Ddev Group, a supplier of insulation compounds to the cable industry continues to provide advanced solutions to the modern infrastructure requirements of the country. To provide safe power distribution, its specially designed Water Tree Retardant (WTR) XLPE compound makes insulation material sturdy in humid environments, like in Mumbai. With the development of low-toxicity LSZH compounds with improved mechanical integrity, the company has further strengthened its compound portfolio. There’s a strong focus on certification, sustainability through recyclable blends, and collaborative efforts with manufacturers. In an exclusive conversation with Wire & Cable India, Mr. Rajesh Kothari, Director of Ddev Group, shares insights about the current demands, and points out the need for material science innovation– materials offering higher thermal endurance with easier processing.
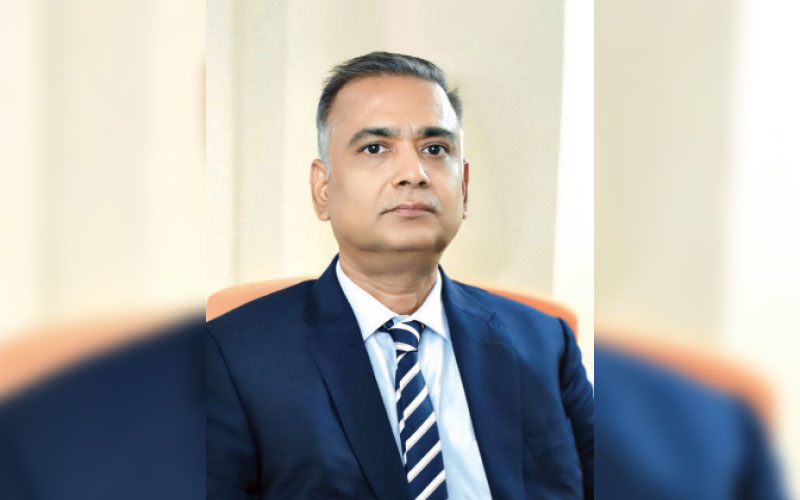
Wire & Cable India: As infrastructure projects and smart cities expand with stricter safety protocols, which of your current compounds are specifically engineered to meet cable manufacturers’ enhanced performance requirements, and what cable types or sectors are they most suited for?
Rajesh Kothari: We have always worked to provide safe products to the cable industry. We being the leading insulation compound supplier gave solutions to industry to meet the latest and advanced needs of the users. It would be worth mentioning about one of our products which is designed to provide a safe power distribution network– WTR XLPE insulation. It is a specially designed compound to make insulation material more sturdy against development of electrical trees in humid conditions, that is why it is called Water Tree Retardant (WTR) XLPE. It is the most preferred product for cities like Mumbai.
WCI: What breakthroughs have you made to help cable manufacturers in reducing smoke density and toxicity without compromising mechanical integrity in LSZH compounds?
RK: LSZH or HFFR compounds are designed to reduce smoke density and toxicity. However, the product design is such that reduced toxicity is achieved at the cost of mechanical properties. With the efforts of our R&D team we have been able to work with the latest additives and base resins to achieve very low toxicity with very good mechanical performance.
Watch: Top Cable Companies in India
WCI: Are your compounds developed and certified in direct response to cable manufacturers’ compliance needs. How do you support them in regional compliance efforts?
RK: It has been a hallmark of Ddev Group. We have always focused not only on developing compounds for emerging needs of industry but also to achieve certification so that our customers are well enabled to compete at the global stage.
We have certification of LV XLPE for aerial bunched cables from the French Laboratory, and certification of MV XLPE with semicon and jackets together from KEMA. Our LV XLPE is suitable for UL 44 , UL 4703 for the USA market, certified by Underwriters Laboratory USA.
We have VDE certification for WTR XLPE with long term wet ageing tests, signifying our product’s adherence to European Union safety and quality standards in the electrical and electronic industries.
WCI: Can you share a recent example where you developed or customized a compound for a cable manufacturer’s specific project or tender requirement?
