Indian steel wire industry is experiencing rapid growth as manufacturers adopt sophisticated technology and expand production capacity. This strategic transformation reflects shifting market dynamics as producers position themselves for expansion while navigating evolving customer expectations and financial imperatives.
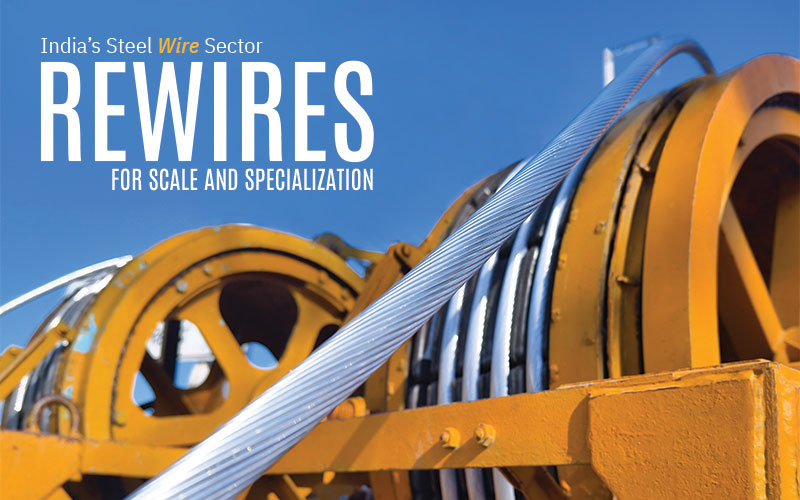
As India’s manufacturing backbone strengthens, the role of steel wire becomes increasingly pivotal. Steel wires serve as essential inputs for infrastructure projects, automotive components, construction applications, and precision engineering. The versatility of these products continues to expand as manufacturers develop specialized variants for emerging applications, positioning the sector for sustained growth alongside India’s industrial expansion.
Production reached 5.6 million tonnes in FY2023, with analysts projecting volumes to potentially reach 8-9 million tonnes by FY2028 as manufacturers capitalize on infrastructure investments and automotive sector expansion. Another market analysis values the steel wire market at approximately USD 10 billion, poised to expand to USD 14 billion by FY2031 at a 5.1% CAGR. This growth trajectory is fundamentally reshaping market dynamics.
Industry Evolution: The Rise of Organized Players
Numerous small and medium enterprises once operated independently, facing perennial efficiency challenges and quality inconsistencies due to the lack of economies of scale. Major producers, including Global Wire India (GWI—Tata Steel’s downstream division with brand name Tata Wiron), Viraj Profiles, Bansal Wire Industries Limited (BWIL), and Bharat Wire Ropes, faced competition from hundreds of regional manufacturers. This competition obstructed efforts to establish consistent quality benchmarks and limited capital available for technological upgrades.
However, the industry’s structure is evolving as operations increasingly organize to meet growing demand efficiently. The small and medium enterprises that once dominated India’s steel wire sector are steadily losing market share to organized producers with larger manufacturing capacities.
Production capacities across major steel wire manufacturers illustrate the scale and investment in the sector. Viraj Profiles operates at 528,000 TPA capacity, while BWIL has expanded its manufacturing capacity from 240,000 TPA to 600,000 TPA, with a significant investment of INR 550–600 crore in a new facility.
This new facility at Dadri, Uttar Pradesh, currently operates at 360,000 TPA and is poised to scale up to 420,000 TPA by the first half of FY26. This is probably the largest single-site manufacturing unit for finished steel wire products in India.
Tata Steel’s GWI operates around 550,000 TPA, with Group Nirmal contributing 200,000 TPA to the finished steel wire segment. HD Wires, Systematic Group, and Bedmutha Industries each maintain capacities of approximately 120,000 TPA, while Rajratan Global’s Indian facilities produce 102,000 TPA and Bajrang Group operates at 60,000 TPA.
While primarily upstream players, Jindal Steel & Power Limited (JSPL) and Jindal Stainless supply critical wire rod inputs that downstream manufacturers draw into specialized steel wire products for diverse industrial applications.
JSPL operates 600,000 TPA facilities primarily producing carbon and alloy steel wire rods, which serve as key raw materials for manufacturers of industrial wires, fasteners, springs, and construction-grade wire products.
