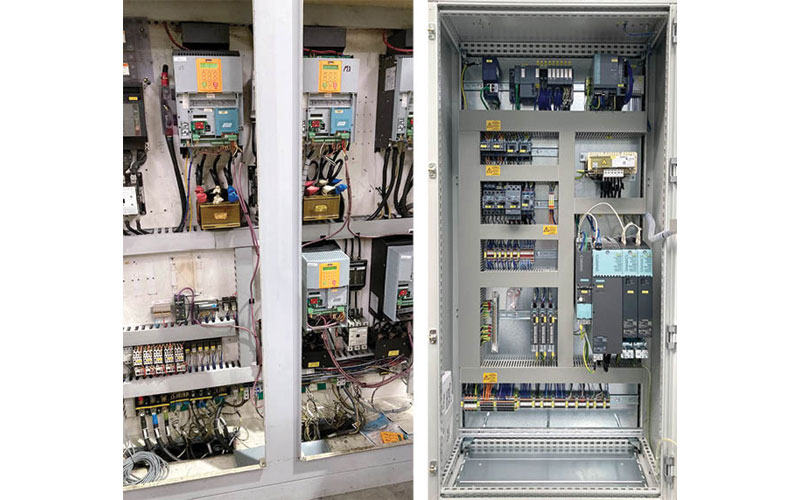
In mechanical and plant engineering, the term ‘retrofit’ refers to the modernisation of existing systems. The primary goal of a retrofit is to increase the profitability of older systems. These modernisation efforts often focus on electrical components, as the mechanical structures of many machines are highly durable and robust. In contrast, control systems are subject to significantly shorter life cycles. Once a control system is discontinued by the manufacturer, replacement components are increasingly difficult to source, leading to higher procurement costs and longer lead times. However, the available knowledge should not be overlooked in the economic feasibility evaluation. Experienced operators and service technicians familiar with older systems are becoming scarce, resulting in extended downtimes as new personnel must familiarise themselves with the equipment. These risks can lead to prolonged, unplanned production downtimes.
Watch: Top Cable Companies in India
In order to minimise the risk of failure and to ensure production capacity, regular checks of machine control systems, especially of older machines, are recommended. In addition to maintaining production capacity, modern drive technology also has a positive impact on energy costs, potentially reducing them by a double-digit percentage range.
FUHR GmbH & Co. KG, based in East Westphalia, develops and manufactures high-precision systems for producing profiled wires through cold rolling. The immense process forces occurring during cold rolling must be absorbed by the machine. This requires an extremely rigid mechanical structure that is virtually made for eternity. The electrotechnical components are not. However, this also gives the opportunity for an electrotechnical retrofit to operate the machines for decades to come and significantly reduce energy consumption. Such a retrofit often pays for itself within just a few years.
Assuming a rolling mill operating in three shifts has a drive power of 100 kW and a retrofit reduces energy consumption by 15%, this results in a daily saving of 360 kWh. With the current electricity prices, this can quickly add up to EUR 100 per working day.
Also Read: Wire & Cable India Emagazine Mar-Apr Issue 2025
Another critical aspect is machine safety. The operating company is responsible for the safety of a production plant. Even if the system was CE-compliant at the time of delivery, the operational safety must be checked regularly. If the framework conditions have changed, adjustments to the safety concept of the plant may also be necessary. FUHR GmbH & Co. KG is happy to advise its customers in all matters related to retrofit and machine safety.