Leading manufacturers of world-class steel wires with an annual capacity of 1,80,000 metric tonnes and an INR 1,200 crore turnover, Nirmal Wires Private Limited (Group Nirmal) is looking forward to further its position as a holistic solutions provider in the wire and cable industry. This was revealed by Mr. Raman Saraf, Director, Nirmal Wires Private Limited (Group Nirmal), during his interaction with Wire & Cable India magazine.
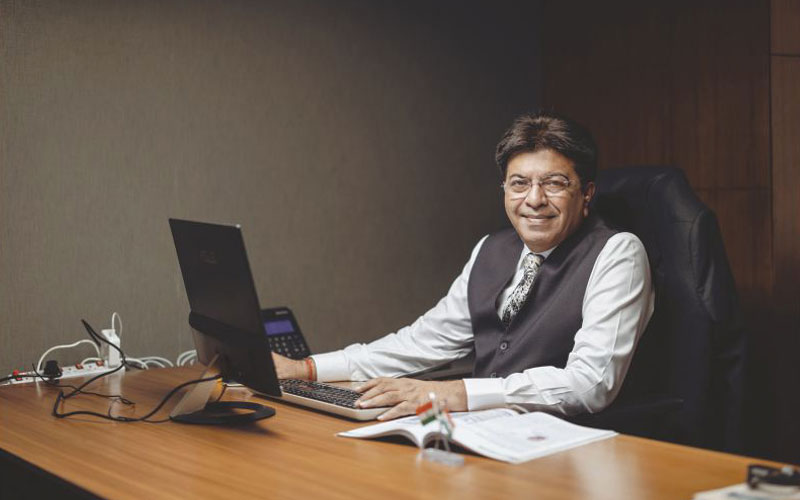
Wire & Cable India: Please share your views on the Indian vis-a-vis the global steel wire industry. What is the role of the Indian government in the growth of this sector?
Raman Saraf: On a global scale, India’s steel wire industry is distinguished by its resilience and adaptability in the face of fluctuating market conditions and evolving technological paradigms. As the world witnesses a paradigm shift towards sustainability and technological advancement, India’s steel wire sector is poised to capitalize on these trends through innovation-driven initiatives and strategic collaborations.
India’s resilience in adapting to market changes and embracing technological advancements underscores its competitiveness. The government’s strategic interventions, including the National Steel Policy and Production Linked Incentive scheme, have propelled domestic production and competitiveness. Additionally, infrastructure development initiatives and Make in India campaigns have spurred demand across sectors. Overall, the government’s supportive policies and conducive environment have positioned India as a key driver of growth in the global steel wire industry.
WCI: What are the major ongoing challenges in the Indian steel wire industry?
RS: Despite its promising trajectory, the Indian steel wire industry confronts several ongoing challenges. Foremost among these is the volatility in raw material prices, which can significantly impact production costs and profitability. Additionally, infrastructure bottlenecks, logistical constraints, and regulatory hurdles pose persistent challenges to seamless operations and expansion initiatives within the sector. Moreover, competition from cheaper imports, often subsidized by foreign governments, presents a formidable obstacle to the domestic steel wire market.
Furthermore, environmental concerns and compliance with stringent sustainability standards necessitate substantial investments in eco-friendly technologies and processes, adding another layer of complexity to industry operations. Overcoming these challenges demands a concerted effort from industry stakeholders, policymakers, and regulatory bodies to foster innovation, enhance competitiveness, and ensure the sustainable growth of the Indian steel wire sector.
Watch: RR Kabel | Solar Cables | Solar Plant | Renewable Energy
WCI: How can these challenges of the industry be addressed? How is your company contributing towards this transition?
RS: Addressing the multifaceted challenges facing the Indian steel wire industry requires a comprehensive approach encompassing innovation, collaboration, and strategic initiatives. Firstly, fostering closer collaboration between industry players, government bodies, and research institutions can facilitate the development of innovative solutions to tackle issues such as raw material volatility, infrastructure bottlenecks, and regulatory compliance. Secondly, investing in advanced technologies and process optimization can enhance efficiency, reduce environmental impact, and bolster competitiveness. Additionally, advocating for fair trade practices and addressing trade barriers to curb the influx of subsidized imports can safeguard the interests of domestic producers.
At Nirmal Wires, we are actively contributing to this transition through a three-pronged approach. Firstly, we prioritize research and development to innovate new products and processes that enhance efficiency and sustainability while mitigating the impact of raw material price fluctuations. Secondly, we invest in state-of-the-art infrastructure and technology to streamline operations, optimize resource utilization, and minimize environmental footprint. Lastly, we actively engage with industry associations and regulatory bodies to advocate for policies that foster a level-playing field and promote the long-term growth & sustainability of the Indian steel wire industry. Through these concerted efforts, we aim not only to address the challenges faced by our industry, but also lead the way towards a more resilient and prosperous future for all stakeholders.