Usha Martin leverages manufacturing facilities across multiple locations, while Jindal Stainless focuses on premium-grade stainless steel wire rod production. These capacity figures reflect the industry’s evolving structure as manufacturers respond to increasing domestic demand and export opportunities.
“The industry is moving towards value-engineered products that balance cost, performance, and longevity,” observes Mr. Sidharth Agrawal, Managing Director of Systematic Group, highlighting a fundamental shift from commodity production to highly engineered solutions.
As companies adapt to these shifting market realities, technology investments and quality enhancements have emerged as critical drivers for sustainable growth.
Watch: Top Cable Companies in India
Catalysts of Growth: Technology, Scale, Policy, and Quality
High-value segments including automotive and construction increasingly demand standardized products meeting strict technical specifications. This quality imperative drives producers toward technology investments that enhance production capabilities.
“We continue to upgrade and adopt automation and real-time monitoring systems to enhance quality control and minimize defects in our end product,” explains Mr. Mahesh Poddar, Chairman of Miki Wire Works.
Well-capitalized manufacturers gain competitive advantages through technological upgrades that improve efficiency and product quality. BWIL’s expansion rides on substantial investments at its Dadri plant in automation and smart manufacturing systems that reduce production variances to meet international quality benchmarks.
Rajratan Global has implemented state-of-the-art heat treatment systems for producing high-carbon steel wires, allowing for specialized metallurgical properties crucial for automotive safety components. For premium-grade alloy and carbon steel wire rods, JSPL invests heavily in advanced production technologies, focusing on precision drawing equipment that maintains tighter tolerances than industry averages.
Vividh Wires Director Mr. Ashwani Gupta emphasizes this technology-driven growth: “By combining our operational excellence and our relentless focus on quality with world-class technology, we are confident that we have the ability to stand shoulder-to-shoulder with the best manufacturers of the world.”
Raw material price volatility and technological investment requirements have intensified financial considerations for producers. Key input prices for iron ore, coking coal, and steel scrap fluctuate sharply, as global geopolitical tensions and supply chain disruptions disrupt markets. This volatility has particularly pressured smaller firms, while larger players better absorb cost swings through stronger procurement strategies.
Larger manufacturers leverage economies of scale in procurement, production, and distribution, reducing per-unit costs while increasing pricing flexibility. BWIL and Bharat Wire Ropes have significantly expanded market share through scale-driven efficiencies and product line expansions.
The implementation of Quality Control Orders (QCOs) has established clearer manufacturing standards, requiring significant capital investments for compliance. Many producers now face choices between substantial modernization investments or market repositioning as regulatory requirements evolve. Recently, Kataria Industries strengthened its specialty wire position through strategic acquisition of Ratlam Wires’ wire manufacturing business.
Capital allocation remains particularly important for producers facing rising operational costs and compliance requirements. Strategic partnerships, joint ventures, and acquisitions represent increasingly common growth strategies as the industry evolves.
Government infrastructure initiatives have generated increasing demand for standardized wire products meeting precise specifications. Producers with advanced testing capabilities and robust quality systems have gained market advantage, accelerating the shift toward organized production.
These foundational shifts in technology, scale, policy and quality set the stage for industry leaders to execute strategic growth initiatives.
Winning Moves: How Industry Leaders are Expanding Their Edge
Leading domestic producers, including BWIL, Group Nirmal, Rajratan Global Wire, Usha Martin, Bedmutha Industries, Viraj Profiles, and Tata Steel’s GWI, are driving growth through technological collaborations, capacity expansions, and export diversification.
Tata Steel’s acquisition and expansion of operations in Thailand transformed its wire business into a global enterprise (Global Wires Business—GWB), enabling the company to serve Southeast Asian markets with a strong manufacturing base and extend the reach of its specialized wire products beyond India.
Today, Tata Steel’s GWB, including GWI and Thailand’s operations, is the largest finished steel wire producer from India. GWI’s 550,000 TPA operation includes dedicated production lines for infrastructure-grade wires that meet specialized tensile strength requirements for bridge construction and seismic reinforcement applications.
Usha Martin has strategically strengthened its global position through technical collaborations with European wire rope specialists. Its global manufacturing footprint includes specialized facilities dedicated to mining-grade wire ropes and aviation cables that command premium prices in international markets.
