of credibility and trust, particularly for government and utility clients. In addition to routine factory acceptance tests, we conduct type tests from time to time to validate our product performance under diverse environmental conditions. Through this robust quality assurance system, we ensure that our EHV cables and conductors consistently meet the highest reliability and safety benchmarks, regardless of the deployment environment.
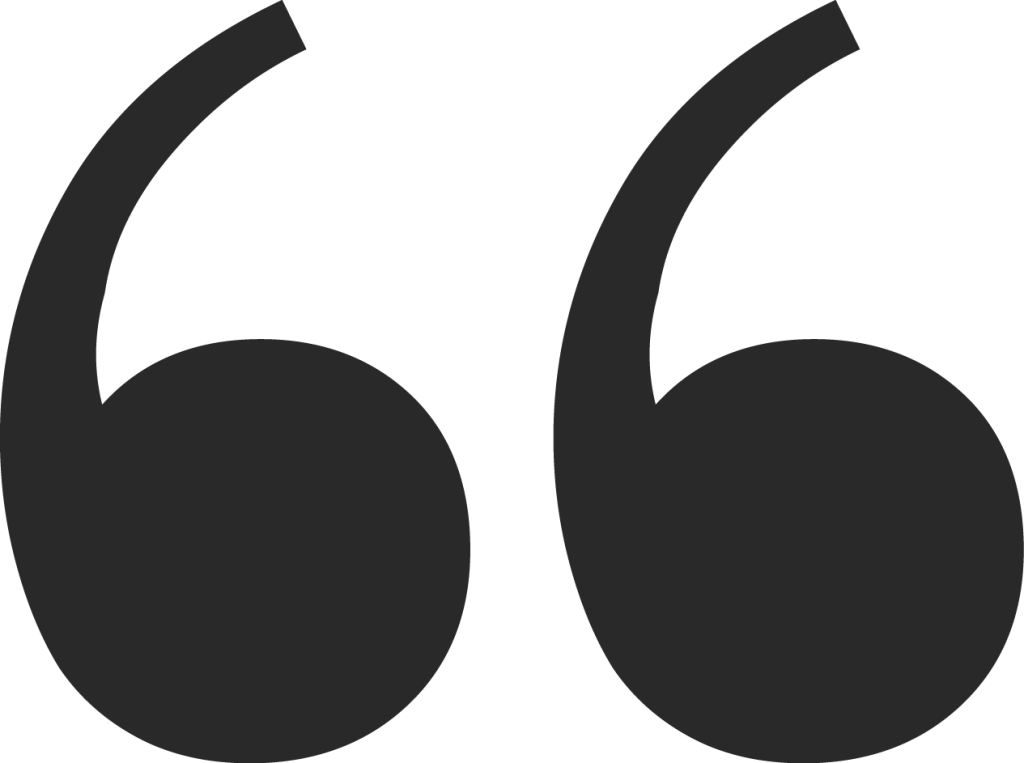
Currently, we have an installed annual production capacity of approximately 150,000 km for aluminium conductors up to 33 kV; 50,000 km for cables and 33,000 km specifically for EHV conductors.
WCI: What is the typical lifespan of your EHV cables and/or conductors? What value-added services, such as engineering support, installation guidelines and maintenance, do you provide to customers in the field?
MF: Usually, EHV cables and conductors are designed for a long operational life, typically ranging between 30 to 40 years, depending on environmental and load conditions. We manufacture our products using high purity raw materials and advanced insulation technologies, ensuring optimal electrical performance, thermal stability and mechanical strength over decades of service. As a company with an established presence in the power sector, we are actively engaged in turnkey EPC (Engineering, Procurement, and Construction) projects, which enables us to offer a comprehensive, solution-oriented approach. This includes not only the supply of high-quality EHV conductors, but also value added services that support project execution from start to finish.
WCI: What is your total production capacity and what target are you eyeing? To what markets do you majorly cater?
MF: Our manufacturing capabilities are designed to support large scale infrastructure demands, with a focus on quality, consistency and timely delivery. Currently, we have an installed annual production capacity of approximately 150,000 km for aluminium conductors up to 33 kV; 50,000 km for cables and 33,000 km specifically for EHV conductors. These capacities are supported by state-of-the-art machinery, robust quality systems, and a skilled workforce committed to meeting stringent delivery timelines.
Looking ahead, we are targeting a 20–25 percent increase in our production output over the next few years. This is part of our strategic expansion plan aimed at capitalizing on emerging opportunities in transmission infrastructure upgrades, renewable energy integration, and urban power distribution networks.
At present, our major market is the domestic sector, where our products are widely used by Central and state utilities, EPC contractors and infrastructure developers. We have a strong track record of supplying to government-backed schemes, such as rural electrification, smart grid development and renewable energy evacuation. In addition to our domestic focus, we are also actively working towards expanding our international footprint, particularly in high-growth regions like Africa and the Middle East. These markets present a significant opportunity for quality-driven manufacturers like us and we are aligning our operations, certifications and export logistics to effectively serve their infrastructure development needs.
Also Read: GEMSCAB Targets 50% Capacity Boost With Third Manufacturing Unit in Rajasthan
WCI: Please walk us through your unique manufacturing setup. What new technologies have you invested in to cater to the demanding market?