RK: Collaboration is a critical tool for survival as well as growth. We have a long history of collaborative efforts with our customers as well as suppliers. The very recent example is development of a 3.3 KV compound for one of our customer to tender requirements of NTPC. We had collaborated with one of our customers and enabled them to meet the tender requirement and at the same time got our product listed as an approved product by NTPC.
WCI: Are you working with advanced technologies or synergistic blends that go beyond traditional compounds, specifically to enhance performance in cables?
RK: We are constantly working with our suppliers and are working on many such developments. Some of such projects are already bearing fruit in case of LSZH grades where we have used such blends as carriers. We are also working on many projects to take full advantage of advancements in material science.
WCI: How are you addressing environmental concerns in compounds—whether through halogen-free formulations, recyclable blends, or bio-based additives?
RK: We as a group of companies are very much aligned to the sustainability aspects. We are working on recipes where the recycles can be used. Currently the scope is limited due to stringent performance needs and the prevailing specifications. We are aligning ourselves with work being done to modify specifications to enable introduction of recyclable products to help circularity.
Also Read: Shakun Polymers’ ECOTEK Series Delivers High‑Performance Fire‑Safe Compounds
WCI: From a compounder’s perspective, what’s the next big leap needed in material science to meet the cable industry’s evolving needs?
RK: We need materials which can achieve higher thermal endurance with much simpler processes. We also would list out nano materials development and availability to improve mechanical performance of compounds without too much of loading.
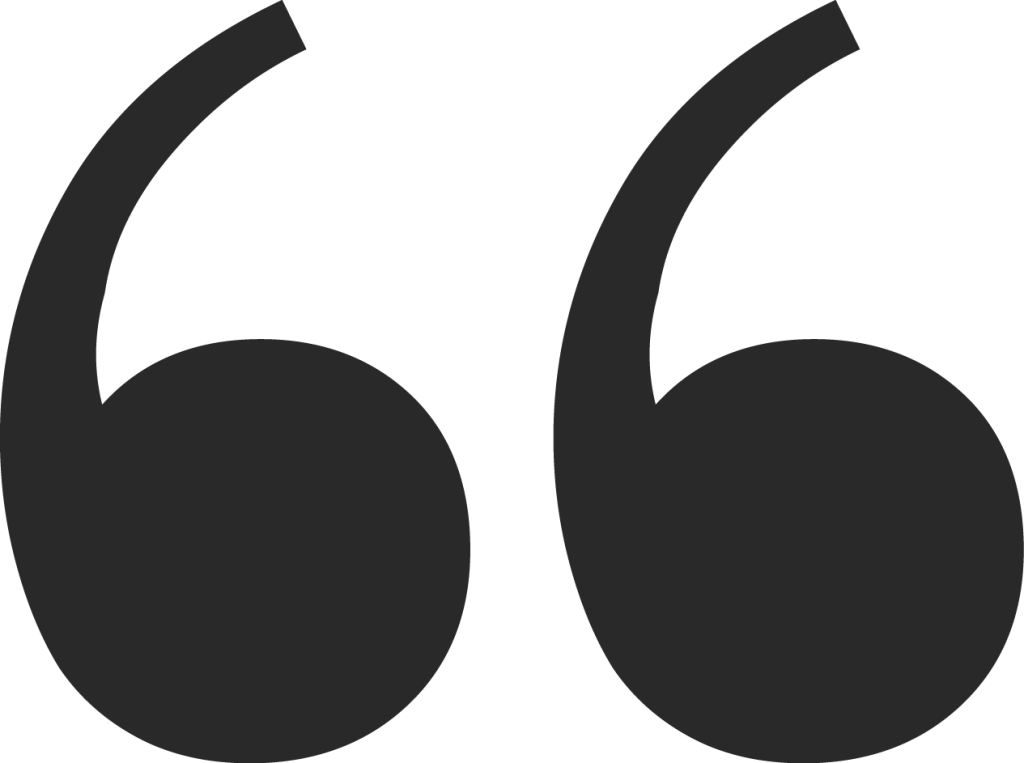
We have always focused not only on developing compounds for emerging needs of industry but also to achieve certification so that our customers are well enabled to compete at the global stage.