Viraj Profiles, with an integrated manufacturing capacity of 528,000 TPA, allocates a significant portion to stainless steel wire production, offering corrosion-resistant variants tailored for marine and other demanding applications. Jindal Stainless has carved a niche in high-performance stainless steel wire rods, which downstream wire producers process further for precision applications, including instrumentation and medical devices.
Systematic Group has converted its 120,000 tons annual capacity toward higher-margin specialized fastener wire, abandoning commodity segments entirely during its recent modernization.
Specialty wire production represents a strategic focus for manufacturers seeking higher margins. Companies increasingly target specialized applications in automotive, infrastructure, and engineering sectors where performance requirements drive innovation.
Rajratan Global Wire has positioned itself as a key supplier of bead wire for Thailand’s tire manufacturers. Notably, Rajratan is the only manufacturer of bead wire in Thailand, positioning itself to meet the specific requirements of tyre manufacturers in Southeast Asia.
Foreign investment is also a key strategy for scaling operations and enhancing the industry’s growth trajectory. Belgium-based Bekaert expanded Indian operations through its partnership with Mukand Ltd in 2007. Although Mukand Ltd. concluded its wire manufacturing collaboration with Bekaert through a 2014 stake sale and now concentrates largely on stainless steel long products, the company’s earlier specialty wire ventures yielded valuable insights into sustainability practices and materials innovation.
Digital manufacturing investments have become essential for maintaining competitiveness. GWI’s implementation of IoT-enabled monitoring systems has reduced production disruptions while reducing defect rates by a significant 18% and improving dimensional consistency across high-tensile wire product lines.
“With the adoption of Industry 4.0 technologies like IoT and AI, the steel wire industry in India is evolving, enabling smart factories and improving its efficiency,” notes Miki Wire Works Chairman Mahesh Poddar. Similar digital initiatives at Usha Martin have integrated automated heat treatment and advanced surface finishing technologies, ensuring consistency in wire ropes for mining and construction applications.
Policy Push: Incentivizing Innovation and Sustainability
The Production-Linked Incentive (PLI) Scheme for Specialty Steel has accelerated industry transformation by incentivizing high-value production. The program encourages large-scale manufacturing investments while reducing import dependence for specialized wire products. The Steel Import Monitoring System (SIMS) provides additional protection against sudden import surges.
The government through such policies and regulatory framework encourages manufacturers to adopt more sustainable processes alongside quality improvements. “The budget’s emphasis on sustainable manufacturing, with INR 150 billion incentive for low-carbon steel production, also encourages the adoption of greener technologies in wire manufacturing,” notes Miki Wire Works Chairman Mr. Mahesh Poddar.
Tariff rationalization remains a constant industry demand to balance domestic production support with manufacturing competitiveness. The Steel Wire Manufacturers Association has been advocating for higher duties on finished wire products while seeking reduced tariffs on essential raw materials including high-carbon wire rods.
Mr. Ashwani Gupta, Director of Vividh Wires, emphasizes the urgency for government action on appropriate safeguard duties: “Without such proactive policy measures, Indian manufacturers may face an uneven playing field that will threaten the long-term competitiveness of the steel sector.”
The government’s recent reduction of tariffs on flat-rolled stainless steel from 22.5% to 15% demonstrates policy responsiveness. This move reflects the government’s commitment to improving cost efficiencies for downstream industries while still ensuring strategic trade protections and strengthening competitiveness against imports from China and Southeast Asia.
While policy support creates important growth pathways, significant challenges remain for manufacturers navigating this transition.
Also Read: Bansal Wire Industries to Invest INR 3,500 Crore for Pan-India Expansion Drive
Hurdles Ahead: Modernization, Margins, and Manpower
Growth presents challenges as producers adapt to stricter quality standards and automation requirements. Many enterprises operate with equipment requiring upgrades and limited technical resources. This limitation creates compliance challenges as standards evolve. Capital constraints affect modernization options, particularly for manufacturers without access to institutional financing.
Persistent input cost volatility creates significant planning challenges, especially for higher-value segment producers. To counteract this, producers are devising favorable material sourcing strategies and investing in process innovations to stabilize margins and maintain competitiveness. Mukand Limited CEO Mr. Neeraj Kant describes how sustainability initiatives address both environmental and cost concerns: “Adaptation will hinge on collaboration and innovation. We’re seeing a shift toward greater use of recycled stainless steel, which not only reduces dependency on volatile raw material markets but also aligns with global decarbonization goals.”