MF: Our manufacturing setup has been thoughtfully developed to address the quality, scale and speed required by today’s power infrastructure projects. Located strategically near the Kolkata port, our facility offers logistical advantages for both domestic distribution and international exports, significantly reducing lead times and improving supply chain efficiency. The plant itself is vertically integrated and equipped with advanced manufacturing and testing infrastructure, covering the entire production chain, from wire drawing and stranding to insulation, sheathing, and high voltage testing.
This allows us to maintain tight control over quality while offering a flexible production schedule to meet diverse project timelines and real-time process monitoring systems that are deployed across critical stages to track parameters and ensure product consistency. To keep pace with the evolving market, we are also integrating ERP systems and lean manufacturing practices, enhancing traceability, operational efficiency, and responsiveness. As part of our commitment to quality, we are in the process of getting our in-house laboratory NABL accredited, which will further strengthen our testing credibility and align us with the highest industry standards. With this robust, future ready manufacturing ecosystem, we are fully prepared to serve both the domestic market and emerging export regions, notably Africa and the Middle East by delivering reliable, high-performance conductor and cable solutions.
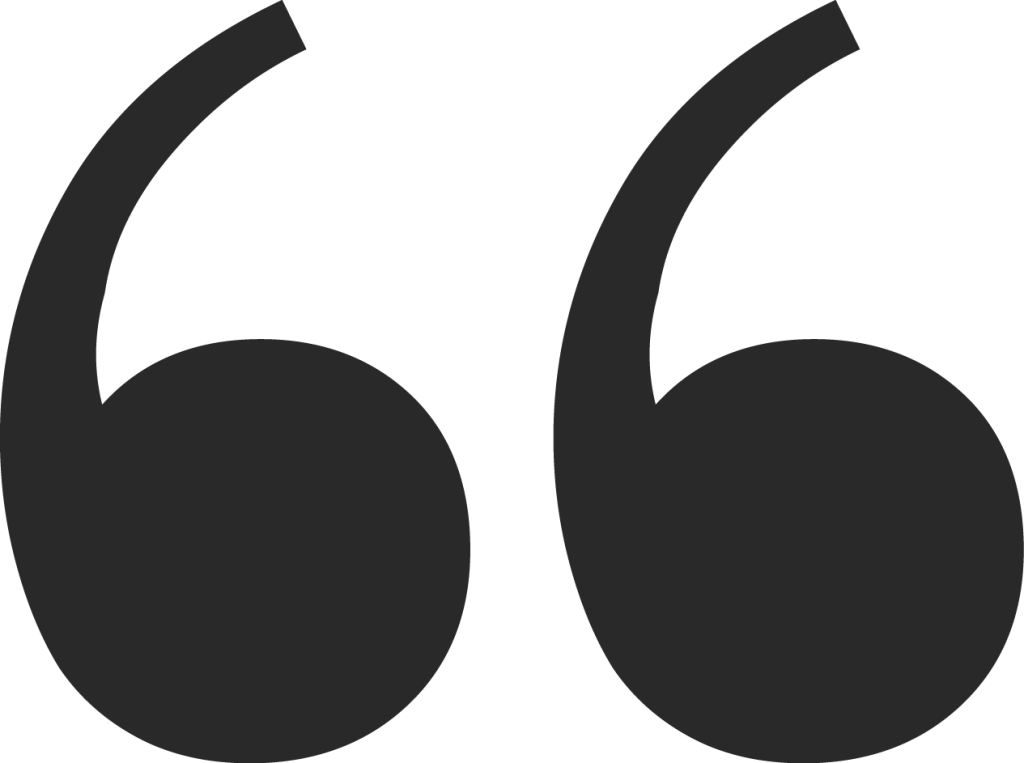
Quality and reliability are at the core of our manufacturing philosophy, especially when it comes to Extra High Voltage (EHV) cables and conductors, which are critical to power infrastructure.
WCI: What are some of the major challenges you are experiencing in the market?
MF: One of the major challenges we are currently experiencing in the market is the volatility in raw material prices, particularly aluminium and copper, which are critical inputs for conductor and cable manufacturing. This price instability has been further aggravated by global tariff war and trade disruptions started by the US, leading to delay in procurement planning and cost forecasting. Such fluctuations directly impact project budgeting and execution timelines especially in public sector projects where pricing structures are fixed for longer durations. Despite these external pressures, we have put measures in place such as strategic sourcing, buffer inventory planning, and long term supplier partnerships to ensure minimal disruption to our clients.
WCI: Where do you see the market headed in the next 5 years, in terms of growth, innovations, technology integration, and new challenges? How do you see yourself in that landscape?
MF: Over the next five years, the power transmission and distribution market is poised for a significant transformation, driven by a combination of infrastructure growth, clean energy integration, and policy-level commitment toward sustainability. With India pledging to become net carbon neutral by 2070, the country is expected to witness massive investments in renewable energy, grid modernization, and efficient transmission technologies. This will directly accelerate the demand for high-performance conductors and EHV cables that can support higher loads, lower losses, and smart grid capabilities. Innovation will play a pivotal role in this shift, with increased adoption of HTLS conductors, real-time monitoring systems, and intelligent cable designs that cater to both conventional and renewable energy corridors.
Technology integration, especially in terms of digital asset management, condition-based monitoring and automation, will become essential in ensuring system resilience and reliability. We see ourselves strongly aligned with this evolving landscape. Our company is investing not only in scaling up production capacity, but also in developing future ready products and enhancing our efforts to meet the technical demands of upcoming projects. Furthermore, our involvement in turnkey EPC projects positions us to contribute holistically, from manufacturing to execution, towards India’s vision of a greener, more connected energy future.