Joining the ends of strands and stranded conductors in front of the extruder is an important issue in cable production. The target is to select a quick, reliable and economic method to ensure continuous production.
Basically, there are two different methods to weld stranded conductors in front of the extruder.
1. Chamber welding method
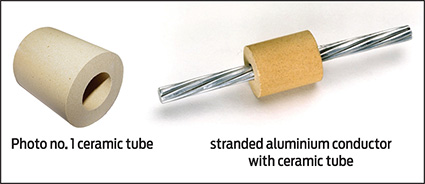
Here the joint is produced by resistance pressure welding in a tube (chamber), which is made of glass, ceramic or graphite. The choice of tube material is made depending on the strand or stranded conductor cross-section as well as the welder’s capacity respectively.
For welding the two stranded conductor ends, i.e. the end of the already running cable drum and the beginning of the new drum, are inserted into the tube (see photo no. 1) in such a way that the point of contact is in the middle. This assembly is then inserted into the formed grooves inside the welder’s clamping jaws and firmly clamped.
The point of contact of the two stranded conductor ends is brought to melting temperature via ohmic resistance when switching in welding current, and then the ends are pushed together and welded in the tube by the prevailing upset pressure. The material having become liquid is diffused evenly between the single wires forming the stranded conductor. After completion of the welding process the welded strand is unclamped and the tube is smashed.
On buttwelding machines designed for smaller strand sizes the material is upset via spring pressure as a rule, with the clamping devices being opened or closed via pedal for ease of operation – so the operator has both hands free to handle the strand ends as well as the tube (see photo no. 2 – type SE 1). For bigger stranded conductors clamping as well as upsetting is done pneumatically (see photo no. 3 – type SE 130).
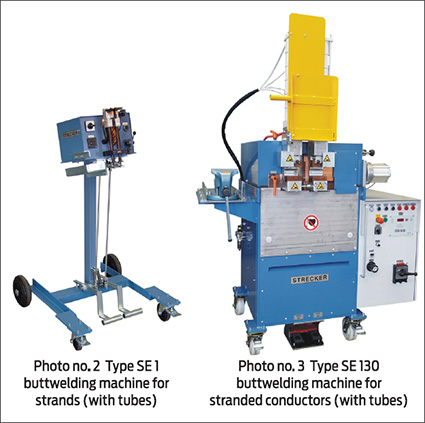
Once the welding process is completed, the surface of the welded joint is free of any burrs, clean, smooth and hardly bigger in cross-section than the original material (see photo no. 4). Generally, welds made by means of tubes require just a little refinishing (i.e. by filing), to make their cross-section which is slightly increased due to the process itself pass through the inlet die of the extruder without problems.
The chamber welding method is suitable for regular strand constructions as well as for fine-stranded, flexible stranded conductors as well.
2. Dual upset buttwelding process with automatic deburring
This welding method is applied most successfully to buttweld solid wires for decades already, but also for joining stranded conductors without any tubes it is a proven and well-tried process, even preferred by quite a number of reputable cable manufacturers.
Contemporary extruders (XLPE) are fitted with inlet dies, which allow no significant tolerances in outer diameter of the stranded conductor. At the same time these lines work with short processing time. As a result there is the necessity to produce within the shortest delay possible welded joints of identical outer diameter compared to the original stranded conductor. Furthermore the welds must be safe and reliable, i.e. the first weld already must succeed optimally so the extruder’s storage won’t run empty.
These requirements can be conditionally fulfilled by buttwelding machines working according to the chamber welding method only. All the more as the individual operator’s correct handling of the complete process has an important impact on the success of the weld.
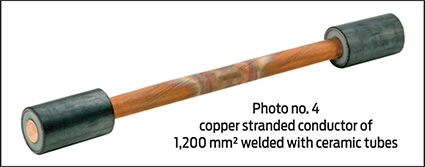
When releasing a dual upset buttwelding process with automatic deburring, first the point of contact of the stranded conductor ends is brought to the required welding temperature with low pressure (welding pressure) only. Once the material has become liquid, high pressure (upset pressure) is switched in and presses out of the welding zone all heat-influenced material, leaving just very few tenths of a millimeter in the welded joint. The stranded conductor’s flexibility is influenced negatively in this rather short area only. Welding electrodes are fitted with knife-shaped inserts, which immediately after the process shear off the welding burr produced during the process. The still closed burr ring is torn apart when opening the clamping device and falls off. All motions, e.g. clamping as well as upsetting and deburring are fully hydraulically activated.
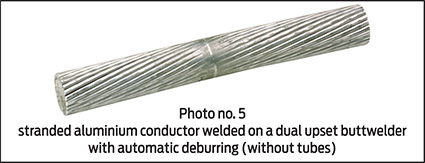
The weld is identical in diameter when compared to the unwelded original material (see photo no. 5), with a welding zone that is much shorter than on welds made according to the chamber welding method.
Welding time is very short, too: a weld on stranded copper conductors 1,200 mm² will only take up to max. 30 seconds when using a dual upset buttwelding machine with automatic deburring type MK 800 (see photo no. 6).
Another, positive side effect on dual upset buttwelding machines with automatic deburring: no running costs for purchasing tubes as so-called consumable items, no need to keep them in store.
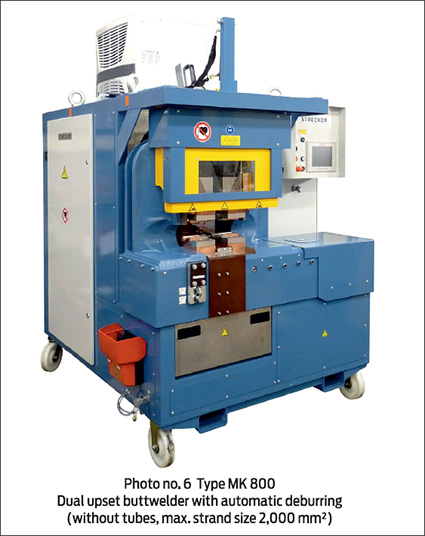
Dual upset buttwelding machines with automatic deburring are the optimum solution for joining regular stranded conductors, however, cannot be used for fine-stranded flexible conductors.
As a result of recent developments, now it is possible to offer buttwelding by medium frequency working at abt. 1,000 Hertz, with 3-phase current supply. So there won’t be a single phase load of the mains supply anymore. The amperage absorbed during a welding cycle is reduced substantially, e.g. divided by two approximately. As a result, fuse protection is facilitated in particular for bigger buttwelding machines having a capacity of 100 kVA or more (mains fuses, often a transformer is installed exclusively for the buttwelding machine).
Medium frequency technology is not limited to new machines only, but it is also possible to modify existing machines.
The article is authored by August Strecker GmbH & Co. KG