Technical workforce shortages have emerged as manufacturing processes become more sophisticated. Companies increasingly struggle to recruit workers skilled in advanced manufacturing technologies, automation systems, and digital production tools. Addressing these shortages requires coordinated industry initiatives combining specialized training programs with equipment investments.
On the Horizon: Global Ambitions, Greener Goals
Growth appears poised to accelerate as leading manufacturers strengthen market positions through strategic expansions. Small and medium enterprises face both opportunities and challenges to modernize operations or consider strategic partnerships. Rising quality standards and competitive dynamics create transformation imperatives for producers developing scale economies or specialized capabilities.
Strategic partnerships will continue reshaping the competitive landscape, with companies like BWIL and Usha Martin expanding scale while increasing operational efficiency. Digital manufacturing technologies will drive production improvements while enhancing quality consistency.
Export opportunities represent significant growth avenues for manufacturers investing in quality systems and technical capabilities. “Indian manufacturers have aligned their production processes with international quality standards like ASTM, DIN, and ISO, enabling broader acceptance in global markets,” explains Mukand Limited CEO Mr. Neeraj Kant, whose company exports specialty wire products to about 50 countries.
This quality-driven approach has become essential for companies with global ambitions. Vividh Wires Director Mr. Ashwani Gupta encapsulates this mindset: “Our vision is clear: To produce wires that are at least at par with global standards, if not exceeding them,” reflecting a commitment that has helped secure export contracts across Europe and North America.
Sustainability initiatives increasingly influence manufacturing strategies as environmental considerations gain prominence. “We strongly believe in protecting the environment during manufacturing and are continuously working to make our processes greener. This involves optimizing energy consumption, reducing waste, and investing in sustainable production techniques,” elaborates Miki Wire Works Chairman Mr. Mahesh Poddar.
The BWIL facility at Dadri features solar power generation, rainwater harvesting, energy-efficient machinery, and an acid-free wire cleaning process. An on-site Effluent Treatment Plant (ETP) and extensive landscaping reinforce its green footprint.
Renewable energy investments address both sustainability objectives and long-term energy costs. “We partnered with Tata Power Renewable Energy Limited to establish a 43.75 MW captive solar project in Jamkhed, Maharashtra that is expected to generate nearly 100 million units of clean energy annually and is expected to offset 54,687 tonne CO₂ emissions per year,” reveals Mukand Limited’s Mr. Neeraj Kant.
Industry transformation will require coordinated approaches to innovation, strategic partnerships, and policy support. Companies successfully adapting to these changing market dynamics will likely emerge as leaders in an increasingly competitive global marketplace where scale, technology, and sustainability represent critical success factors.
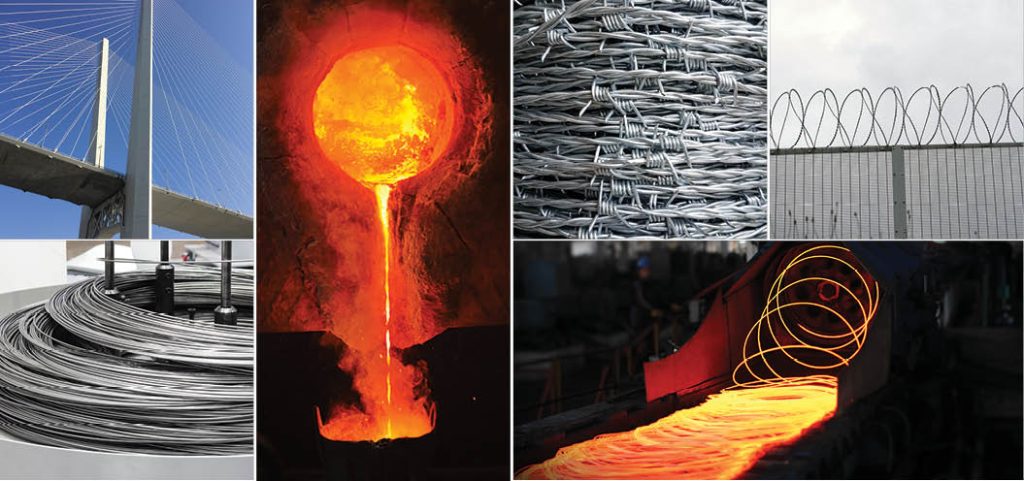