WCI: Could you please take us through the business journey, milestones and achievements of your company?
RS: Our journey began in 1971 with Shri Ramautar Saraf at the helm. Fueled by the spark to create the best quality steel products in West Bengal, he established a small wire drawing unit under the corporate entity Central Store Supplies (P) Ltd incorporated in 1942. After many years of hard labor and facing multifarious challenges, he kept the flame alive. In 1985, he put up a steel wire galvanizing plant under the corporate entity Nirmal Wires Private Limited, incorporated in 1981.
He handed over the torch, kindled by him, to his sons Mr. Nirmal Saraf, Mr. Raman Saraf and Mr. Piyush Saraf. With the infusion of youthful energy, Team Nirmal knew no limits. In a few years, we had established a flourishing business in the steel products industry mainly steel wires and rolled products. The torch burning brighter than ever before was handed over to the third generation of leaders: Mr. Varun Saraf, Mr. Prateek Saraf, Mr. Vidyut Saraf and Mr. Parag Saraf. They have carried the torch far and wide and are now meeting customer needs in over 40 countries around the globe.
WCI: Brief us about your specialized products along with their USPs.
RS: We have an expansive product range of over 100 SKUs of different products including galvanized & black steel wires, ribbed steel wires, welding electrodes, aluminum conductors and hot rolled steel products. Some of our wires and their vast applications include wires for producing umbrella ribs, various types of springs, wires for earthing, staying, armoring of cables, and concrete reinforcement wires. These wires are used in transmission, distribution & generation of power, security & protection, fencing, general engineering, automotive, amongst others.
We stand out in the wire and cable industry as a holistic solutions provider. We don’t just guarantee product quality; we guarantee extensive after-sales service, and a robust customer feedback collection system to further our customer-first commitment.
WCI: What have been the recent developments at your organization and what are your future growth plans?
RS: Some of our recent developments have been the production line that was designed, installed, and commissioned in house for our newest product Niznal™, a zinc aluminium alloy coated wire, that redefines strength, durability, and reliability. It is a high-performance wire made from a special alloy of zinc and alumnium, which gives it superior corrosion resistance and durability compared to a traditional galvanized wire. It provides up to 6X longer life (as compared to a standard GI Wire) and therefore, lower product lifecycle cost.
We have recently launched our own line of cables under the brand name Nirmal Cables, as a forward extension of our existing line of conductor products. We are immensely proud of all the work put in by our technical team to successfully launch this product.
We have also launched ASTM class B & class C zinc coated wires. These provide a heavy coating of 850 gm with maximum durability and enhanced corrosion protection. These heavy coated wires are designed for use in harsh and corrosive environmental conditions (for example: salty & moist atmosphere near seashores). We have also developed high-speed wire drawing processes.
Future product offerings include zinc wires, zinc aluminum wires, low relaxation prestressed concrete wires and patented steel wires. Along with this, we are constantly working in R&D on ways to make our production process more sustainable, galvanizing without the use of acids and flux, and ways to increase efficiency and thus, capacity.
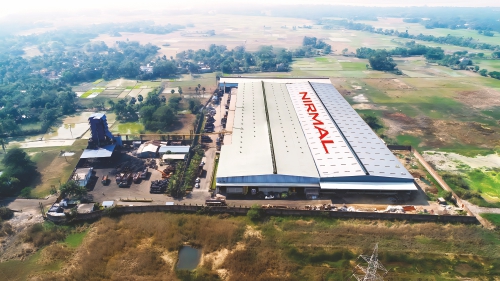
WCI: Describe your infrastructure and manufacturing setup for the steel wire sector along with their manufacturing capabilities.
RS: At Nirmal Wires Private Limited, our infrastructure and manufacturing setup epitomize excellence and efficiency in the steel wire sector. With five cutting-edge manufacturing facilities strategically located across India, we boast a combined production capacity of 180,000 metric tons per annum. Our facilities are equipped with state-of-the-art machinery and technologies, surpassing industry standards in terms of productivity and quality. Each facility is meticulously designed to optimize production processes, ensuring seamless operations and superior output.
Central to our manufacturing ethos is our unwavering commitment to quality assurance. We have established a robust quality control department staffed by seasoned professionals, who oversee every stage of the production process to maintain uncompromising quality standards. Our largest factory unit houses an extensive NABL-certified laboratory, equipped with cutting-edge instrumentation and testing capabilities, ensuring the precision and reliability of our products.
Furthermore, we have invested significantly in our packaging systems to ensure safe and secure transportation of our products to clients worldwide. Rigorous safety measures and inspection facilities are integrated into our factory infrastructure to uphold the highest standards of occupational health and safety.
Visit Stand: Hall 15 / B35 at Wire Dusseldorf