Mr. Karthik Raman, Head of Product Management of Kennametal shared about “Digital Twin”, an innovative end-to-end solution-driven approach utilized by Kennametal to help customers solve machining challenges.
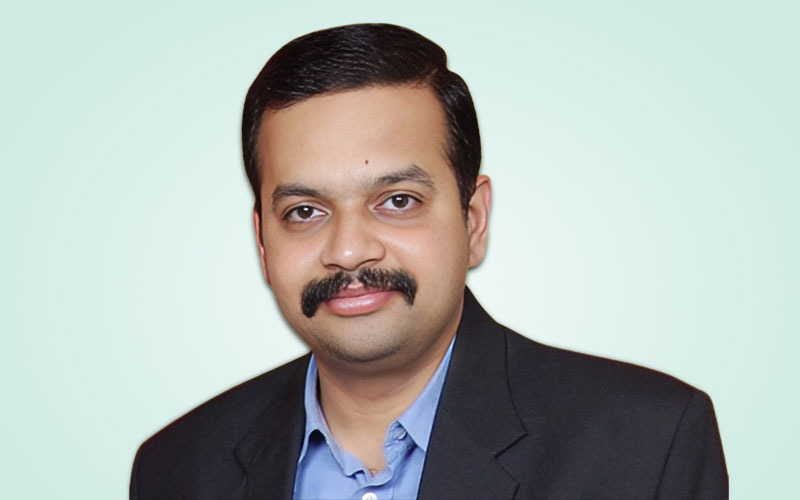
We live in a fast-paced world, one where new technologies are adopted faster than ever before. In manufacturing, specifically in in-part production, we’re observing a transformation due to the ever-increasing use of cloud-enabled, connected data platforms that aid high-volume transactions, interactions, and relationships from hundreds of data sources. These platforms also unify data from multiple standalone sources and present a comprehensive view to support real-time decision-making—today, more commonly referred to as Data-Driven Decisions (DDD).
Also evolving are customers’ machining requirements. Customer requirements can range from machining a complex 5-axis part with a high machinability index and tight tolerances to prioritizing the optimization of machining strategies to streamline processes, drive productivity, control cost, and reduce waste.
Watch: RR Kabel | Solar Cables | Solar Plant | Renewable Energy
To help customers solve machining challenges, Kennametal utilizes an innovative end-to-end solution-driven approach called, “Digital Twin”. Digital Twin is a blueprint for smart machining.
A “digital twin” is a virtual model that is designed to represent a physical object or product accurately and precisely in this case. It can be tested and validated before it is put into production and the market. A digital twin allows engineers and process planners to identify any process failures before the part goes into actual production.
Complex multi-axis machines require a deep knowledge and understanding of fixtures, cutting tools, and processes, as well as programming. Kennametal’s digital twin solution helps customers visualize the complete machining operation in a virtual setting with the right process parameters so that issues or adjustments can be addressed in the planning stages as opposed to later, potentially halting operations. Digital twin replicas also help translate machining results to performance by allowing for a precise estimation of chipping loss, cycle time, and executable NC codes.
With Kennametal and its blueprint for smart machining, customers can create custom tool path simulations and access the latest CNC programs for metal cutting tools and machining strategies, while continuing to deliver proven machining and manufacturing solutions. Kennametal can help take your manufacturing to the next level.